Perfect Partners
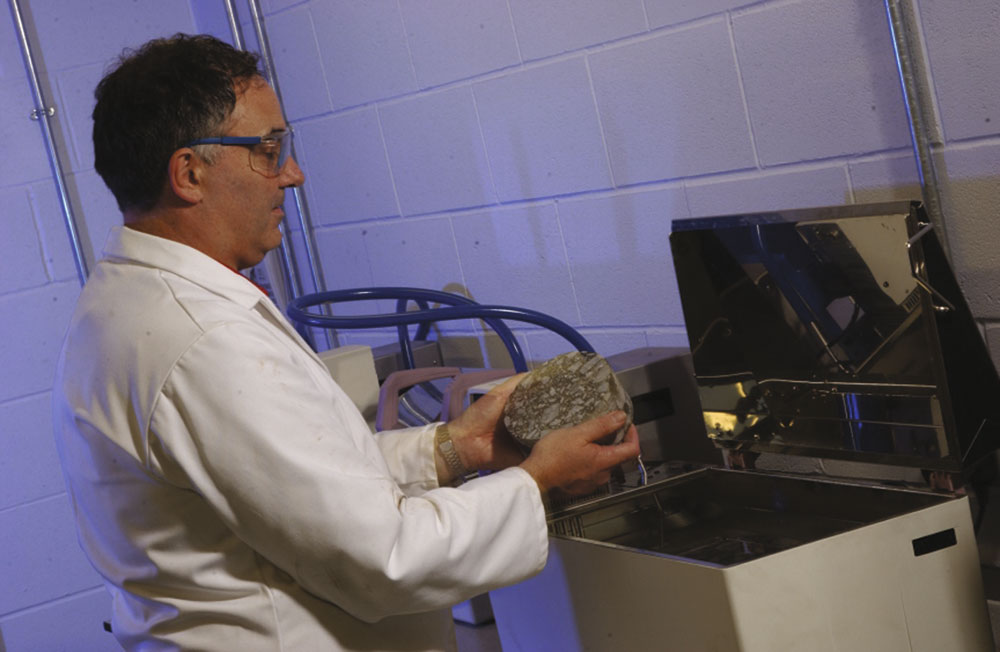
Shell Bitumen and The University of Nottingham benefit from pavement engineering alliance
In the past technical support to the asphalt industry from Shell Bitumen was predominantly troubleshooting; problems would arise with the performance of a particular road and Shell Bitumen would work with their customers to identify the source or sources of the problem and to rectify them.
The advent of performance specifications for asphalts changed all that, focusing greater emphasis on product development, particularly over the past five years or so. A flood of new proprietary products has hit the market as a result; and after a short pause for breath recently the pace of development is about to pick up again. ‘Five years ago most of our activity was problem-solving,’ says Shell Bitumen’s new-technology manager, David Whiteoak. ‘Now, joint development activity with customers accounts for a much greater percentage of our work.’
Shell Bitumen have always been at the forefront of research and development activity, but to be in a better position to cope with the greater demand Shell set up a formal link with world-renowned pavement engineering specialists at the Pavement and Geotechnical Engineering Division (PEGD) of The University of Nottingham’s School of Civil Engineering, called the Nottingham Centre for Pavement Engineering (NCPE). The PEGD is globally respected as a centre of academic and research excellence in pavement and rail-track engineering. The outcome of this alliance was the Pavement Research Building at the university which has now been open for two years. David Whiteoak says the demand for its services has been very high.
The Pavement Research Building is a unique, state-of-the-art pavement engineering facility housing leading-edge research facilities that have attracted worldwide admiration. It represents a £2.3 million investment and was built as part of a long-term deal with the School of Civil Engineering. Shell have based the specialist engineers of their UK technical department in the building, which also houses the university’s pavement engineering staff and research students — a total of 40 people.
Each partner has separate research facilities, with the university undertaking pavement testing and academic studies into all aspects of pavement and rail-track engineering. Shell Bitumen’s work in Nottingham includes most of the laboratory tasks previously carried out by staff at their Shell Global Solutions bitumen laboratory at the Cheshire Innovation Park, formally known as Thornton Research Centre. Road as well as rail industry clients can access the centre for independent testing services.
‘Ten years ago,’ Mr Whiteoak says, ‘clients used to focus on price and specification, now they are looking to be one step ahead of their competition so technical support is a critical part of their customer-value proposition. We are still providing the highest quality of technical support, including troubleshooting, but these days clients are increasingly interested in innovations in products. The centre allows us to combine the talents of leading academics in the field with our own technical and commercial skills.’
The Shell–University of Nottingham link dates back to 1954 when Shell awarded the university its first contract in pavement engineering, to study cracking in asphalt pavements. Nottingham’s track record has been well established since then, resulting in the development of several innovations for equipment used in research and experimentation. Nottingham has also developed analytical methods for the design and evaluation of asphalt pavements that are used in many other countries. Within the Pavement Research Building a wide range of tests and analyses on bitumen and asphalt are carried out, providing support for the university’s research projects. ‘The ability to maintain confidentiality is absolutely crucial to the reputation of the facility from Shell’s point of view,’ says Mr Whiteoak. ‘All of our laboratory services in the UK are now carried out here and we bring a lot of materials to be tested on behalf of clients. We have a secure laboratory management system that ensures anonymity of sample sources to protect both confidentiality for customers and Shell’s intellectual property.
‘We could have continued investment in our own facilities but we saw strategic benefits from forming an alliance with another organization. So we looked for a partner who is the best in the field and that was The University of Nottingham. Our timing turned out to be perfect as the university was looking to rationalize its activities, and we quickly agreed on the terms of a strategic alliance.’
The university now has a modern building to bring together all its pavement engineering staff and students under one roof for the first time. There is a good fit with the respective workloads of a busy, commercially focused organization like Shell and the longer-term, research-based thinking of an academic institution. Mr Whiteoak explains: ‘We need things done almost immediately on behalf of our customers,
whereas the university undertakes mostly one- to three-year projects. So if we need a lot of attention quickly devoted to a particular job we have the flexibility to focus more effort on a short-term basis.’ A wide range of projects are being undertaken on behalf of Shell and with an eye to the market, while having a strong connection to the more ‘blue-sky’ thinking which the academics do.
What areas are the researchers looking at for future development? Much attention has been given in the past seven years or so to material design and Shell believe that the properties of asphalt are now well understood. Attention in the future is likely to focus more on pavement and structural design.
‘The market has changed,’ says Mr Whiteoak, ‘and what is in an asphalt is much more intensively analysed than before. Optimization of asphalt formulations will continue — if it lasts 15 years how can we get it to last 20 years? Rapid delivery of technology is a key issue and it is not unusual for developments in the laboratory to be commercial for both our customers and ourselves within 12 to 18 months.’
Clive Mather, chairman of Shell UK, visited Nottingham in 2003 and gave the work of the School his full backing. He said: ‘This is pioneering stuff, with no model anywhere else in Europe offering this level of partnership expertise. It demonstrates our commitment to develop ever more advanced bitumen for the roads and airfields industry, and our leadership in terms of technical innovation.
‘We had to make a transition from having a well established laboratory operation within Shell to working with a third party. There was a culture change for us both, as our respective cultures are very different. Universities generally do not recognize customers; they are focused on papers and presentations. We are firmly focused on customers and we strive to give continuously better service to them. We have learned how to work together in ways that allow the two sets of objectives to be satisfied.’
Shell Bitumen, Rowlandsway House, Rowlandsway, Manchester M22 5SB; tel: (0870) 201 7777; fax: (0870) 201 8888; website: www.shell.com/bitumenuk