Paving The Way For Greater Control
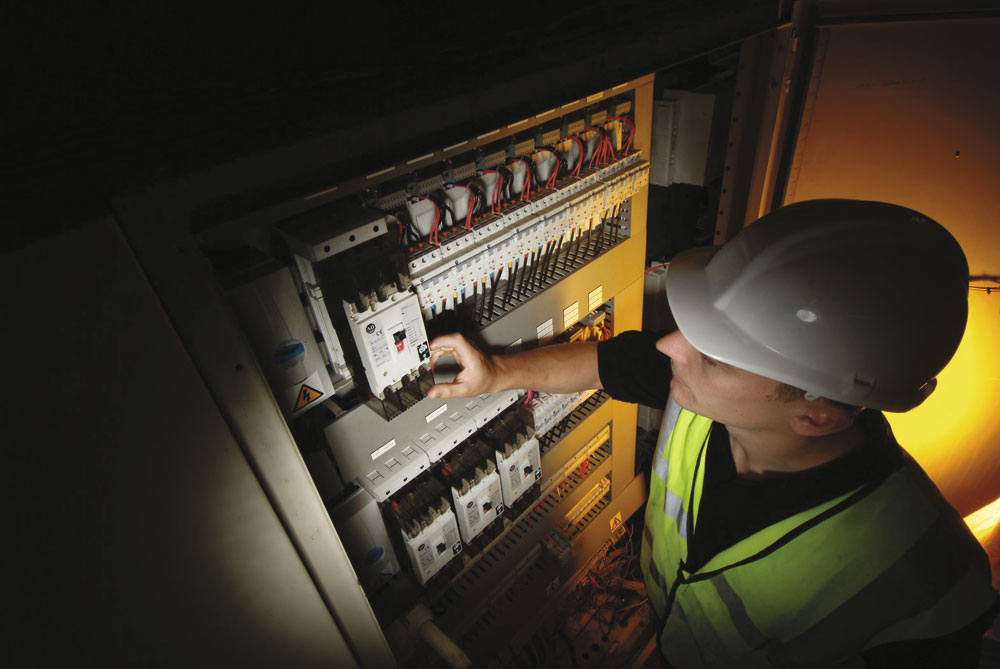
Engineers from Batching & Blending Systems help increase reliability at RMC’s Washwood Heath depot by installing a comprehensive plant control system
Last year RMC Aggregates, specialists in the production of asphalts and bituminous macadams, began a major refurbishment programme to replace the ageing control system at their Washwood Heath depot in Saltley, Birmingham, and approached Batching & Blending Systems Ltd (BBSYS) for a cost-effective solution.
The depot — part of a national network of 129 quarries and 49 asphalt plants — is in constant operation throughout the year and is home to both an asphalt plant and a batch-heater plant, fed by a swing-chute cold-feed system. Each year over 180,000 tonnes of asphalt are produced at the 4-acre site.
The existing control system had become unreliable and outdated, with the control gear worn and liable to failure, resulting in downtime and lost sales. High Wycombe-based BBSYS, in conjunction with RMC engineers, decided that the plant’s first major electrical upgrade since its opening in 1986 should include Rockwell Automation’s Allen-Bradley equipment.
‘The original switchgear was installed almost 18 years ago and was in a pretty bad state,’ said Roger Hill, director of BBSYS. ‘Standards have changed a lot since 1986 so we needed to upgrade to something that was easy to install, configure and commission. Cumulatively our engineers have been involved in more than 200 projects at coating plants, and Allen-Bradley is widely accepted as the benchmark in the quarrying industry. It was ideal for such a complex turnkey project.’
It was essential that the work was carried out quickly so that the plant could resume production as soon as possible. The retrofit project would normally have taken several weeks to complete but contractors were allocated only 10 days to finish the installation; a deadline that would have been almost impossible using conventional equipment. ‘The reputation of the plant is hugely important,’ said Al Laverty, commercial manager of RMC Aggregates Western. ‘You’re only as good as your last delivery and you’ve got to make sure you can maintain a good level of service to your customers. The equipment had to be installed quickly to minimize downtime.’
BBSYS specified a Rockwell Software RSView32 SCADA system and a range of Allen-Bradley equipment including SLC500 PLCs, SMC-Delta soft starters, a 141A busbar system and Powerflex 700 inverter drives. The integration of starters, PLCs and software provided RMC with a comprehensive and future-proof control system that could be monitored from computer terminals throughout the site.
SLC500 PLCs are fitted in a new control room and linked to six remote I/O racks mounted in each of the switchgear panels. Allen-Bradley SMC-Delta soft starters replace existing Star Delta equipment, and the 141A busbar mounting system allows engineers to use hot disconnections if anything fails; this means that faulty components can be replaced within minutes rather than hours.
‘There used to be a substantial amount of downtime because you had to wait until the entire plant was out of action before you could isolate the panel,’ said Mr Hill. ‘With the new equipment you can change a motor starter without shutting everything down. An electrician had to regularly attend the site when there was a problem but they don’t need to do that now. This also helps to keep costs down.’
Powerflex drives installed on the exhaust fan systems in both the asphalt plant and the batch-heater plant achieve the greatest savings. Rated 110kW and 55kW, respectively, the drives help reduce energy consumption, noise pollution and maintenance costs.
By varying the speeds needed to control the fan motor’s suction within the dryer drum, RMC expect to save around £10,000 annually with payback expected within two years.
But it is Rockwell Automation’s complete ‘integrated architecture’ approach that has most increased productivity and flexibility at Washwood Heath, by allowing the entire system to be monitored and accessed from a standard desktop PC.
A state-of-the-art control room in the main building now houses two computer terminals, with RSView32 software providing complete access to the asphalt and batch-heating plants. ‘The system used to rely on push-button controls in a Portakabin overlooking the site, but we’ve now taken the control room back into the offices,’ said Mr Hill. ‘Staff are now in a far more comfortable, cleaner and quieter environment, and effectively one operator can now control both plants.’
Full-colour TFT monitors display the entire process graphically and allow operators to check recipes, colourings, weights and temperatures. Staff can see how much asphalt is being produced, whether the plant is maintaining its efficiency and, if any problems arise, exactly where faults have occurred.
‘Quality control has vastly improved since the installation, with more accurate weighing technology and a reduction in waste. Not only that, but with the new system each operator is accountable and every batch is traceable,’ he said.
A password-protected 40GB database stores records dating back several years–essential for keeping the site running smoothly and ensuring quality control. Stocks are constantly monitored and all activities logged, which makes fault-finding and maintenance far simpler than before. Mixes, weights and timings can also be pre-programmed and stored as recipes –capturing when the machinery is operating at its peak and allowing staff to reproduce identical results at the touch of a button.
‘These changes have brought us into the 21st century,’ said Mr Laverty. ‘The old system had seen better days, it was hard to maintain and spare parts were difficult to source. Reliability is now very good.’
The upgrade has helped RMC to maintain their position in a highly competitive industry and to meet strict quality-control standards and health and safety regulations. Following its success, Batching & Blending Systems have already started to plan their next projects.‘
A job of this size and complexity is bound to have a number of hurdles — it’s all about how you get over them,’ said Mr Hill. ‘Rockwell Automation have been a lifesaver on this job, especially with such a tight time frame. We helped maintain the reputation of the plant through the reliability of the Allen-Bradley hardware and we have had no problems at all. We’re now looking at similar improvements at another five sites.’