Low-temperature Asphalt
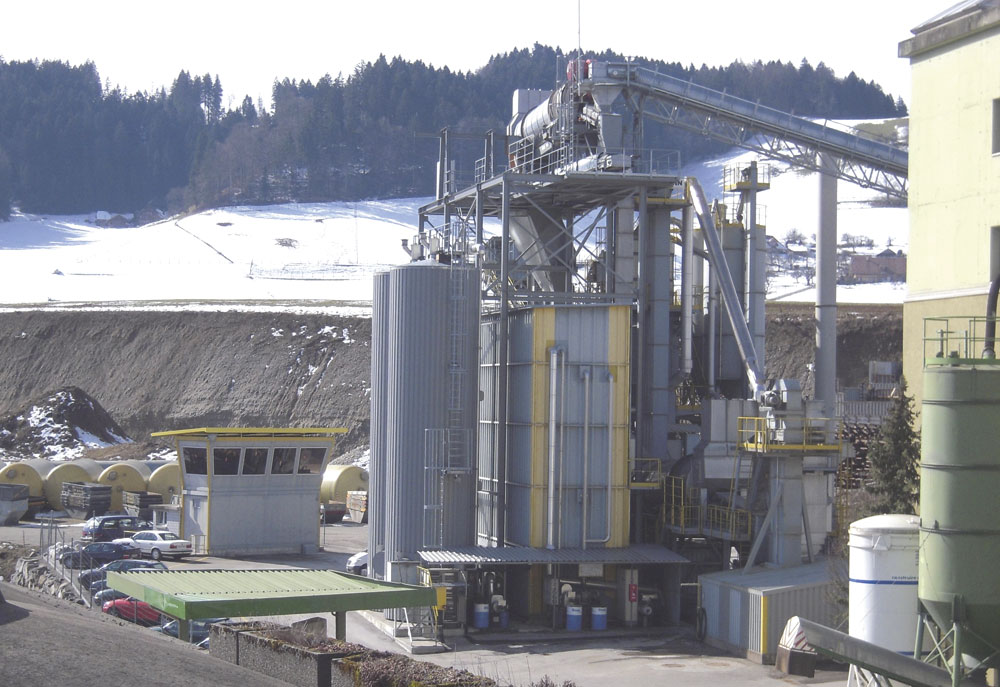
Another step towards ‘green roads’
Natural fluctuations in the global climate occur over periods ranging from a few years to millions of years. For more than two-and-a-half centuries, humans have increasingly changed the composition of the atmosphere through greenhouse gas emissions. Human activities tend to reinforce the natural greenhouse effect, leading to noticeable changes in the climate. Studies indicate that average global temperatures have risen by 0.74°C during the last 100 years, with a particularly sharp increase since 1970. Many climate experts now believe that the severe warming over the last 30 years can no longer be explained by natural climate fluctuations alone, and that it is more likely to have been caused by the greenhouse gases that humans have introduced into the atmosphere by activities such as the burning of fossil fuels or the clearing of large areas of tropical rainforest. Carbon dioxide (CO2) accounts for the majority (80%) of man-made greenhouse gas production, and asphalt mixing plants are a major source of such emissions.
The two key aspects of a ‘greener’ asphalt industry are lower production temperatures and the use of as much recycled asphalt as possible. Lower asphalt mixing temperatures lead to reductions in various emissions, which is why the industry is introducing what is known as ‘warm-mix asphalt’. This is produced and laid at about 100°C, instead of the usual temperatures of around 160°C.
Likewise, increasing the proportion of recycled asphalt results in a direct reduction in overall CO2 emissions from the road construction industry. Even today, large quantities of asphalt are simply dumped or used for insignificant applications, but in order to safeguard resources, it would be more appropriate to use the available reclaimed asphalt, which consists of high-quality bitumen and ready-prepared aggregate, in high-performance applications to build new, long-lasting roads.
Key benefits of lower asphalt production temperatures include:
- less fuel consumption
- reduction in emissions from the plant (gases and smoke)
- reduction in emissions on site, which significantly improves working conditions for employees, machine operators and people living in the vicinity.
Different technologies for low-temperature asphalt
Various methods for producing low-temperature asphalt are available. They include the use of additives, foams, special types of binding agents or a combination of these methods. It is usually possible to lower the mixing temperature by at least 20°C and sometimes by as much as 70°C. Various technologies are used, depending on the plant operator and the conditions on the construction site.
Bitumen foam
Viscosity measures a fluid’s internal resistance to flow. In order to modify viscosity at relatively low temperatures, so that the bitumen can mix well with the granular aggregate, cold water at high pressure is sprayed into the heated bitumen through nozzles. The bitumen is gently cooled and foamed at the same time, making it more fluid. As this happens, its volume increases by more than 10 times; this ratio is known as the expansion factor. The foam that is generated in this way soon subsides again, and the half-life is used to quantify the time taken for this to happen. However, the better a bitumen can be foamed, the faster it will usually subside, so the objective is to find an ideal combination of expansion ratio and half-life. The granular aggregate must also have specific properties so that it can be processed to make foamed bitumen asphalt.
Some of the parameters relating to the properties of asphalt produced using foamed bitumen vary slightly from those of conventionally manufactured asphalt, although generally these neither increase nor reduce the quality of the asphalt itself.
Plant installations and construction site
Depending on the technology chosen to reduce the asphalt production temperature, different modifications to the asphalt production plant will be necessary. For example, to produce asphalt using foamed bitumen, a special component for foam generation is necessary. Notwithstanding such modifications, asphalt mixing plants in different regions of the world are gearing up to be able to produce low-temperature asphalt.
As recent projects have proven, only minor construction site changes are necessary for the paving and compacting of low-temperature asphalt made with foamed bitumen. Depending on the chosen recipe, the manual workability can be slightly harder, but workers have noted an improvement in the work environment due to the absence of the typical blue smoke.
Low-temperature asphalt can be paved and compacted in the same way as ordinary hot-mix asphalt
Summary
The key benefits of low-temperature asphalt, compared with hot-mix asphalt:
- Energy is saved.
- Stack emissions are reduced (CO2, CO, NOx, VOC).
- Blue smoke is reduced on site.
- Working conditions are improved.