How Warm-Mix Asphalts Can Reduce Risk in an Asset-Management Culture
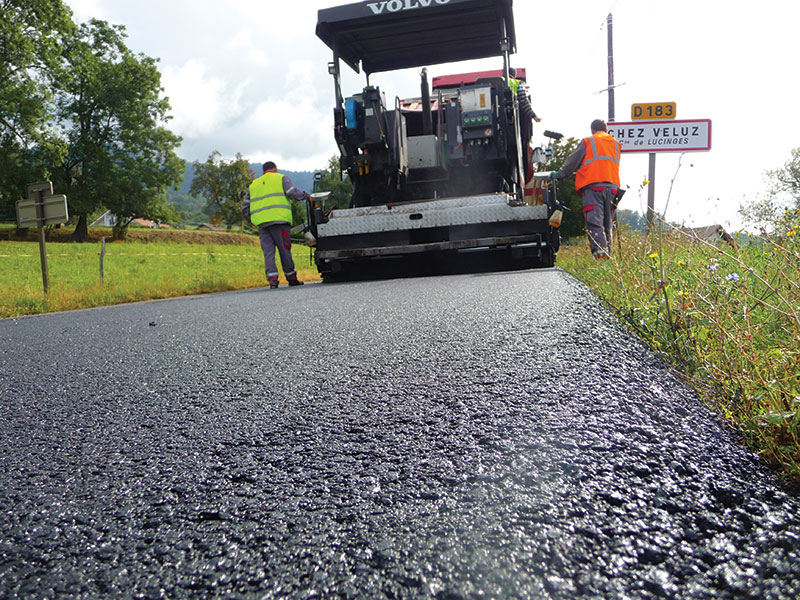
First published in the June 2015 issue of Quarry Management as Making the Link
Reducing risk in an asset-management culture
By Rick Ashton, market development manger, Bitumen Division, Total UK Ltd
So far, 2015 has seen good news stories on highways investment on the back of bad news about potholes and the backlog of repairs on the local road network.
The Government is slowly progressing towards the sensible funding of one of the nation’s most valuable assets in a way the industry and the clients have been asking for for many years. There is still a long way to go, however, in terms of addressing years of underfunding and the subsequent backlog.
The media is full of pothole stories and statistics generated by the Asphalt Industry Alliance ALARM survey are being quoted by politicians and practitioners alike. Buzzwords mentioned throughout the industry include ‘whole-life cost’, ‘asset management’ and ‘investing to save’ – not to forget ‘outcomes’.
Could it be the planets are starting to align for the asphalt industry and the time has come to throw off the shackles of austerity to start to gear up for recovery?
Imaginations have been captured and the public mood heightened through the media raising the profile of the ‘Pothole scandal’ over recent times. Indeed, the recently launched ALARM is often referenced as ‘the pothole survey’ in the media. This is missing the point somewhat. Potholes are a symptom of the disease (underinvestment) not the disease itself. But what disease are we dealing with? How can asset-management systems and ‘investing to save’ cure this malady?
Asset management
To manage any assets there has to be a short- and a long-term strategy, combining these effectively to give the right outcome at the end of the investment venture. This ethos can be related to any investment, be it shares, pensions, running a car or surfacing a road. If an entity is recognized as a physical asset, it is necessary to manage it precisely over a set period to create maximum return from the investment.
For example, routine servicing of a car is crucial to the efficient running of the vehicle. Moreover, if the correct service schedule is not followed, the manufacturer’s warranty and resale value will be adversely affected, making penny-pinching an ineffective economic strategy. At the outset, this behaviour may seem painful to the pocket but the enthusiastic owner knows, through experience, that this outlay and attention to detail will give rewards throughout the ownership experience and pay commercial dividends when the asset is eventually released from his or her care.
Likewise, traditional financial investments are not entered into lightly then left to mature without thought or maintenance. Share portfolios are considered investments and constantly monitored for performance. Pension investments and property portfolios are managed with appropriate care taken in their selection and return on investment or capital employed measured in earnest. Sustainable business in the banking sector is now seen as critical.
So how can this logic apply to the highways sector?
For a long time cost was king in asphalt procurement. Knowing the cost of everything yet the value of nothing is poor accountancy. Cost versus value, or in this case performance, is the key to life-cycle efficiency, and ‘sustainability through durability’ sums up this ethos. Put simply, cheap can be expensive.
There is no doubt mistakes have been made in the past, sometimes in terms of specification applied, and sometimes miscalculated installation in unsuitable climatic conditions.
The application of texture specifications more suitable to traditional positive-textured materials was applied to early negative-textured thin-surfacing. This resulted in harmful outcomes for the client resulting in some of the adverse publicity around early SMA products adapted to the UK.
The recent introduction of maximum texture limits should improve matters in this regard.
Most asphalt types have an optimum application and each has a place in the engineer’s inventory. Asphalt is made up of some simple components which when mixed together result in some pretty complex behaviour.
If anyone ever writes ‘The Asphalt Engineer’s Book of Failure Modes’ it could be filled with terms such as rutting, static creep, pushing, fatting, fracturing, embrittlement, reflective cracking, alligator fatigue cracking, fretting and even ‘looking tired’.
Behind any of these symptoms there is rarely one contributing villain causing the behaviour. Asphalt performance can be influenced by many factors including manufacture, mix, installation, traffic, climate, drainage or indeed a combination of all the aforementioned considerations. One way to reduce engineering risk in any given situation is to design out the known risks to end performance. Remove the known risks from variables that offer the likelihood of a historic failure mode and confidence is then developed in the structure’s resilience or durability.
Polymer-modified bitumen (PMB) offers this opportunity in ways traditional penetration-grade bitumen cannot. The careful use of selected polymers and additives in bitumen can extend the effective temperature range across which asphalt remains solid at high temperatures (reducing the risk of deformation) yet flexible or elastic at low temperature (reducing the risk of cracking). Traditional generic PMB incorporates polymer in a physically blended state with polymer and bitumen blended and dispersed together yet held in separate phases at microscopic level. This offers some benefits as outlined. Particular care is needed with these traditional products in terms of the performance limits they are exposed to and in silo storage during manufacturing. Separation stability can be an issue with the separation of the polymer from the bitumen being a reality in long-term storage. There are many variants in the polymers and additives used and some suit certain applications better than others – not all PMBs are the same.
Cross-linked PMB
Research and development spanning more than 30 years at Total Bitumen has seen the continuous development of a portfolio of ‘cross-linked’ PMBs known as the Total Styrelf range.
Cross-linking PMB involves the addition of a chemical catalyst to the PMB which chemically links the polymer strands in what can best be described as a three-dimensional network. This characteristic gives a much more cohesive structure to the PMB.
With this technology the effects of oxidative ageing are reduced and retention of elasticity or elastic recovery is maintained across an extended service period, in comparison with physical blended PMB. Storage stability is also helped by the formation of this network.
An example of the enhanced performance of Total Styrelf cross-linked PMB was a long-term trial spanning 14 years undertaken by The University of Lausanne in Switzerland. Sections of a mountainous motorway were constructed with the same asphalt mixture but using 16 different binders, including penetration grades, modified penetration grades and various polymer-modified binders.
Asphalt cores recovered from the long-term test facility showed that 80% of the Total Styrelf binder elastic recovery characteristic was intact after 14 years of service. The main failure mode observed in the other test sections at this point was cracking through the effects of thermal cycling, ultraviolet and oxidative binder hardening due to the exposed mountain location.
After 20 years the only test section remaining serviceable and not replaced was the cross-linked Total Styrelf section. The conclusion of the independent study was that cross-linking a PMB enhances elasticity and the retention of the early-life characteristics.
Cross-linking the PMB protects an asphalt, postponing embrittlement and, hence, reducing failure modes such as fretting or fatigue cracking in harsh environments. This, in turn, adds resilience to cold-weather cracking as the asphalt ages. It is these qualities that could assist the client looking for long-term confidence in material performance and, hence, more predictable asset management.
Warm mixes
Warm-mix asphalt technology now available from Total can also be applied to this PMB technology. Total Styrelf Eco2 been has developed to offer all the technical advantages of a cross-linked PMB but with a significant reduction in application temperature. Reducing the installation temperature of asphalt gives several advantages.
The initial development of lower-temperature asphalts was driven by the carbon-reduction agenda. This led asphalt manufacturers to begin looking at the whole energy costsof producing hot-mix asphalt. What became apparent during this early learning curve are the other significant advantages these products can offer in tandem with these benefits.
There have been huge steps forward in the US in the specification and take up of such products. It is currently estimated that more than 30% of US asphalt production is based on reduced-temperature technology. Interestingly, the drivers for warm-mix technology are not solely a reduction in energy or CO2 emissions. The current drivers for this uptake are even more tangible.
Reduced-temperature asphalt offers physical engineering benefits to the producer and contractor alike. The production technology has been simplified. Where once capital investment was required in production facilities for foaming systems and water injection, associated flow meters etc, ready-to-use warm-mix binders such as Total’s Azalt Eco2 or Total Styrelf Eco2 are now available. These ‘off-the-shelf’ modified bitumen products are delivered and stored in the same manner as conventional binders but mixed at reduced temperature, usually around 40 degrees less than the equivalent conventional hot mix. This means practically any asphalt production facility can adopt the technology without physically modifying its production infrastructure.
The technology therefore extends to polymer-modified bitumen. Warm-mix cross-linked PMB is actually available from Total in the form of Total Styrelf Eco2 using the same ready-to-use technology.
Once on site, laying asphalt at significantly reduced temperature gives other considerable advantages over conventional hot mixes.
In contraflow arrangements, traffic is passing surfacing crews as close as a metre away. In humid conditions installing hot mix like this will involve drivers passing through steam emitted from the paver screed and rolling equipment. This reduction in visibility when the workforce is closest to the travelling public is less than ideal. On warm-mix asphalt installations, this hazard is almost completely eliminated with little or no visible steam generated during the paving process.
Also, post installation, the asphalt will reach a temperature suitable for trafficking quicker than conventional surfacing. This, in turn, can allow more work to be completed in a shift. This is particularly efficient when contractors have limited possession of a carriageway under restricted-hours working conditions. Potentially, this benefit allows more layers to be placed or thicker lifts to be installed in the working time available, ultimately reducing the contract programme.
Reducing the time roadworks take is the kind of outcome the contractor, client and, ultimately, the real customer – the travelling public – appreciate.
Conclusion
The introduction of thin-surfacing over the last 25 years offered some initial short-term gains, particularly in noise reduction and installation advantages over traditional materials. The use of higher-performance cross-linked polymerized binders in these asphalts can now offer a long-term risk-reduction strategy offering extra confidence for prudent asset management.
Longer-lasting binder technology offers asset managers increased confidence in achieving the required outcomes throughout a structure’s design life. The use of superior technology does not come cheap, but premature failure is more expensive and politically unacceptable. As in so many areas of life, investing in the best technology available from the outset is often the key to successful procurement.
A change of mindset may be required to make the most of the funds now becoming available for highways investment. Sustainable investment means seeing and treating the local roads network as a £400 billion national asset.
Just as humans require a healthy cardiovascular system to thrive, so the roads need to function with a healthy circulatory system to operate successfully.
The social and economic welfare of the nation depends on how we invest in the highway asset over the coming years. Offering the best chance of extended life to the structure is ‘investing to save’ in the future of the country through the highways.
Total’s product range subscribes to the mantra of ‘sustainability through durability’, facilitating asset management as the industry enters a key phase of the sector’s future.
- Subscribe to Quarry Management, the monthly journal for the mineral products industry, to read articles before they appear on Agg-Net.com