The Road To Sustainability
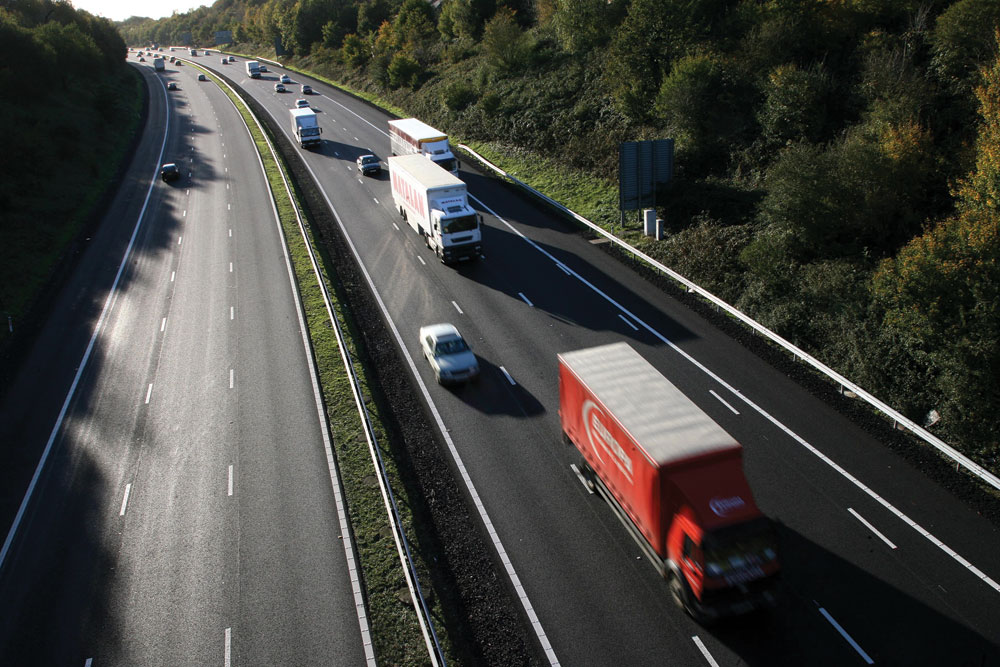
The bitumen market and the requirements of bitumen customers are changing, and the industry must adapt to meet its customers’ future requirements. One such requirement is the closing of the materials cycle by using a recycled asphalt planing (RAP) content when replacing old porous asphalt surface course. Phil Shirley investigates
Last year CEMEX worked closely with BP Bitumen to successfully deliver the first major contract in the UK for the recycling of existing road surface course into a new surface course. The £1.3 million contract, carried out on part of the M4 on behalf of the Welsh Assembly Government, achieved a recycled asphalt planings (RAP) content of 25%, and a share of the success can be attributed to the use of Olexobit 50 polymer-modified bitumen (PMB).
‘Olexobit binder was selected by CEMEX because of its unique proven pedigree in the UK and across Europe,’ said BP Bitumen business development manager Gareth Evans. ‘We also provided mixture evaluation and optimization advice to CEMEX, which made a significant contribution to the successful outcome of a very important project.’
The work on the M4 has placed CEMEX at the forefront of the growing market for reusing worn-out road surfacings. Some of the early porous asphalts and thin surfacing systems, the so-called ‘modern’ or ‘negatively textured’ surfacings, are now reaching the end of their design life, creating a potentially huge market to recycle these premium materials, which typically contain over 70% of high-PSV coarse aggregate, and put them back as ‘new’ products.
‘When porous asphalts were originally installed in the UK in the 1990s they were expected to last about eight years,’ Mr Evans added. ‘In reality, and despite hugely increased traffic volumes, those produced with Olexobit PMB have endured for over 10 years, which is proof of the performance capability of the binder – this product has really earned its reputation as the preferred PMB for porous asphalt and thin surfacings.’
CEMEX completed the groundbreaking project at the end of August 2006 over a 5km section of the M4 between Junctions 32 and 33 near Cardiff. This section carries a lot of heavy traffic resulting in the old porous asphalt surface course, which was originally produced with Olexobit 100 PMB, needing replacement after 12 years of use.
The old surface was a 50mm thick porous asphalt surface course containing a large proportion of –20mm high-PSV coarse aggregate. This mixture, unlike hot-rolled asphalt with chippings, is good for recycling into a new ‘modern’ surface course.
The work was carried out over a six-week period, at night and one lane at a time, to minimize traffic disruption. Between 400–600 tonnes were planed off each night and replaced before reopening to traffic in the morning.
The road was planed to a depth of 50mm and the planings were taken to CEMEX’s Wenvoe Quarry for crushing and screening. The processed planings were then transported to the company’s Forest Wood asphalt plant where a new thin-surface course (Viapave Type R) was produced with a 25% RAP content. Viapave Type R is a nominal 14mm aggregate, high-PSV thin-surfacing system which, for this section of the M4, was produced with Olexobit 50 PMB and laid at a nominal thickness of 50mm.
Normally RAP is only added to base and binder courses, and the RAP content of these mixtures is usually only 10–15%. Most planings do not contain enough coarse aggregate of a suitable size and PSV for recycling into surface courses. Also, higher addition rates require special measures to dry and heat the RAP and to remove the steam that is generated. On this contract, the processed planings contained plenty of coarse high-PSV aggregate and were added partly to the drier and partly to the mixer to facilitate the manufacture of the new surface course.
The Welsh Assembly’s demand for 25% recycled material is at the upper end of what can be achieved without major plant modifications. It is anticipated that the industry will see more and more of the modern high-PSV surface courses being recycled back into new surfacings.