Improved Efficiency At Purfleet
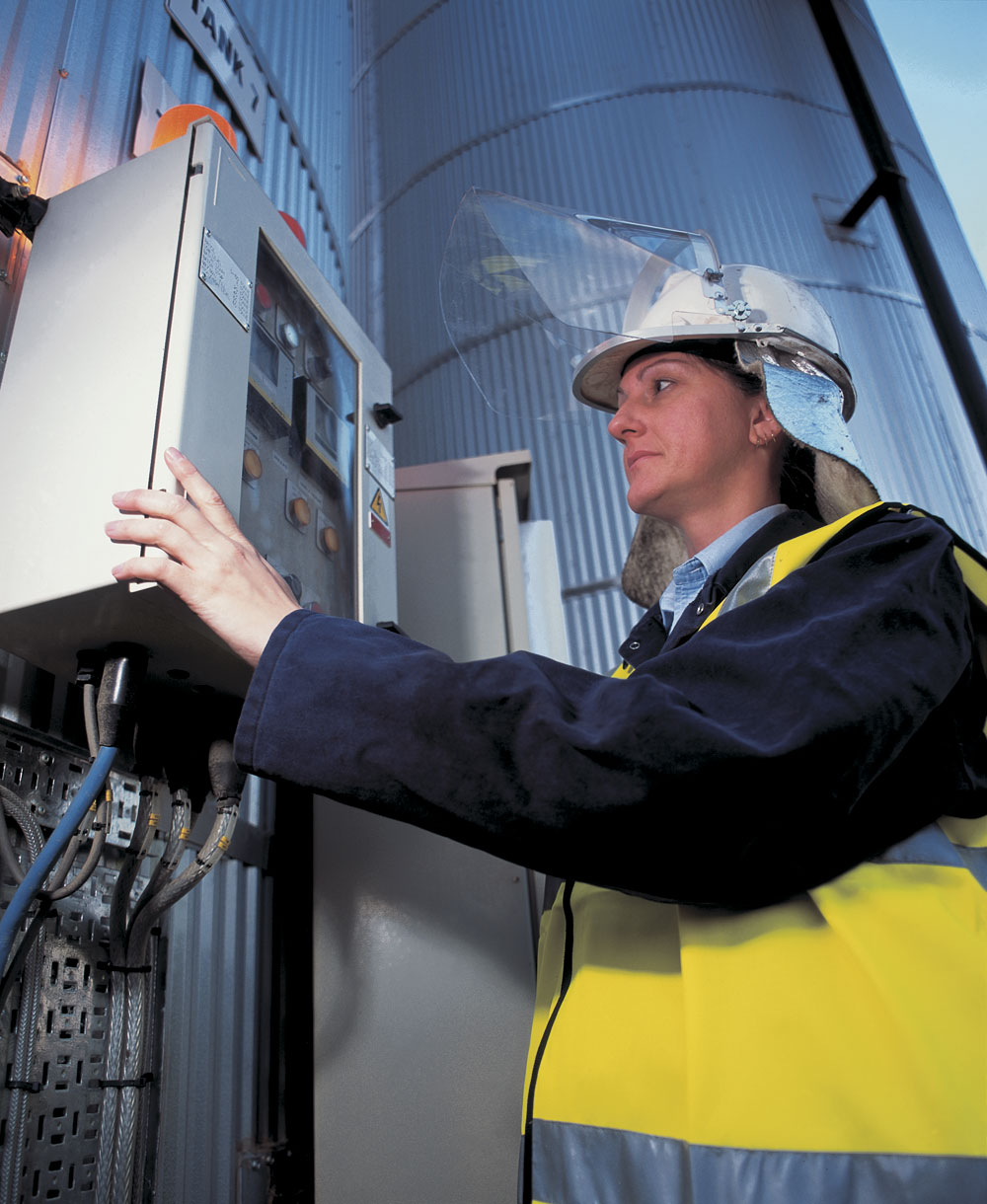
BP Bitumen and Foster Yeoman redefine bitumen stock management
By Phil Shirley
BP Bitumen, a European leader in the development, production and supply of bitumen products, and Foster Yeoman, one of the UK’s leading producers of asphalt, have launched a joint initiative which, they say, has the potential to shape the future of bitumen stock management.
The two companies have invested a significant amount of lead time in developing a stock-management system using specially engineered giant storage tanks and the latest monitoring technology to create one of the most efficient and safest asphalt plants in the UK.
‘We have been rolling out logistics solutions using large tanks within our customer base for several years now,’ said BP Bitumen UK marketing and product manager Mark Bunch. ‘It’s a learning curve and the work we are now doing is the culmination of years of experience working with some of the leading companies within our customer base, such as Bardon, Brett, Hanson, MQP and Foster Yeoman. The timing of this joint initiative was right and we will be looking to roll out such offers across our customer base where an appropriate business case has been established.'
The flagship project required a substantial investment in bitumen tanks and telemetry at Foster Yeoman’s Purfleet depot, but the two companies believe the health, safety, environmental and logistics supply chain management benefits will provide a worthwhile return on the investment during the plant’s operational life, particularly in the area of plant safety.
According to the Refined Bitumen Association, the total number of safety incidents reported at delivery sites increased from 57 in 1999 to 99 in 2002. Significantly, 80% of the total number of safety incidents reported at delivery sites in 2002 were due to spillages, an increase of more than 20% on 1999’s spillage-related incidents.
BP and Foster Yeoman have excellent records of managing safety within their own organizations and their commitment to improving safety at Purfleet is a good example of health and safety ‘best practice’, particularly as Foster Yeoman are one of the UK’s leading producers of asphalt with a manufacturing capacity of over 2 million tonnes a year from 11 plants located at eight sites across southern England.
‘Safety is our first priority and we offer our customers a comprehensive range of health, safety and environmental information and a commitment to work with them in partnership for greater safety awareness,’ said Mr Bunch. ‘Our core offer revolves around the operational imperatives of the safe supply of product at the correct temperature, on time and on specification, backed up by a high level of customer responsiveness.’
The Purfleet plant, which is approximately 30min from BP Bitumen’s primary bitumen production unit at Coryton refinery in Essex, is 14 years old and produces up to 500,000 tonnes of asphalt each year, making it one of the largest plants in the UK. Prior to the recent modernization, however, its capacity was restricted to three 60m3 bitumen tanks for main production grades and two 30m3 tanks for more specialized grades.
According to Purfleet depot manager Mark Pomfret, plans to upgrade the site began almost two years ago as changes within the industry began to increase pressure on the performance of the plant. ‘Several factors persuaded us to modernize the plant,’ he said. ‘These included an increase in the load size of bitumen deliveries from 18 tonnes to 27 and 28 tonnes, shorter delivery windows, increased traffic congestion and increased customer expectations of delivery performance.
‘The remedy was to increase our bitumen storage capacity and create more delivery flexibility. Our goal was to improve our service to customers and increase plant safety. We have achieved both, largely through the effective management of functional safety, using the latest instrumentation technology to provide protection of people, plant and the environment, combined with optimum availability of plant operation.’
BP Bitumen and Foster Yeoman approached bitumen-handling system specialists Cartem to design and build the largest practical tank that could be factory fabricated and delivered to site by road, thus avoiding the more expensive site-build option.
The limiting factor of the design was the maximum permitted travelling width for transportation to site without resorting to excessive oversize loads, which could have involved costly road closures and overhead cable removals. The resulting design allowed 12m high vertical vessels of 150m3 gross capacity to be produced and delivered, the largest of their kind ever to be built by Cartem.
The new tanks were designed to include a transfer system that automatically fills the existing 60m3 working tanks when their contents reach pre-defined levels. The transfer system has a number of sophisticated controls that ensure safe actuation of the valves and pumps. Reliable level controls and back-up equipment prevent any danger of overfilling the working tanks.
Telemetry has been used within other industries for several years but is relatively new to the asphalt industry. The 150m3 stock tanks at Purfleet feature the latest telemetry systems from Siemens, allowing BP Bitumen to remotely monitor the contents of each tank via a PC. This in turn allows them to plan delivery requirements more efficiently, rather than relying on ‘just-in-time’ telephone orders which place unwanted pressure on scheduling. The new Internet-based system, which is linked via a cellular telecommunications device fitted at the site, will potentially eliminate weekend deliveries with the majority of supplies being made during a broad night-time delivery window to suit logistics.
The system is fully integrated so that Foster Yeoman and their logistics supplier, Excel, are also linked into the communication network. The levels of the new 150m3 stock tanks and the existing 60m3 working tanks are monitored by a non-contact radar device which allows all three companies to maintain a ‘level watch’ 24h a day, seven days a week.