Making Greener Roads
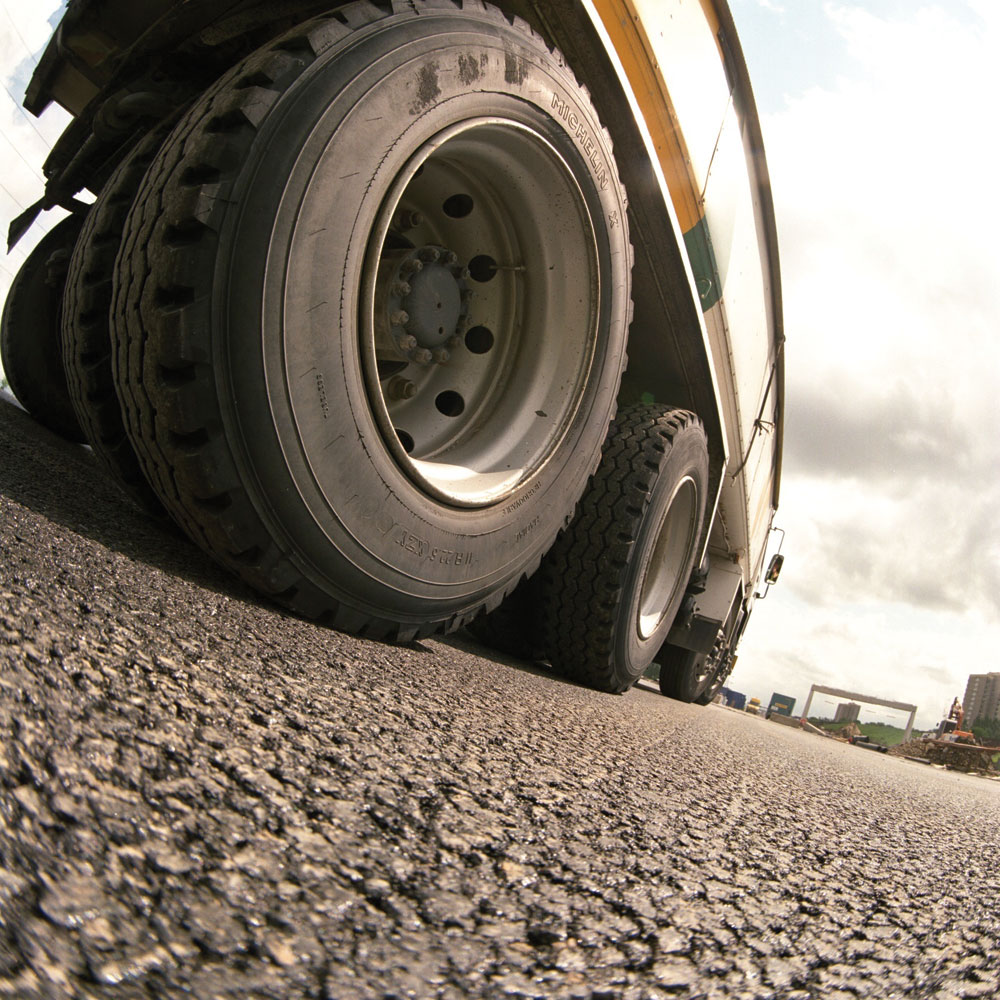
At a time when ‘saving the planet’ is high on the agenda, the use of environmentally friendly alternatives as bitumen modifiers is becoming an increasingly popular option. Neil Turner, technical director at Excel Fibre Technologies, examines the benefits
Protecting the environment is one of the burning issues within the road construction and maintenance industry, and one of the ways ‘greener’ practices can be implemented is to incorporate chemical-free fibre modifiers into the bitumen mix.
There is an abundance of waste paper in the UK; it is estimated that around 2 million tonnes of paper is sent to landfill each year. In fact, many local authorities are landfilling waste paper as far as 100 miles away from their boundaries. It makes good sense, therefore, to try to recycle as much waste paper as possible, and one way of doing so is by reusing it as a bitumen modifier in the UK’s road systems.
Environmentally sound
The mechanical process used to transform everyday newspapers into a cost-effective, high-performance fibre product requires minimal energy, which means that the finished product has low embodied energy. Reinforcing its sustainable credentials, the fibres also have zero ozone depletion potential (ODP) and are free from CFCs, VOCs and other harmful substances.
Despite being produced from a recycled feedstock, cellulose fibres are manufactured to tight specifications, in some cases regulated by BBA/HAPAS in the UK. Using a combination of ‘fibre-izing’, milling and granulation, the waste newspaper is transformed into its original cellulose fibre state and re-engineered so that it has the correct fibre length and consistency to deliver optimum performance.
Newspaper makes up the bulk of the fibres, with other materials such as paperback books and telephone directories also used. These are sourced through kerbside collections as well as community schemes, such as those run by schools to bring in unwanted materials for collection.
Creating a strong, safe surface
The fibre works in the bitumen to produce a high-quality durable surface that is tough, smooth and quiet, with high deformation and rutting resistance.
As no chemical additives are incorporated into the fibre, it is completely safe to handle while being added to the bitumen. Once the fibres have been dispersed within the mix they hold the bitumen in place during laying by creating a lattice, binding the materials together without impairing adhesion to the aggregate material. This lattice, created by the interweaving of the long fibres, gives the surface an increased elasticity, making it less brittle and more able to withstand continual heavy loading.
This increased elasticity leads to significantly reduced permanent deformation and, therefore, less rutting. The strength and resilience of the bitumen fibre mix means that thinner coverings can be applied, which reduces both the costs and the time needed to lay the surface.
The closely controlled manufacturing process guarantees consistency in the size of the fibre, which in turn ensures that it holds together during handling and transportation but breaks up and disperses quickly and evenly when mixed. This results in a surface that has evenly distributed texture and voids, thereby contributing to a quieter, more enjoyable drive, with excellent wet skid-resistant properties.
The enhanced durability cuts down on the work needed to maintain the surface, which is not only cost-effective, but also good news for drivers who, as a result, encounter fewer disruptions to their journeys. In addition, the longevity of the surface equates to extended periods between resurfacing, and when the surface does need replacing, the thinner layers can be planed and replaced more easily, again keeping disruption to a minimum.
High performance in harsh conditions
Fibre modifiers have demonstrated exceptional performance at critically low temperatures without sacrificing performance. The fibres have also been tested and shown to be free from mould growth and swelling throughout the lifetime of the road. In addition, extended accelerated ageing trials, which subjected the fibre mixture to water and soil bacteria, have demonstrated a resistance to rotting and premature degradation.
The structure of the finished surface also allows it to accommodate more water, which is held within the body of the material rather than on the surface, thereby providing safer driving conditions in wet weather. Moreover, this ability to hold water produces less spray and reflects less glare from the road surface, thus aiding visibility. Road markings also become more visible, and the reduction in surface water reduces the chance of skidding and aquaplaning.
Ease of use
Fibre modifiers can be supplied as individual bags or via bulk tanker, depending on the equipment available at the mixing plant. The fibres can be compacted, in the form of pellets, to minimize volume for transportation and handling, while the engineering processes ensure there is no clumping in the mix. The bags are specially designed to be ‘low melt’, so they too can be thrown in and will disperse throughout the mixture to save time. Additionally, because the fibres are made from recycled newspaper, they are totally inert they will not degrade over time, giving an unlimited shelf-life.
Best of both worlds
At a time when the road industry is striving to become more environmentally friendly, recycled fibre modifiers are a cost-effective alternative offering high levels of durability and a smooth, long-lasting surface. With a successful track record over the last 15 years, the fibres have been tested in harsh road conditions and have proved to be a viable ‘green’ alternative.