FM Conway Create and Deliver New Asphalt Solutions
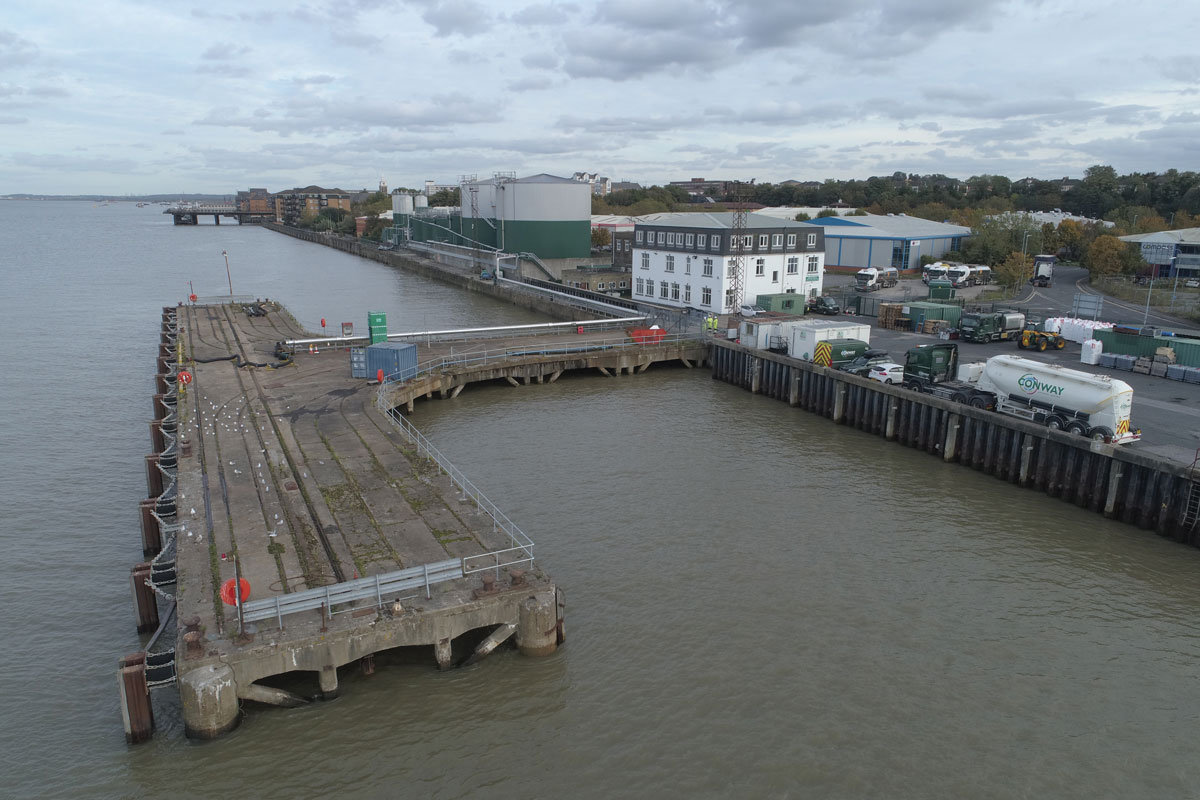
First published in the January 2022 issue of Quarry Management as Pushing the Boundaries
With extensive research and development facilities at their Technology Centre and UKAS-accredited laboratory in Gravesend, Kent, FM Conway are creating and delivering new solutions for clients through their lab-to-lane testing capability. Dan Gilkes reports
FM Conway, one of the UK’s leading asphalt producers, are celebrating more than 60 years in the infrastructure business with further investment in research and development facilities and production plants.
Civil engineer; highways maintenance and drainage management contractor; asphalt, aggregate, and concrete producer; and surfacing specialist, FM Conway have every aspect of the infrastructure construction and maintenance business covered. The company even installs electric vehicle charging points. Yet, despite this holistic approach to transportation and the built environment, many parts of the business remain highly specialized, with more than six decades of expertise and experience to call upon.
‘FM Conway are 60 years old this year and have always been a civil engineering company with an ethos of self-delivery,’ said development director Tim Metcalf, speaking to QM at the end of 2021.
That dependence on its internal supply chain has been core to the company’s success for many years. Being able to not only supply a range of proven materials to site, but also to completely engineer and create new solutions, to perfectly meet the needs of an individual customer, remains a key factor.
To achieve this, FM Conway have seven high-quality asphalt plants, along with their own bitumen terminal and polymer-modified bitumen (PMB) plant, situated around London and the South East. Between them, these sites produce more than 1.2 million tonnes of asphalt per year, with further expansion planned for the future.
‘With the addition of our latest plant at Newhaven, we have witnessed growth and logistical efficiency, optimizing the port for aggregate deliveries into the new facility,’ said Mr Metcalf.
Lab to lane
The asphalt and bitumen terminal sites are not simply producing a menu of proven mixes, however. FM Conway also operate extensive research and development facilities, from their Technology Centre and UKAS-accredited laboratory in Gravesend, Kent. The lab is used to design and test new materials, while also analysing existing mixes, on-site recycled materials, and supplied aggregate and bituminous products.
‘At any one time in R&D we have around 15 projects going through the lab, from standard materials that are being developed, to binders that we manufacture,’ said Lorraine Burton, FM Conway’s laboratory manager. ‘We also have a recycling unit, that carries out weekly checks on materials, while the asphalt plants are checked daily.’
‘The laboratory and the Technology Centre offer our clients something better, enhanced facilities,’ said Mark Flint, head of technical. ‘Product development is 30–40% of what we currently do. We develop a design in the lab and then run lab and road trials, running products through the plants to a trail site, which allows us to make the materials more performance based.’
This lab-to-lane testing capability is allowing a much closer relationship with clients, whether they are internal surfacing divisions from within FM Conway, or external businesses.
‘Ultimately, everything is external, we are working across all sectors. Whether it’s internal or external doesn’t really matter,’ said Mr Flint. ‘We’re making the client part of the decision-making process.’
‘We can be talking to clients and other contractors up to two years ahead of the project,’ said Tim Metcalf. ‘In terms of working with clients, we are starting to see real collaboration in some areas. We’ve also had some ongoing contracts for many years, so we are continually discussing new products with the London boroughs.’
‘Lab-to-lane testing encapsulates what we do. We look after the full process, for us and for the client,’ added Mr Flint. ™
Climate control
One highly topical area that is driving research and development is the global recognition of climate change and the desire to do something about it. This is leading to higher acceptance of warm-mix asphalts and to a requirement to increase the percentage of recycled aggregate in finished materials.
‘Sourcing of materials in terms of carbon footprint has become more and more relevant,’ said Mr Flint.
‘Everyone is talking about warm mix, but not enough are taking it up,’ added Mr Metcalf. ‘FM Conway have been discussing warm mix for a long time and it’s time for us, as an industry, to do more.
‘The laboratory can also help with carbon reduction. Durability, energy reduction and full-life carbon costs are high on our agenda. We’re now looking a step beyond warm-mix asphalt.
‘We’re also seeing a growth and more of an acceptance of recycled asphalt,’ said Mr Metcalf. ‘The challenge in the future could be the supply of enough quality recycled aggregates.’
‘We’ve done trials of up to 50% recycled in surface courses. But the standards have to change to use more recycled product. We’ve proven that recycled material can go way beyond the specifications,’ added Mr Flint.
When using recycled asphalt courses, the laboratory is able to test donor sites for the quality of the aggregate and the bitumen that have been used previously.
‘We do more analysis and testing of recycled material than primary material,’ said Mr Metcalf. ‘We treat the road as the quarry face. However, we have to go further to justify its inclusion in the specification.’
Future focus
The laboratory collaborates with four major UK universities. This is partly to make use of university facilities, to carry out testing that is not always possible within the lab, but it also confirms existing knowledge within the business. The company also sponsors research that will benefit the industry.
‘We do push the boundaries,’ said senior technician and PhD researcher Muhammed Ikram. ‘We’re constantly trying to improve materials; we’re looking at bio-binders and cutting down on the consumption of crude oil-based materials. We look at the carbon footprint across the whole life cycle, including durability.’
This forward-looking approach is also attracting young people into the industry, with FM Conway having no trouble filling the growing number of roles within the Technology Centre and laboratory.
‘We’ve grown significantly over the last three years, and we will continue to do that going forwards,’ said Lorraine Burton.
‘We’ve got a lot of young people at the Technology Centre, people attracted to the industry,’ said Mr Metcalf. ‘The Technology Centre is ever expanding, and we still have room to grow further.’
- Subscribe to Quarry Management, the monthly journal for the mineral products industry, to read articles before they appear on Agg-Net.com