New Drum-Mix Plant Fabric Filter Installation at Bardon Hill
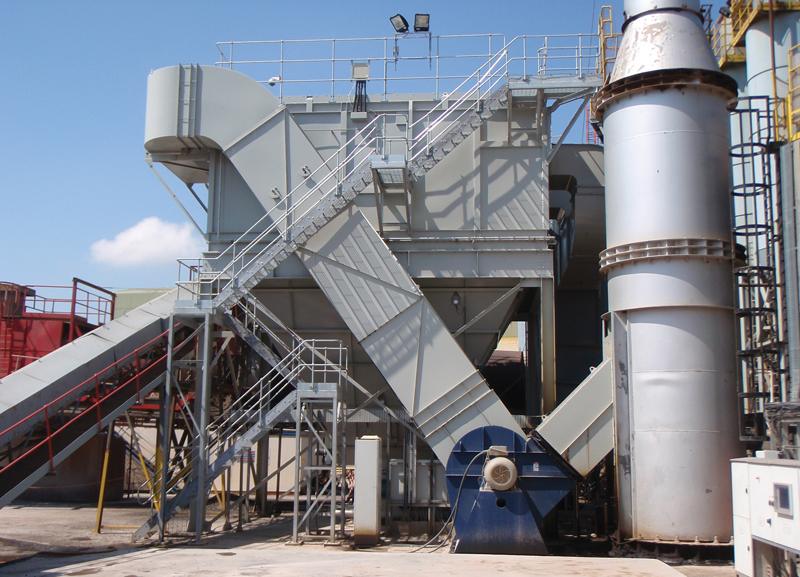
First published in the January 2016 issue of Quarry Management as Feeling the Pulse at Bardon Hill
New BG Europa SF20/2 fabric filter installation provides increased exhaust and filtration capacity
Replacement of the existing fabric filter on the Standard Havens drum-mix plant at Bardon Hill presented a challenge for BG Europa (UK) Ltd, as Aggregate Industries wanted the new installation to occupy the same area as the existing unit, whilst offering increased exhaust and filtration capacity.
The existing reverse-air cleaning filter unit had provided several years of service, however the need for a replacement provided the opportunity to increase capacity in preparation for the future upgrade of the drum mixer. With limited space available, a bespoke solution was needed in order to install the new filter system within the footprint of the existing unit.
BG Europa’s SF pulse-jet filter offered the opportunity to increase both filtration performance and available exhaust capacity, whilst utilizing the existing foundation fixings.
Using a pulse of compressed air, the BG Europa SF filter generates a shock wave which cleans the filter bags. This advanced and efficient method of cleaning has been well proven in the field and does not suffer from the problems often associated with reverse-air filters, which suck atmospheric air into the bags to clean them.
Moreover, the internal design of the pulse-jet filter eliminates the need for ducting channels within the filter body, thereby allowing a higher density of cloth to be installed.
SF20/2 fabric filter installation in operation
At Bardon Hill, a total of 1,280 x 500g/m2 Nomex type filter bags are installed in two 10-module parallel filter units to provide a total cloth area of 1,438m2. Within the snap-ring bags, the zinc-coated wire bag-support cages each incorporate an integral venturi to enhance bag cleaning efficiency.
The pulse-jet shockwave cleaning system sequentially cleans rows of filter bags while they are online, thus ensuring that all of the cloth area within the filter is utilized at all times for efficient filtration. This contrasts with the reverse-air type cleaning method, which can take up to 25% of the bags off-line for cleaning.
An electronic pulse controller, installed within a dust-tight enclosure mounted at the filter top, is pre-wired to each of the solenoid valves. This allows fine adjustment of the cleaning pulse duration and frequency to suit the operating conditions. Additionally, a differential pressure monitor is installed to ensure cleaning is only performed when required, thus reducing energy requirements and ensuring the bags maintain the ultimate level of cleaning performance.
The bags and cages are factory installed within the filter unit top sections to speed-up site installation. The filter top is enclosed by handrails with safety-gate access and kicking strips. Within this area, access to the bags and cages is provided through full-width, easily removed hatch covers.
The compressed-air manifold for bag cleaning is housed within the filter body ensuring protection from the elements. This arrangement provides easy access from within the handrailed area at the filter top by the removal of full-length lift-off covers. The solenoid valves are also fitted on top of the manifold, allowing unrestricted access for ease of maintenance.
Collected fines fall from the filter bags into a common pyramid hopper with dimensions designed to allow its support structure to be fixed to the original foundation bolt nests. As a result, the project did not require any additional civil works, thus minimizing both disruption and overall costs.
Regardless of infrequency of access, the existing vertical ladder, which is a common feature of most existing filter installations, did not provide the degree of safety now expected within the industry. Therefore, BG Europa supplied and installed stairways and rest platforms to allow improved access from ground level to the filter top, inlet ducting and exhaust stack.
Jason Broughton, asphalt operations manager at Bardon-Croft, commented: ‘With no operational issues since the installation, it has been a perfect replacement and what we expected. BG Europa’s bespoke design minimized any disruption and overall costs, with the extra stairway and improved access bringing everything in line with the current health and safety requirements.’
Fulfilling their project brief on time, BG Europa have provided Aggregate Industries with a modern system designed with safety as a key criteria. Additionally, the facility now has the capacity and flexibility to allow future upgrades as new clean recycling technologies become available.
For more information visit: www.bgeuropa.co.uk
- Subscribe to Quarry Management, the monthly journal for the mineral products industry, to read articles before they appear on Agg-Net.com