Driving Innovation in Asphalt Technology
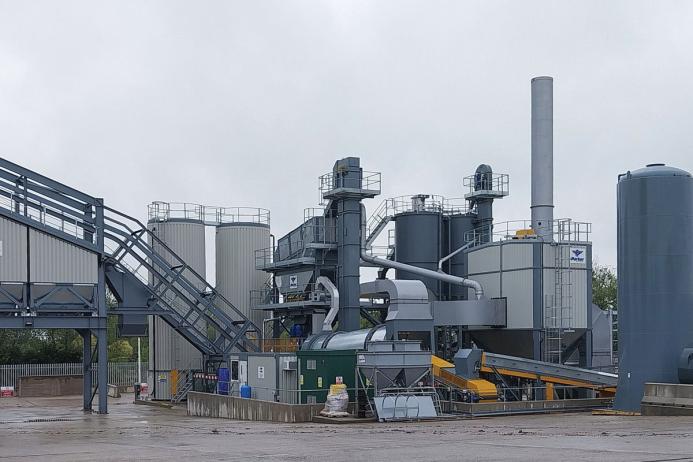
First published in the January 2024 issue of Quarry Management as The Circular Economy
Scott Jones, director of Asphalt and Paving Solutions for Cemex EMEA, talks about how the circular economy is driving innovation in asphalt technology to meet decarbonization targets
UK roads and highways are constantly in the spotlight. The ongoing need for essential maintenance, construction, and continual improvements make them a popular source of conversation, conjecture, and scrutiny. Latest developments in smart technologies, from electrification to wireless integrated road systems, are just a few examples that reinforce the constant and continuous need for the sector at large to innovate. In the construction supply chain, this influence, coupled with the need to meet critical climate action goals, has in recent times seen an even stronger focus on ways to make the UK’s new and evolving road infrastructure safer, more hardwearing, and more sustainable.
Significant leaps in technology have been made in road construction materials over the last few years with new developments coming thick and fast. At Cemex, sizeable investments in the circular economy have given rise to the emergence, development, and introduction of numerous asphalt technologies, as part of the company’s Future in Action climate action strategy.
Cemex believe a circular economy is essential for environmental sustainability. By transforming waste materials into invaluable solutions, carbon emissions are reduced, and other environmental benefits delivered. What would have been considered ground-breaking experimental materials and techniques only a few years ago, are now becoming commonplace in the quest to support customers with their carbon footprint reduction programmes.
Asphalt plays a key part in Cemex’s Urbanisation Solutions product portfolio, which has a continuous focus on bringing more sustainable solutions to market to help meet the challenges of modern urbanization. As an organization, we have been working hard in this field and in the last 24 months have made some significant headway. We have invested heavily in the development of new solutions used in our road-surfacing operations across Europe, but particularly in the UK where demand is highest.
Cemex invest in UK asphalt business
Cemex have recently introduced a significant investment programme in their UK asphalt operation. This includes the opening of a new plant in Birmingham, as well as developments at several other locations to ensure a more efficient and more sustainable operation with smoother product delivery for customers. The new Birmingham plant, located on Doris Road, allows the company to better target this key urban market with its array of asphalt solutions.
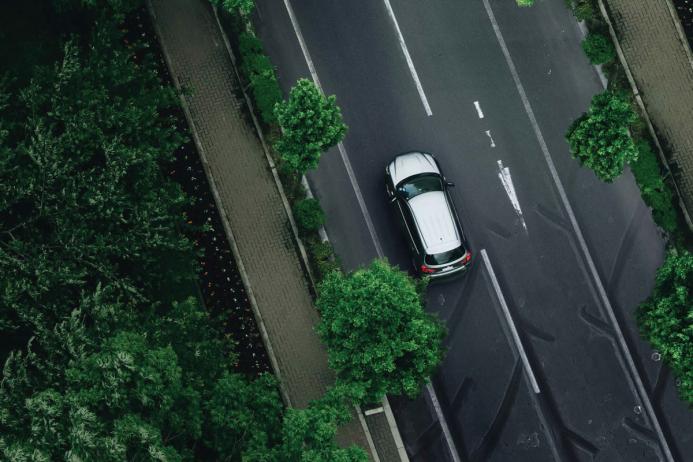
Products produced on site will include RubberMix asphalt (RMA), which incorporates crumb rubber granules taken from used tyres into the mix, helping to offset the environmental impact of highway maintenance activity through the circular economy; and Vialow, Cemex’s low-temperature, reduced-carbon asphalt, which comes with the option to offset residual CO2 to make it a CarbonNeutral product, in accordance with The CarbonNeutral Protocol. Further trials are under way on other more sustainable asphalt products that prioritize circularity.
The new Birmingham site will now operate as a ‘Local Asphalt’ plant, providing a dedicated service for customers that require small tonnage collections and deliveries, stocking everyday essentials such as the tools and equipment needed to provide a first-class service.
Further investment has been made into the wider Cemex UK asphalt business, with the installation of multiple new bitumen tanks at Cemex’s Stourton, Preston, and Dove Holes plants. These tanks have a higher capacity than those previously in place, which will enable increased production speed, increased mix options, plus a more flexible supply.
Additionally, the new tanks are more energy efficient, helping Cemex to run a more sustainable operation, in line with their dedicated climate action strategy, Future in Action. This is the latest stage of Cemex’s plan to replace all the bitumen tanks at their UK asphalt locations with newer, more efficient models. The company was recently recognized by the Mineral Products Association for its bitumen system management, winning a Health and Safety award at last year’s ceremony.
Cemex extend Vertua range of more sustainable asphalt solutions
With more sustainable products and solutions playing a critical role in the construction industry’s decarbonization journey, Cemex have extended their Vertua portfolio of more sustainable products to include a comprehensive range of asphalt solutions. Cemex’s Vialow, Viaflow, and Viacourt asphalts now form part of a new series of high-performance asphalt solutions which have been stringently classified to join the Vertua product family.
All Cemex products which carry the Vertua brand must meet strict criteria for at least one of five sustainable attributes, ranging from lower carbon emissions, increased energy efficiency, and water conservation, through to the incorporation of recycled materials and design optimization. These attributes have been identified in line with Cemex’s dedicated Future in Action climate action strategy.
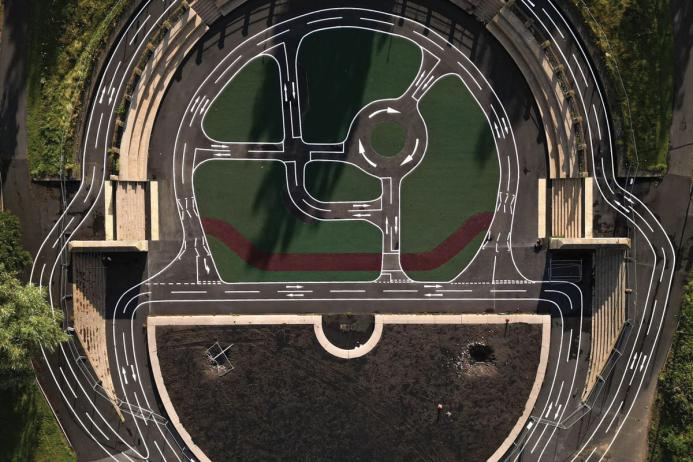
Lower-carbon asphalt technology at Everton Park community project
Cemex recently helped to deliver the successful completion of an innovative carbon-reduction regeneration project at the historic Everton Park, in Liverpool, to provide a brand-new community cycling facility.
Funded by both Liverpool City Council and British Cycling, an under-used part of Everton Park has been transformed into Liverpool’s first purpose-built children’s learn-to-ride facility. The £380,000 ‘Mini-Roads’ scheme was delivered by highways contractor Dowhigh Ltd, working in close partnership with Cemex and Shell Construction and Road, to realize the partnership’s first successful large-scale application trial of Shell’s Bitumen CarbonSink, a new bio-component binder which locks carbon into asphalt.
Shell Bitumen CarbonSink reduces carbon footprint by up to 250kg carbon dioxide equivalent per tonne of bitumen. The solution involves the addition of biogenic components engineered to ensure bitumen compatibility that will not compromise the performance characteristics of asphalt. The end result is an asphalt pavement that can be recycled whilst also retaining captured bio-carbon in the long term.
As well as reclaiming and recycling existing materials on site to re-use in the new road construction, Cemex’s RubberMix asphalt was supplied to help offset the environmental impact of highway maintenance activity through the circular economy. Asphalt containing Shell Bitumen CarbonSink will be offered to future customers as part of Cemex’s Vertua products and solutions.
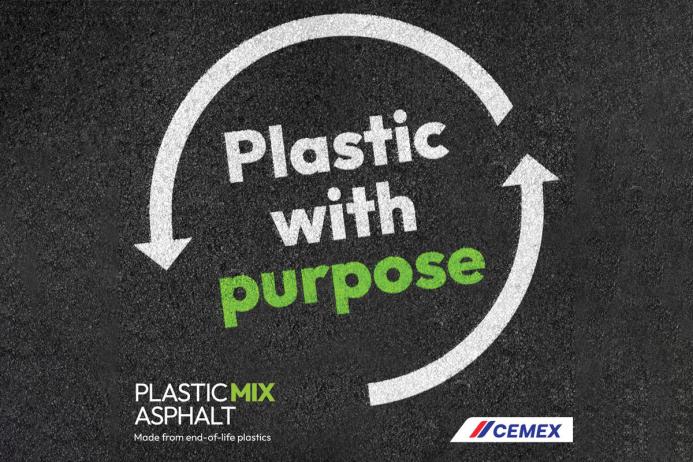
PlasticMix asphalt
Cemex’s latest development in the asphalt range is the introduction of PlasticMix asphalt (PMA). This product comprises a more sustainable asphalt solution that uses non-recyclable plastic waste to help reduce the amount of plastic that ends up in landfill or being burnt in incinerators, which, in return, reduces carbon emissions.
PlasticMix asphalt utilizes non-recyclable plastic waste and gives it purpose, using it to construct vital infrastructure for local communities, including supermarket carparks, local roads, industrial areas, and essential road maintenance.
At Cemex, we are committed to developing a more sustainable approach to highway maintenance and construction, as we continue to invest in circularity, by incorporating waste sources from other streams into our materials. In tandem, we are focused on the advancement of our portfolio of lower-carbon asphalt urbanization solutions to meet customer and environmental demand; ultimately building a better future for everyone.
Subscribe to Quarry Management, the monthly journal for the mineral products industry, to read articles before they appear on Agg-Net.com