The Road to Net-Zero Asphalt
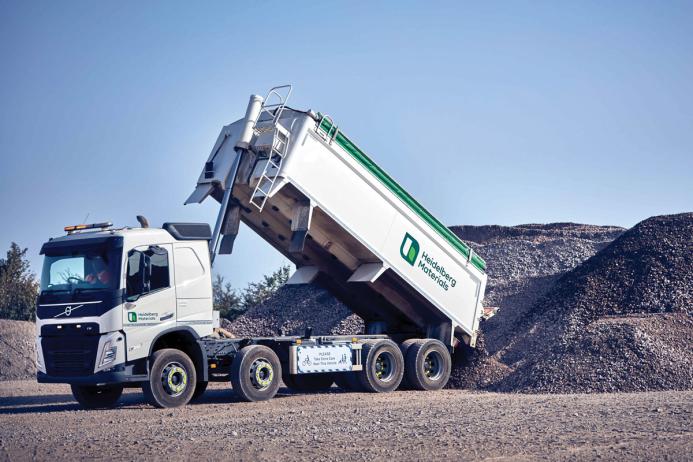
First published in the January 2024 issue of Quarry Management
The asphalt industry is making great strides in its efforts to help the UK Government, National Highways, and local authority highways teams meet their net-zero ambitions. Gareth Day, asphalt and contracting managing director at Heidelberg Materials UK, looks at the innovations being used today and some possible future steps
Asphalt is already one of the most sustainable construction materials available: it is extremely durable and 100% recyclable, with worn-out surfaces able to be reused in new asphalt, which may also contain other recycled content as well as secondary materials.
The embodied carbon per tonne of asphalt is typically between 40kg and 75kg, dependent on the type of asphalt, raw materials, transportation, and production process used. Of these, production emissions – the energy and raw materials used – are by far the largest contributors, with emissions associated with laying the asphalt only around 4–6% of the total embodied carbon of the finished material.
These production emissions can be reduced in several ways, including:
Optimizing the supply chain by, for example, delivering aggregates by rail rather than road
Reducing the moisture content of aggregates (at source and through covered storage)
Upgrading to modern, efficient burners
Switching to lower-/zero-carbon fuel sources, including hydrogen
Producing asphalt at lower temperatures
Eliminating waste in the asphalt production process
Increasing the percentage of recycled asphalt planings (RAP) within the mix
Using lower-carbon bitumen or bitumen substitutes
Designing asphalt with long-term durability in mind.
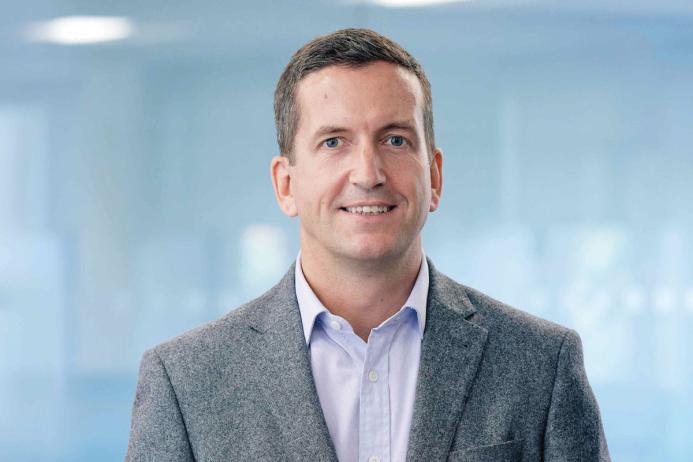
Reducing production temperature
It is well recognized that reducing the temperature at which asphalt is produced – and thereby reducing energy consumption – can have a meaningful impact on emissions.
Warm-mix asphalts (WMAs) are produced using special techniques and/or additives to reduce the production temperature to between 1,000°C and 1,600°C, compared with up to 2,000°C for conventional hot-mix asphalt products.
The use of WMAs is gathering pace, helped by the announcement from National Highways in 2019 encouraging its use as standard on the strategic road network, but the reality is that only a small proportion of total asphalt production volumes are WMAs, presenting a sizeable opportunity for carbon reduction from a technology that is already proven and readily available.
In addition to WMAs, half WMAs and cold-mix asphalts offer the potential for significant carbon reduction. Half WMAs typically reduce manufacturing temperatures to around 1,000°C through the use of micro-foaming techniques, whilst cold-mix asphalts are produced using emulsion-based binders which do not require heating but have more limited applications.
Typically, WMAs can cut 2–4kgCO2e/tonne of asphalt produced, while half WMAs can cut 12–14kgCO2e/tonne, and cold-mix asphalts 24–26kgCO2e/tonnes when liquid fuels are used.
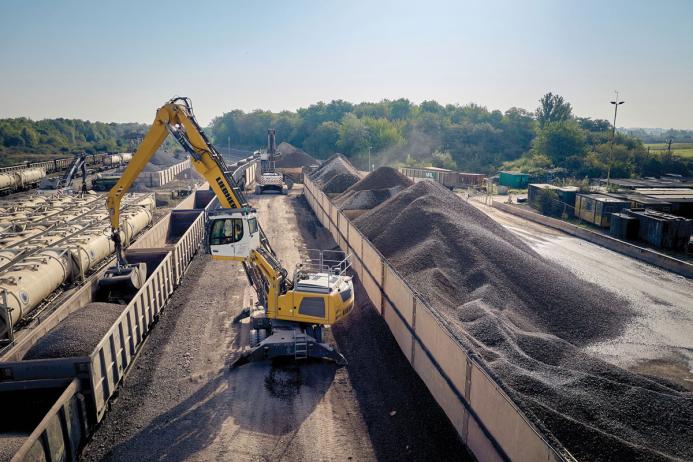
Alternative fuels
Emissions from the fuel used in production are a large factor and these can be almost completely removed by switching burners and mobile plant to a net-zero fuel mix by using hydrogen.
With this in mind, a demonstrator project using nuclear-derived hydrogen is being trialled at Heidelberg Materials’ Criggion asphalt plant in mid-Wales, in collaboration with EDF. The project, which has been awarded £6.1 million of funding from the Department for Energy Security and Net Zero, will use hydrogen created at EDF’s Heysham 2 power station, in Lancashire, to fuel the industrial processes at the plant, replacing the existing mix of liquid fossil fuel. This is likely to be one of the first times hydrogen has been used to produce asphalt on an industrial scale in the UK.
In addition to these production emissions, there are those generated in the transportation of raw materials to asphalt plants, the delivery of asphalt to site, and by the plant used for laying. Rail distribution of aggregates, for example, can reduce carbon emissions by 76% compared with road transport, and switching to lower-carbon fuel sources – such as using electric or hydrogen trucks – can also cut almost all transportation emissions.
Emissions generated from pavers and rollers can also be significantly reduced using hydrotreated vegetable oil (HVO) and gas-to-liquid (GTL) fuels. For example, Heidelberg Materials’ pavers and rollers use GD45+, which reduces CO2 emissions by more than 40%, as well as cutting NOx by 14% and releasing 18% fewer fine particles compared with traditional diesel.
Materials innovation
Collaboration between asphalt manufacturers and their supply chain has driven a wide range of process and product innovation to help reduce carbon emissions and create a more resilient road network.
Among the latest to gather pace are ‘biogenic’ asphalts which contain natural, responsibly sourced, biogenic materials within the bitumen content of the asphalt, which absorb and store CO2 throughout their life. This CO2 is then ‘locked’ within the asphalt and not released back into the atmosphere – even when the asphalt is recycled.
The construction industry is moving towards a circular economy with new products containing more recycled content, while still being fully recyclable at the end of their life. Using RAP avoids the use of primary aggregates, and asphalt containing waste glass or plastic can provide a beneficial use for the materials at the end of their life.
Cold recycled bound material (CRBM) allows a high percentage of recycled content to be used in the mix – up to 100% in some cases – and, as the name suggests, is produced cold, minimizing production emissions. These materials are usually produced on site, removing any carbon impact from transportation, and are laid by conventional paving equipment.
CRBM can also include tar-bound planings, which are classed as a hazardous waste, removing the cost and carbon implications of sending them for processing or to landfill.
Whole-life carbon emissions
Considering the embodied carbon of asphalt at the point of production and laying only tells one part of the story. There are almost 250,000 miles of road in Great Britain – as well as car parks, runways, driveways etc – that need to be maintained. So, reducing the number of interventions is an important driver as it will lead to the use of less materials, cut waste, and reduce whole-life carbon emissions.
The asphalt industry recognizes the role enhanced material durability can play in minimizing interventions, and anti-ageing polymer-modified bitumens (PMBs) are key in this area. Long-life PMBs can reduce the premature hardening of bitumen that occurs through its chemical reaction with the oxygen in the atmosphere, improving flexibility, strength, and resistance to fatigue and deformation, and extending the life of the asphalt. They can also include biogenic material and other additives that can further reduce embodied CO2.
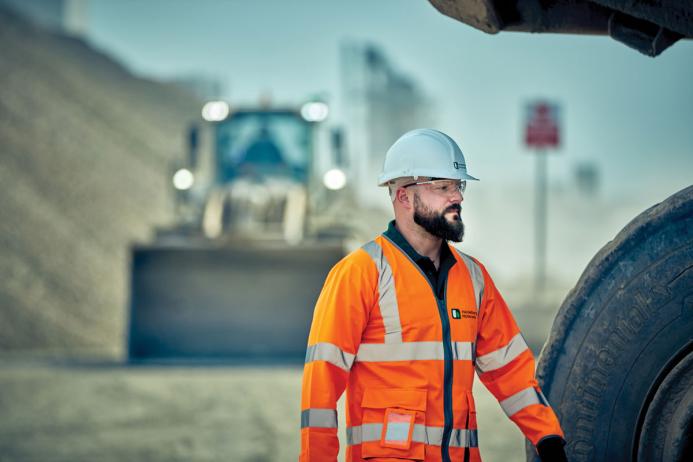
Looking to the future
In the longer term, the industry will need to embrace new, lower- or zero-carbon fuels, such as hydrogen, as they become available. We will also need to continue to inform our customers about the lower-carbon options available and bust some longstanding myths about the durability and workability of some lower-carbon/high recycled content products.
In addition, customers will need to evaluate trade-offs between carbon emissions and cost – such as where innovative lower-carbon materials cost more to produce – and between source and lifecycle emissions, for example, where the time between interventions can be extended for a smaller up-front increase in carbon emissions using long-life or PMB bitumen.
Early involvement and collaboration with the supply chain will allow projects to be designed to use lower-carbon and recycled materials to create a more resilient road network. And, to meet ambitious net-zero targets, we need to work together to share successes and champion innovative new methods of road design and construction.
Subscribe to Quarry Management, the monthly journal for the mineral products industry, to read articles before they appear on Agg-Net.com