Durability in Roads
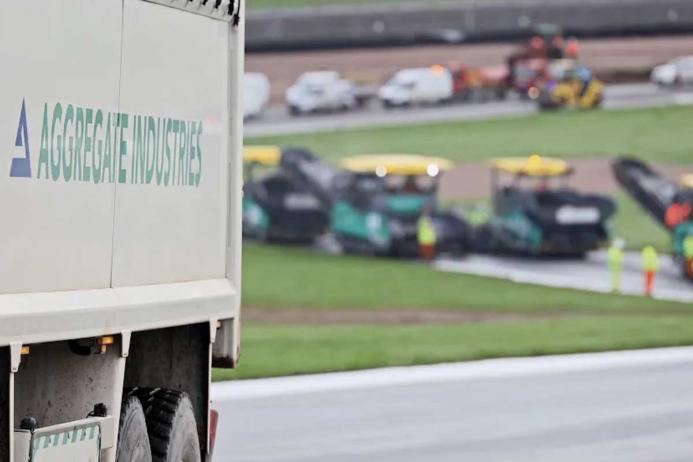
First published in the August 2023 issue of Quarry Management
As the road-building industry continues to come under new pressure to reduce emissions and secure the road to net zero, Neil Leake, national technical manager at Aggregate Industries’ Surfacing Solutions division, explores the importance of durability of design
In a future where it is predicted that by 2060 the UK’s population will stand at nearly 78 million and the nation’s cities will become even denser, transport infrastructure will play an even more critical role in promoting connectivity, trade, and economic growth.
But transport is also the UK’s largest emitting sector, producing around a quarter (24%) of all UK carbon emissions. Moreover, there are already 32 million cars on UK roads, a figure which continues to grow.
In this way, the transition to a more sustainable approach to transport infrastructure is essential to making Britain future-proof and achieving net-zero goals – and road construction and maintenance has a huge part to play.
But while much of the focus here may surround choosing greener – it is also about choosing better. Put simply, it is about going beyond ‘standard’ and strategically opting for more durable, site-specific options that will improve the longevity of a road and extend the length of resurfacing intervals to minimize material need and construction.
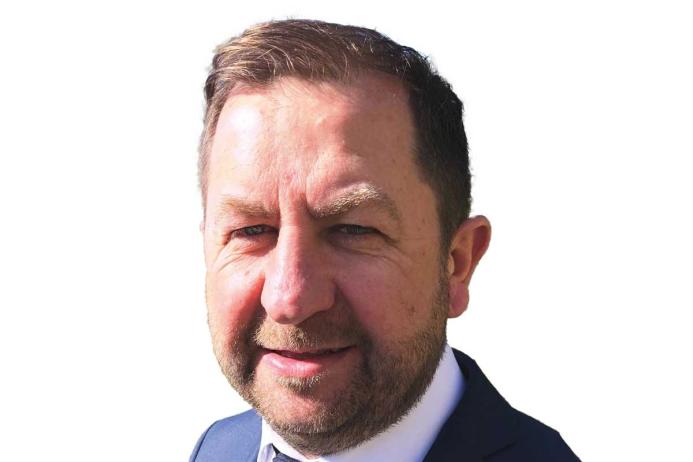
Durable by design
In response, modern high-performance asphalts have been developed to provide proven durability and long-term resistance for specific climate requirements – depending on the location, application, and type of road – to help road operators build roads that last longer.
Aggregate Industries’ ProLay Asphalt solutions have been specifically designed for varying and demanding applications, as different problems demand different solutions. The company’s Clause 942 approved 10mm ProLay Ultra uses high-performing polymer-modified bitumen, which is designed to provide long-term performance and durability for high-speed, high traffic volume roads.
Equally innovative is Foamix, Aggregate Industries’ 100% recyclable, reduced-carbon asphalt which is well suited to the construction, repair, and maintenance of new and existing highways. It is a truly sustainable cold-mix solution for base and binder course layers, which does not compromise on performance, giving equivalent bearing capacity to standard asphalt, with a proven track record for increased cohesion and strength.
There is also SuperLow-Carbon asphalt – the UK’s first commercially available biogenic asphalt. It has been developed in partnership with Shell Bitumen as a pioneering product for more sustainable pavement projects and utilizes a biogenic material which essentially locks in CO2 within the asphalt rather than releasing it back into the atmosphere. SuperLow-Carbon is manufactured at low temperatures, which reduces binder ageing within the product – meaning it remains highly compactable for longer, allowing more time for full compaction, delivering enhanced performance and durability, and ultimately life-expectancy.
What is great about these types of more-durable material solutions is that they not only allow for extended service life of roads and pavements – but also mean better value for money, and, of course, all while being better for the environment.
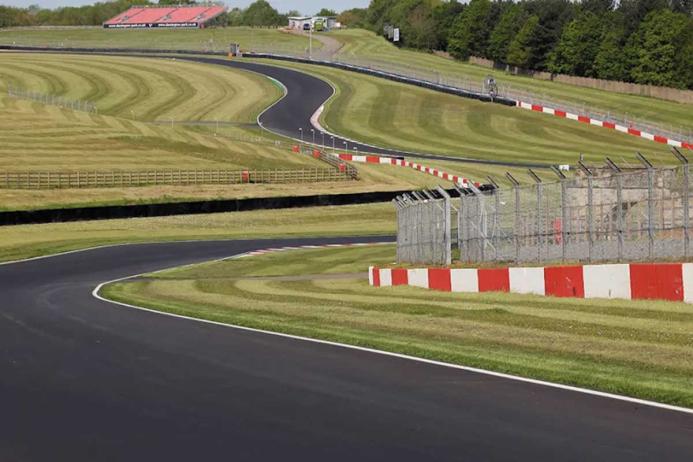
Advanced testing
Whilst the future of road building calls for more durable design, the traditional test methods still used to assess durability are often outdated and not always suitable to evaluate new products.
In response to this, Aggregate Industries continue to push new boundaries in vigorous product testing using the latest advances in technology at the company’s industry-leading Moordale Research and Development (R&D) facility in Derbyshire.
For example, to ensure the exacting level of durability is met for both customers and compliance, the R&D facility now boasts an ‘accelerated weathering machine’, which effectively replicates the effects of environmental conditions, primarily sunlight and water, on the performance of the materials in a relatively short period of time. This allows the team to test each product under intense UV light, for example, to ensure the quality or performance of the product does not degrade over time.
As part of our future focus, we are also looking at alternative polymers and chemical additives to enhance the life of our materials to ensure long-term performance and its ability to stand the test of time.
Durability in action
A great demonstration of the importance of durable road design can be found in Aggregate Industries’ recent involvement in the extensive resurfacing works of one of the world’s most iconic race venues, Donington Park.
Through early contractor engagement along with extensive track profiling, material trials and testing, the company was able to develop a bespoke and highly sophisticated solution that meets the durability requirements of the famous track.
This included more than 5,000 tonnes of the well-established SuperPrixmat Ultra surfacing material, which is specifically designed for demanding high-performance motor racing circuits and has been used on many of the UK’s major performance tracks. The aggregates used within the product provide a high-grip surface solution for high-speed racing.
In addition, Aggregate Industries installed 846 tonnes of binder course and 740 tonnes of stress-absorbing membrane interlayer, SuperSAMI, which is used to reduce reflection cracking.
With the high-performance specification laid using advanced construction methods, a superior level of grip (0.6) was achieved immediately. An average International Roughness Index (IRI) of less than 1.0 was specified, however a tight tolerance of 0.3 was achieved around the track – an exceptional result.
Indicative of its exceptional performance, the new surface on the course has received praise from the UK’s top British Touring Car Championship drivers and Bennetts British Superbike Championship (BSB) riders, with comments on increased grip, in both dry and wet conditions, and smoothness of the course.
Driving force
Choosing long-lasting material options is imperative to the sustainability of any road-building project. After all, it has the potential to change everything in terms of reducing the number of natural resources used to maintain road networks, decreasing the traffic disruption caused by road maintenance processes, and reducing the CO2 emissions during the maintenance process itself. Thus, as the industry comes under pressure to take bolder climate action, it is imperative that durability is more widely recognized as a key driving force.
Subscribe to Quarry Management, the monthly journal for the mineral products industry, to read articles before they appear on Agg-Net.com