The Case for Surface Dressing
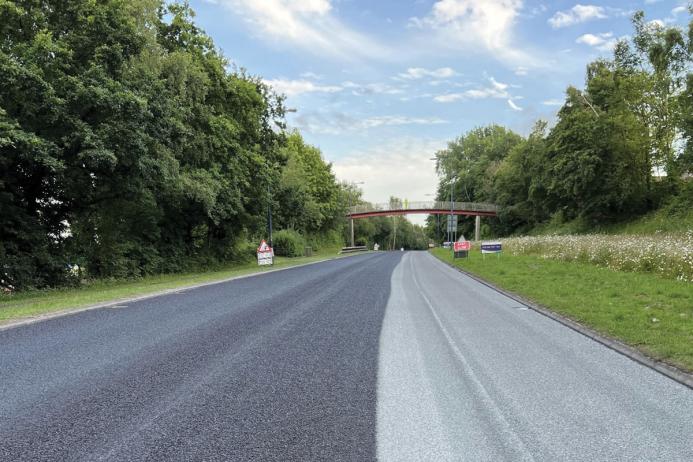
First published in the January 2024 issue of Quarry Management
Keeping local roads safe, without costing the Earth: A joint paper by the Road Emulsion Association (REA) and the Road Surface Treatments Association (RSTA)
Local authorities have a statutory responsibility to ensure that their road networks are in a safe and serviceable condition. At the same time, there is mounting pressure on local authority highway engineers and asset managers to optimize the use of allocated highway maintenance funding; deliver value for road users and taxpayers more generally; and minimize costs (both financial and non-financial), risk, and environmental impact.
Planned, preventative surface dressing treatments must be considered as a highly advantageous solution in this context.
Ninety-seven percent of the road network in England and Wales is maintained by local highway authorities. It is an asset valued at more than £400 billion, and the biggest physical asset owned by the public sector.
The local road network is fundamental to economic growth and prosperity – connecting communities, workers to jobs, and businesses to consumers – and to unlocking new investment and development opportunities.
The future of transport infrastructure will also see roads play a vital role in supporting the mass adoption of green and smart transport, both in terms of private vehicles and heavy goods/logistics fleets, as well as low-carbon alternatives such as cycling. This includes the transition to net-zero highways[1].
Success, however, will be dependent on asset managers taking the strategic decision to prioritize long-term resilience, lifetime value, and proactive, preventative interventions.
A long-term approach is needed
Many years of under-investment in highways, and a reluctance (or inability due to the funding decision-making process) to pursue maintenance policies with a multi-year horizon, have resulted in a road network which is struggling to cope with user demand and climatic change.
Pothole repairs are extremely expensive and disruptive to the UK taxpayer. A pothole is filled every 22s, at a total annual cost of £93.7 million in 2022/23[2]. Repairing a significant number of potholes is not a sign of success, but a sign of failure.
The allocated pothole repair fund provided by central government has been and gone, and yet more than 1 million potholes are still being repaired each year. Why?
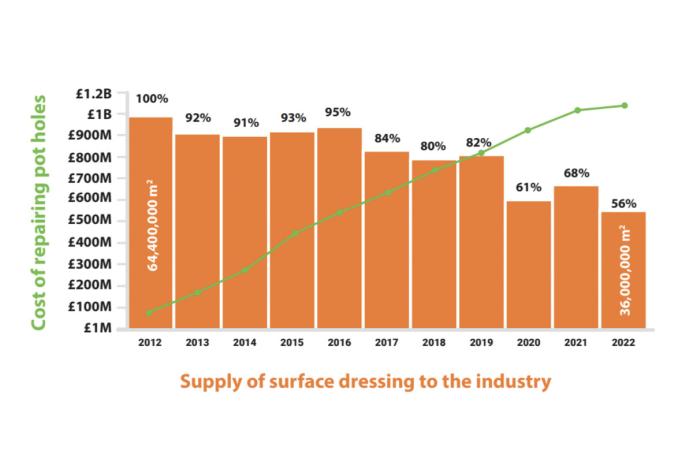
According to statistics from the Department for Transport (DfT)[3], the percentage of roads (A, B and C) receiving surface dressing treatment has declined by 30% since 2016. This is mirrored by feedback from REA members who report a 36% decline in the application of surface dressing – and an increase in potholes. Fig.1 shows the correlation between reduced surface dressing treatments and subsequent increase in potholes over the past decade. Longer term, DfT statistics (fig.2) show a steady decline in the use of surface treatments over not just years, but decades. The REA and RSTA would argue that this is aligned with the continued pivot towards shorter-term funding decision making.
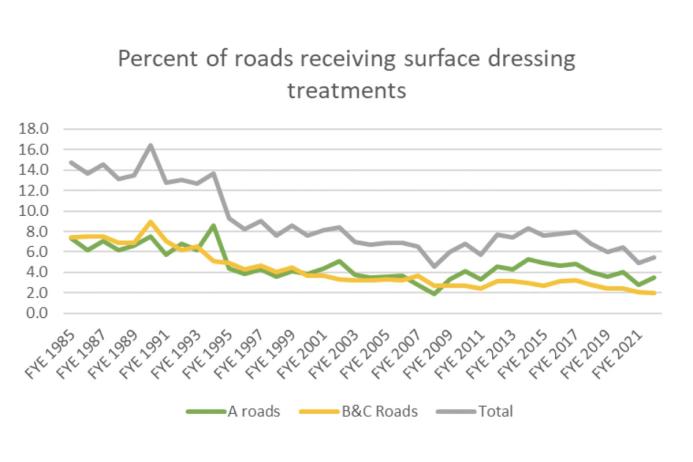
The case for surface treatments
The decline in the use of surface treatments represents a failure to leverage the advantages that such a planned preventative approach provides.
Through the appropriate planned application of such treatments prior to the development of serious surface and structural defects (such as potholes), road conditions can be managed and maintained far more effectively, as well as road lifespans extended – potentially indefinitely.
This provides significant cost benefits. Previous research by the Asphalt Industry Alliance[4] has shown that it is 20 times more expensive to carry out reactive maintenance (filling potholes) than planned, preventative maintenance.
Surface dressing is the most cost-effective method, both financially and environmentally, to improve skid resistance and seal the road surface, which will stop the ingress of water and help prevent potholes appearing in the first place.
The days of ‘tar and chip’ are obsolete. Proven technology using polymer-modified, high-performance bituminous emulsions are now used together with modern plant and equipment.
The development and introduction of proprietary finishes, while providing all the benefits described above, has also further improved the chip retention, and provides a ‘new road’ look for a fraction of the cost.
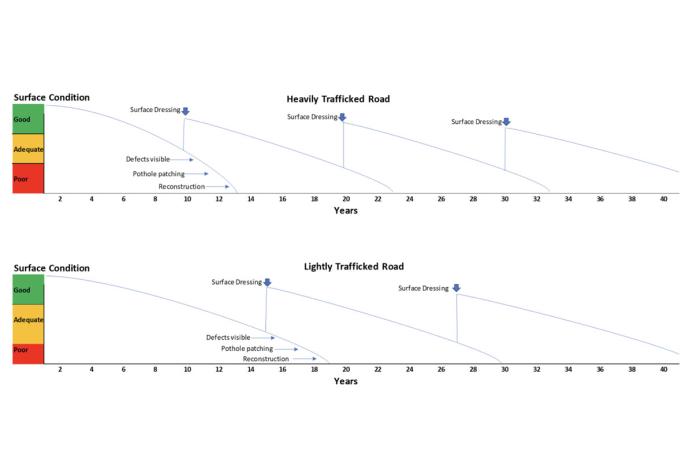
Application examples and cost benefits
Typically, a 6m wide road that is 1km long (6,000m2) can be surface dressed for approximately £30,000 and has a service life of 10–15 years. This is equivalent to the service life of an untreated thin (asphalt) surface course system[5].
To fully resurface the same road in traditional asphalt using primary aggregate could cost up to 10 times this amount and, without surface treatment intervention, last no longer.
So, for the amount that it costs to fix potholes, an additional 3,500km of local roads could be surface dressed, preventing the need for costly and time-consuming interventions in the future and the closure of roads to the public for pothole filling. Moreover, surface dressing brings major environmental benefits.
Modern asphalt surfaces are durable but, by design, sacrificial. Once their anticipated design life has been achieved, the eventual replacement of a typical thin surface (asphalt) course system uses a significant amount of high-quality and expensive aggregates. These are used throughout the entire surface course and not just the contact area of the road surface.
Surface dressing uses up to 75% less bitumen and up to 80% less aggregate per square metre than thin surface (asphalt) courses. This ensures that high-value mineral reserves can be kept in quarries for future generations, while mitigating the added high carbon cost of transporting quarried aggregates to sites across the UK.
Surface dressing interventions extend the surface course design life. If untreated, deterioration will eventually result in the need to resurface. A 6,000m2 road with a 40mm surface course being laid on top will use approximately 580 tonnes of aggregate. To transport this aggregate to site will take 30 vehicles, plus the same again for the disposal of the old planed out surface.
If the same road was surface dressed with a 10/6 racked-in dressing, the same site will be overlaid directly with approximately 100 tonnes of chippings. That will equate to a 75% reduction in transport movements.
Meanwhile, aggregate collected as part of the sweeper surface-cleaning process are recycled and reused, resulting in very little waste generated through the surface dressing application.
At the same time, the bitumen emulsion binders used are sprayed at between 85°C and 90°C, meaning significantly less embedded carbon is required than in asphalt surfacing.
Summary
Surface dressing not only significantly extends the service life of the pavement, with a reduced impact on the environment, but can also be re-applied in many layers over several years. It can help keep the road network safe while maximizing the service life and restricting emissions through fewer interventions and reductions in the use of equipment over the 60-to-90-year road lifespan.
Conclusion
The application of sustainable, low-carbon surface dressing systems on some ‘Amber’ and ‘Green’ local authority roads will further extend the life of the highway and mean fewer potholes, whilst preventing these routes from becoming ‘Red’ and resulting in a costly and disruptive repair for the taxpayer.
By taking the required decisions to adopt longer-term strategies to future-proof roads and act early to prevent, rather than cure, road defects, local authorities can achieve significant cost advantages. The REA and RSTA, therefore, strongly urge local authorities to seek to reverse the long-term downward trend in the use of surface treatments.
References
National Highways: Net zero highways - Our 2030/2040/2050 plan
AIA: Alarm Survey 2023
DfT: Road conditions in England to March 2022
AIA: Alarm Survey 2022
ADEPT RSTA – Service Life of Asphalt Materials for Asset Management Purposes
Subscribe to Quarry Management, the monthly journal for the mineral products industry, to read articles before they appear on Agg-Net.com