Slag In The Mix
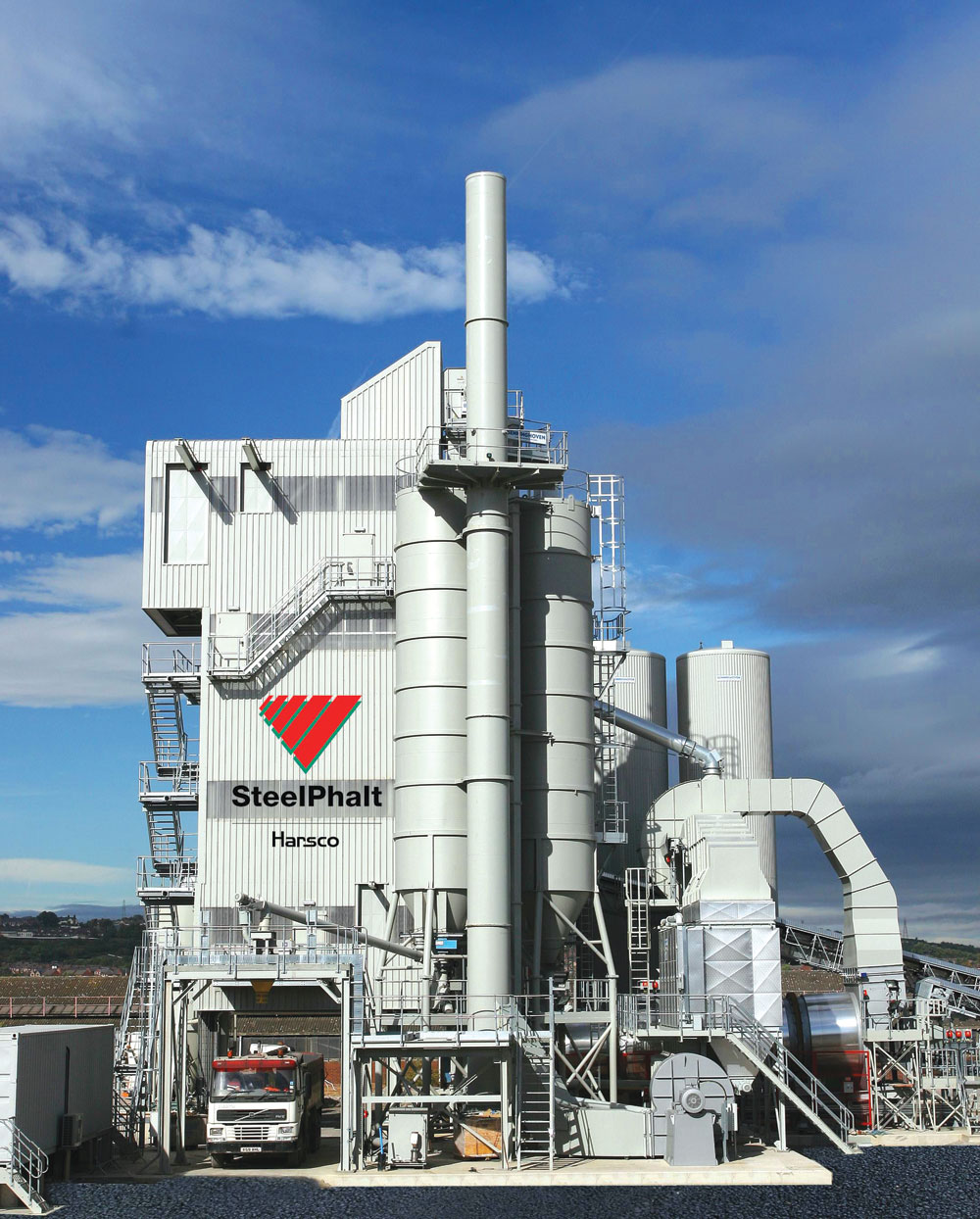
New Benninghoven asphalt plant for SteelPhalt in Rotherham
SteelPhalt’s new asphalt production plant in Rotherham is designed to meet asphalt contractors’ demands for a wide range of high-specification coated materials, including modern thin surfacings, stone-mastic asphalts and other specialized steel slag mixes, for which the company is widely recognized.
Steel slag has been successfully utilized in all road layers, from roadbase to high-performance surface courses, and its special qualities, eg exceptionally high skid-resistance and resistance to deformation, mean that it is increasingly being specified by asphalt buyers for various road-building applications. The use of steel slag in road building also offers clear environmental advantages by avoiding the need to dispose of the material to landfill.
To achieve the required mix specifications, production targets and necessary environmental criteria, SteelPhalt – part of the MultiServ Group – selected a Benninghoven TBA4000 asphalt plant equipped with a 4,000kg mixer. Offering the capacity to cope with rising demand, the plant is capable of producing over 240 tonnes/h of dense basecourse at 5% initial moisture, and 180 tonnes/h of hot-rolled asphalt (HRA) at 6% initial moisture.
At Rotherham, large, specially constructed covered concrete bays accommodate the bulk storage of materials for the plant, with the cold-feed system comprising an arrangement of two separate banks of in-line bins set at right angles to one another. One bank consists of six hoppers for sized slag materials, together with one 10m3 unit for granulated asphalt. On the aggregate side, two of the six hoppers are for sand and are equipped with hopper-wall vibrators to ease material flow. Apart from the granulated asphalt bin, all the hoppers are 14m3 capacity and each one is fitted with a frequency-controlled belt feeder for accurate blending. In addition, all the hoppers are sheeted on their sides, ends and roofs for protection from the elements.
A 28m long collecting conveyor transfers material on to a 10m long x 650mm wide inclined dryer feed conveyor, which, in turn, discharges on to a 3.5m long reversible slinger conveyor that feeds material directly into the aggregate dryer drum.
The dryer drum, which is 2.6m diameter x 10m in length, is fully lagged with 70mm thick Rockwool insulation and aluminium clad for heat retention and noise reduction. The drum is friction-driven by four support rollers through individual 22kW geared motor units. The dryer is enclosed by a 2m high safety fence fitted with an electrically interlocked access gate.
The burner is a Benninghoven Rax Jet 4, which is capable of burning gas oil, eco oil and natural gas. It is equipped with a full range of operating and safety devices to deliver high-efficiency fuel usage, while an air-inlet silencer is connected to the burner to suppress noise levels. Both the burner and silencer are mounted on a track to allow the unit to slide back from the dryer for routine servicing.
Designed to meet the most stringent dust-control regulations, the plant’s dust-collection system, sized for the dryer unit and mixing section scavenging, is rated at 72,000Nm3/h and achieves emission levels of less than 25mg/m3. A centrifugal skimmer unit mounted alongside the dryer separates any coarse dust from the airstream, which passes to the hot-stone elevator feed boot via a gravity flap valve and chute. A secondary cassette bag-filter system collects any remaining dust and transfers it, via two screw conveyors, to a filler elevator. Dust is also collected from nuisance points at the screen, weigh hoppers and elevator. A dust monitor mounted on the exhaust stack provides a remote readout in the operator’s cabin.
Any excess dust collected can be discharged from the reclaimed dust silo, through a rotary valve, into a twin-shaft paddle conditioner, where water is introduced to provide an environmentally friendly method of purging the reclaimed dust.
The main tower itself comprises a number of modular sections for ease of on-site assembly, with full sheeting extending down from the screen section through the hot bin and weigh sections to mixer level.
Hot aggregates are transported from the dryer up to the screen by a vertical bucket-type elevator. This is totally enclosed and features a heavy-duty double-strand chain and wear-resistant steel buckets with replaceable liner plates at impact points. Elevator drive is provided by a 30kW geared motor and toothed chain wheels at the elevator head. The elevator features externally located bearings and a safety backstop facility, while a wide platform provides access for maintenance.
Material discharged from the elevator passes into a six-deck screen featuring twin-shaft drive via two 19kW ‘bolt-on’ low-maintenance vibrating motors. These drive units are mounted outside the screen housing to allow for high-temperature screening of materials. Wide access doors, together with a roll-away chute, provide access to all screen decks. An extraction fan ensures negative pressure is maintained within the screen housing for optimum dust control.
The hot-storage section has a total capacity of 160 tonnes and comprises six bins. All the bins are insulated and clad and each one is fitted with continuous level indicators and an overflow chute. Discharge is by means of a pneumatically operated radial door, which accurately regulates material flow to the aggregate weigh hopper, from where the slag/aggregates are discharged directly into the mixer.
Accurate weighing out of ingredients is achieved by separate load-cell-mounted weigh hoppers – a 4,000kg capacity hopper for slag/aggregate, a 600kg filler weigh hopper, and a 400-litre capacity weigh vessel for bitumen; a 900 litres/min injection pump forces the bitumen into the mixer. Rapid and thorough mixing takes place in the plant’s insulated, 4,000kg capacity, twin-shaft paddle mixer, with drive provided by two 55kW geared motor units through synchronized gears. A radiation pyrometer is situated at the mixer discharge to indicate mix temperature, and a flux-oil metering system with spray bars is fitted to allow the dosing of non-flammable additives into the mix.
A 38m long covered conveyor transports RAP material to the mixer via a belt weigher to give accurate proportional blending. The system can accommodate 20% RAP in the mix at 3% moisture.
Bitumen is stored adjacent to the plant in three vertical tanks – one 50m3 capacity vessel and two 100m3 capacity vessels. These are Benninghoven’s latest high thermal efficiency tanks, which offer low running costs due to their stepped heating system design. In addition, an in-built loading system with high-level probes offers fail-safe filling with no possibility of spillage.
Reclaimed filler from the plant is stored in a 80m3 capacity vertical silo, and a similar unit is used to store imported filler. Both silos are equipped with level indicators and shut-off valves. A 21.5m high elevator transports filler up to the weigh section level.
A gravimetric additive system is also incorporated within the plant to feed granulated material from a 30m3 silo. Each batch of granulate is accurately weighed in a load-cell-mounted weigh hopper before being discharged through a butterfly valve to the mixer.
The plant is controlled by a Benninghoven on-line Batcher 3000 computer system, which displays all plant functions via colour graphics. The system, which is housed in an air-conditioned and heated control cabin adjacent to the plant, is modem linked and provides storage for up to 500 asphalt mix recipes.
Currently, the existing inclined mixed-material storage unit from the old plant at Rotherham is being dismantled and refurbished, and a new 4,000kg skip, skip track with steelwork and spray system will operate with the new plant.
All equipment was supplied and installed to exacting requirements and in accordance with current CDM directives.
Acknowledgement
Thanks are due to Paul O’Malley, business manager with SteelPhalt, SMACC & Forgemasters, and Nigel Moreton of Benninghoven UK Ltd, for their help in preparing this report.