Load-Out And Dosing Control Systems
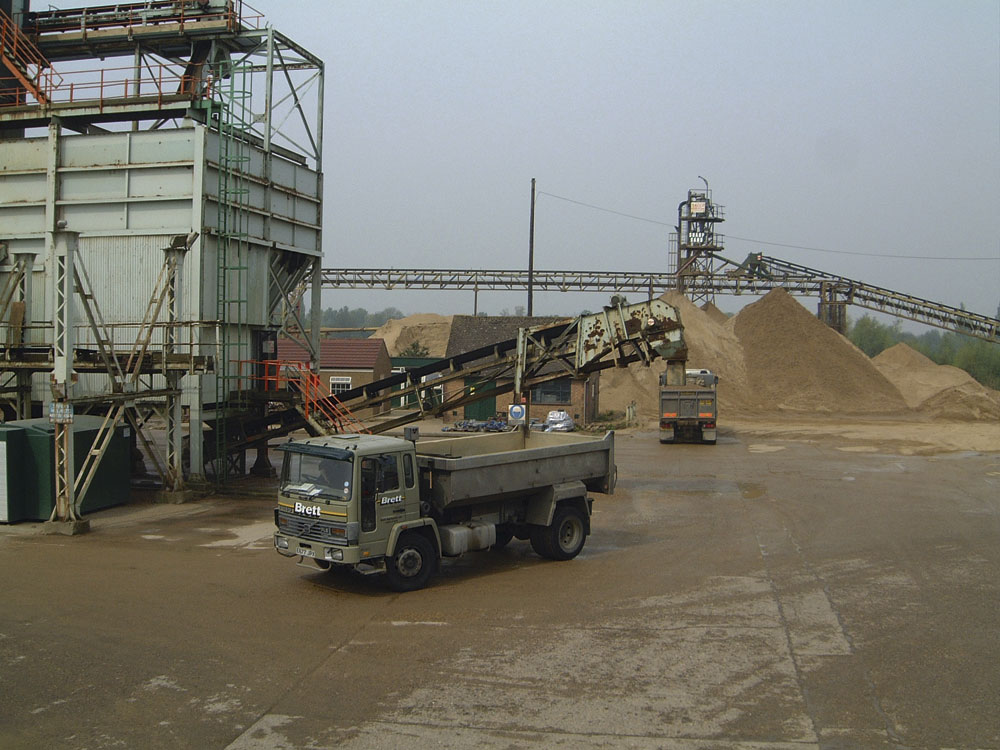
By Jon Scarrott of Lodestone Electronics Ltd
There are many techniques used by industry to load bulk material from storage bins into lorries, trains, dumptrucks and other vessels. Some use volumetric methods but for a high level of accuracy weighing is usually involved. The type of system selected depends upon a number of factors, such as the required load accuracy, the residence time of lorries in the dispensing area, or whether the load-out system is driver operated or operator controlled.
Volumetric load-out
Probably the simplest and cheapest technique is the use of slide or clamshell gates beneath a storage hopper, in conjunction with a timed gate controller. This type of system depends on the flow of material in the load-out vessel being consistent, such as a graded single-size material. Moisture and seasonal variations can affect the consistency so constant calibration checks may be required. Calibration is generally straightforward, however, as the lorries can usually be check weighed on a weighbridge after loading. The required frequency of calibration checks will quickly become apparent in most situations.
In order to calibrate a volumetric system an amount of material instigated by the system is discharged into a dumptruck from the load-out point and a timer in the system is started. The timer is stopped when the material feed has ceased. The material is then taken away and weighed and the weighed value is entered as the weight calibration value in the controller. From this information the system can calculate any discharge amount from the dispensing system. It is generally repeatable to within 5% of target and the set point can be adjusted by the driver/operator as required. A display gives target load and time to load completion. Calibration information should be password protected as this information is entered into the system via the operator’s console.
Errors with this type of system usually occur when the material type in the dispensing vessel is changed or the flow characteristics vary due to low volumes of material in the hopper or changes in moisture content.
Material dispensed by a volumetric system would normally only be used within its own environment, for example dumptrucks taking material from a silo to a coating plant or other similar application.
Static weigher load-out
A static weighing system offers the best level of accuracy. One particular system supplied by the author involves the collection of offcuts from a number of steel presses on to a conveyor system for transport to a weigh hopper. When the load in the hopper reaches a pre-defined set point, the hopper automatically discharges into a waiting lorry. In order to distribute the load correctly a number of discharges are initiated, allowing the lorry driver to move his vehicle in order to even out the load. Once the correct load has been received an alarm is sounded to indicate that another lorry is required. A display indicates the progress of the loading cycle. This loading process can take place continually up to 24h a day and, as there are no tip-off or top-up facilities on site, the weighment has to be consistently accurate.
Dual-hopper weighing system
Other systems, such as dual-hopper static weighing systems, are available but tend to be relatively expensive. This technique involves the loading of one hopper while the other is weighing and discharging. Generally, the hoppers are fed via a bifurcated chute with a divert flap. Depending on the material involved, this can be a source of high maintenance and wear. If properly designed, however, this type of system can give a continuous discharge of material into the receiving vessel and can be very accurate. Calibration is relatively simple using static weights. These can be attached to each individual hopper and placed on the hopper either electrically or via a manual lever system. Although technically this is a continuous weighing system, it uses static weighing techniques and is sometimes used for batching into larger vessels, such as train load-out systems and blast-furnace charging systems.
Simple static batching systems
Some static weighing systems simply weigh in the required materials and discharge the entire vessel when the set point is reached. One advantage of this method of weighing is that multiple ingredients can be added to the same vessel using multiple set points in the weighing controller or SCADA control system. The amount of each ingredient can be stored and printed out or sent to a data-logging system for future analysis. The system also monitors the overall progress of the batch. This can be done either manually or by a continuous automatic batch system. Generally this type of batching would be interfaced into a plant control SCADA system or other PLC-type control application.
Errors with this type of system are generally caused by seasonal variations, for example temperature changes causing the structure to move, windage etc. Hoppers sited within a building usually give the best results.
Loss-in-weight controllers
The loss-in-weight controller works like a static weighing vessel mounted on load-cells but with the added functionality of being able to integrate the discharge of material with time. The loss-in-weight controller not only indicates the amount of material being discharged, but also its rate in weight per unit time, such as tonnes/h or kg/s. This information can be valuable when integrating the controller with a proportional dosing system, eg delivering the correct ratio of cement to sand using a PID controller. The cement stream is generally fed via a screw feeder in order to prevent flushing.
As the weight output is absolute the weighment generally has an accuracy greater than 0.2%. The main source of error with this type of system occurs during the fill cycle. As weighment cannot be made when the vessel is filling an assumption has to be made and the last value before the fill cycle commenced is retained and used by the system. It is therefore necessary to fill the system as quickly as possible and to ensure that the material has settled before weighing is restarted. The best technique is to stop discharging while the weighing vessel is filling, although this is not always possible.
Load-out systems using belt weighers
The most common type of load-out control system involves a load-out vessel feeding on to a conveyor and then into a target vessel, lorry, train, dumptruck etc. A belt weigher measures the flow of material from the dispensing vessel and the information from the belt weigher is passed to the load-out controller, which starts and stops the feed as required by reading the required tonnes and acting accordingly. With most systems of this type in-flight material compensation will be required owing to the distance from the belt weigher to the discharge point. This value is a parameter set at the time of calibration. The in-flight material is determined by setting the in-flight value to zero and the set-point controller to a required amount, and then weighing the load. The difference between the required amount and the actual amount delivered is the in-flight material value. This becomes more complex when dealing with multiple feed points. Generally, each feed point will need to be calibrated against the belt weigher and its in-flight value determined. Depending on which feeders are selected, the controller needs to be able to determine which in-flight values to use. This is generally done by digital inputs to the controller.
There may also be a requirement for accurate material sandwiching in applications such as asphalt production on continuous drum-mix plants. Selecting the relevant feeders is carried out on a time basis, the furthest feeder starting first with the other feeders starting sequentially after the required amount of time. A reverse action is required when stopping the feed.
In order to achieve more accurate loading a trickle feed can be introduced. This allows the bulk of the load to be delivered quickly until a predefined point in the loading cycle is reached, at which point the rate of feed is reduced until the set point is reached.
Sophisticated load-out using weighbridge feedback and lorry tagging
During the past 20 years or so, with the advent of powerful PCs and super quarries where traffic volumes can be very high, automated systems have been introduced to maximize the throughput of traffic. The need to eliminate the time wasted during topping-up and tipping-off is paramount to these types of operations. Also, systems of this kind offer vital management information, such as lorry residence time in the system and a host of other powerful data.
In a quarry environment, a lorry entering the site is tare weighed and the driver presented with a rugged card or ‘tag’ similar to a credit card. Magnetic swipe cards would not last long in a quarry, so inductive identity cards and similar non-contact type cards are used. When the card has been issued the driver is entered into the system and is effectively ‘tagged’. This ‘tag’ contains the driver’s details, the required load, the type of material required, and the time and date this was entered into the system. The driver then proceeds to the load-out point to await his turn for loading, at which point the card is presented to a reader and the driver is directed to the correct loading point by means of a traffic-light system. A series of sensors tell the control system when the vehicle is in place. The driver then presents the card to another card reader in the load-out bay to confirm that the lorry has arrived at the correct load-out point and that load-out can begin. The driver can start and stop the load as required via a local control panel. When the load is complete, the driver returns to the weighbridge to get his ticket. The weighbridge operator uses the same card to call up the lorry’s details and create the invoice. Cards can be dedicated to frequent users to save time on data entry.
During the loading process, the system keeps a record of each weighment from the belt weigher on the load-out conveyor. When the weighbridge weighs a particular truck, it sends this information with its tag back to the load-out controller, which in turn checks and, if required, adjusts the load-out system to comply with the weighbridge value. It is assumed that the weighbridge, being the point of sale, is the most accurate of all the weighers, hence the load-out control system is continually checked against the site weighbridge. If a single size has been dispensed, individual feeders can be adjusted accordingly.
For maximum accuracy each feed point should have its own feeder weighing system. This generally consists of a hopper with an extractor weigh feeder beneath it. Using this technique each feeder can be individually calibrated and controlled with far greater accuracy than volumetric feeders, each feeder having its own control loop. The actual load-out belt weigher on the feed line to the lorry should be a multi-idler system for the highest possible accuracy and repeatability.
Data interfacing
The transfer of information from site to company headquarters and to other relevant personnel can be of great importance for invoicing and production purposes. Some companies use dedicated modem lines to transfer such data, while others continue to rely on the well-tested method of filling in paper forms on site and sending them by post. With the advent of the Internet, data can now be transferred very efficiently from site to anywhere in the world. Relatively simple systems are available for extracting relevant information, either on request or on a timed basis, and sending it to its destination.
Data logging
Data logging to a memory stick has also proved popular. The memory stick can be removed and the data downloaded into a PC and analysed when convenient. This can be displayed in graphical format or as a spreadsheet, all at the click of a button. Data security using this method is also very high and can be preferable to sending the information over the web. Once the data has been recovered it can easily be emailed. Depending on the sample rate and the storage capacity of the memory stick, up to 12 months’ information can be stored in this way. If the data exceeds this, the oldest data is overwritten.