Building Roads of the Future
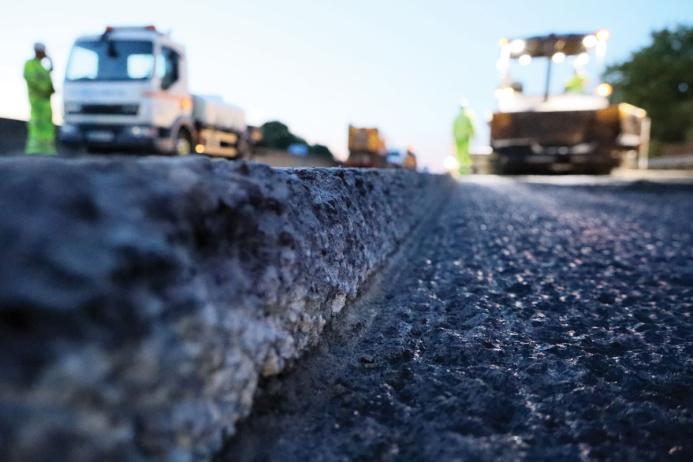
First published in the January 2024 issue of Quarry Management
As climate change, urbanization and soaring car ownership continue to fuel a new age of sustainable road infrastructure, Neil Leake, national technical manager at Aggregate Industries’ Surfacing Solutions division, explores the innovations that are making it possible
In a future where it is predicted that by 2060 the UK’s population will stand at nearly 78 million[1] and the nation’s cities will become even denser, transport infrastructure will play an even more critical role in promoting connectivity, trade, and economic growth.
But transport is also the UK’s largest emitting sector, producing around a quarter (24%) of all UK carbon emissions[2]. Moreover, there are already 32 million cars on the UK’s roads, a figure which continues to grow[3].
In this way, the transition to a more sustainable approach to transport infrastructure is essential to making Britain future-proof and achieving net-zero goals – and, as the most widely used form of transport, road infrastructure must take a lead role.
But, while much of the focus to date has hinged on the future mobility vision and electric vehicle (EV) adoption, it is equally important not to overlook the carbon impact of building and maintaining the UK’s road infrastructure itself.
Inherently, the road building process can involve a number of direct and indirect carbon sources. This includes the construction methods used and the embodied carbon in concrete, asphalt, steel and other materials used to build road schemes, through to the emissions from construction vehicles – all of which can weigh up to a considerable carbon impact.
Thus, as the century-old transport industry transitions to a more sustainable future, it is increasingly important that the road-building sector follows suit – but how?
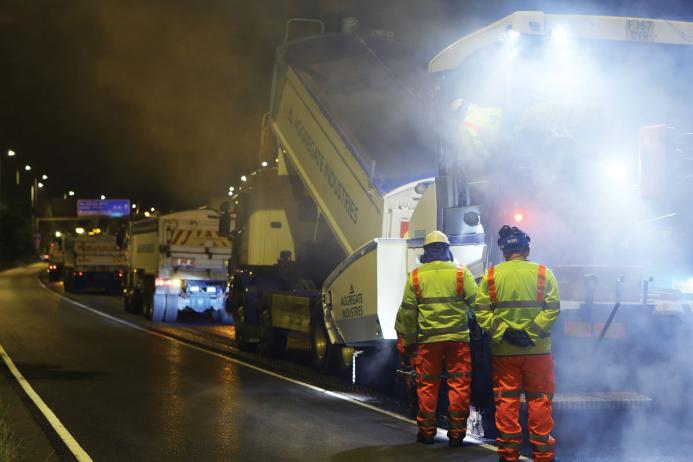
New kids on the block
The good news is that there are already many greener construction material options which have been purposefully designed to drive change and help deliver road construction with greater focus on sustainability.
At Aggregate Industries, for example, we have developed Foamix – a reduced-carbon asphalt that is 100% recyclable and offers a truly sustainable solution. Made from 92% recycled materials, including 85% reclaimed asphalt pavement (RAP), Foamix promotes a circular economy approach to road construction by drastically reducing the requirement for virgin aggregates. As it is manufactured as a cold mix, with the ‘ingredients’ carefully bound together by a ‘foam’ of bitumen and water, it promotes a low manufacturing carbon footprint too.
Moreover, thanks to Aggregate Industries’ mobile mixing plants, it can be manufactured on site, allowing customers to source planings locally – thereby minimizing HGV movements across the local road network, construction times, and user disruption, as well as delivering a significantly lower scheme carbon footprint.
Alongside this, Aggregate Industries recently announced another significant commitment to reducing both their own and their customers’ carbon footprint. We will now be supplying warm-mix asphalt as the company standard. The result is that customers can unlock the full raft of environmental benefits associated with warm-mix asphalt – including reduced emissions and increased efficiencies – without any compromise to performance or having to pay over the odds for a greener product. The result is a huge opportunity to reduce environmental impact.
An innovation consideration
But creating more sustainable road building is not just about choosing greener – it is also about choosing better. Put simply, it is about going beyond ‘standard’ and choosing more durable, site-specific options that will improve the longevity of a road and extend the length of resurfacing intervals to minimize material need and construction.
In response, modern high-performance asphalts have been developed to provide proven durability and better performance – depending on the location, application, and type of road – to help road operators build roads that last longer.
Aggregate Industries’ ProLay asphalt solutions have been specifically designed for varying and demanding applications, as different problems demand different solutions. Clause 942-approved 10mm ProLay Ultra uses high-performing polymer-modified asphalt which is designed to provide long-term performance and durability for high-speed, high-traffic-volume roads.
Equally innovative, is ProLay Curve, a high-performance 10mm product designed and engineered to provide an enhanced surface course for higher-stressed areas.
What is great about these types of more durable material solutions is that they not only allow for increased service life of roads and pavements, but also mean better value for money, all while being better for the environment.
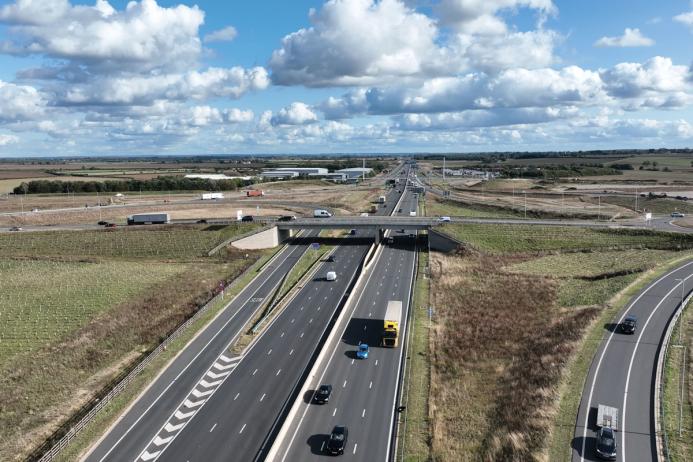
Further down the road
However, this is just part of the story. If the road infrastructure sector is to keep its net-zero ambitions in sight while continuing to serve the current need, it will require even greater climate-relevant innovation – and fast.
In response to this, Aggregate Indutries continue to push new boundaries in product development and testing using the latest advances in technology at the company’s industry-leading Moordale Research and Development (R&D) facility in Derbyshire. But there is more.
As a member of Holcim, we have access to their industry-leading R&D centre in Lyon, France, where more than 200 world-leading academics continue to push the boundaries of innovation and lead the way in sustainable construction solutions and processes. The result is a constant churn of research, collaborative working, and continuous improvement of existing products and processes – both regionally and globally.
In terms of road surfacing, one example of continuous R&D is the use of bio-binders. Inherently, a large chunk of the carbon impact associated with road building comes from the bitumen – a by-product of oil production – which is used to bind the surfacing materials. Bio-based binders not only demonstrate a significantly lower carbon footprint, but a key aspect is that they can ‘lock-in’ CO2 and ensure it is not released back into the atmosphere, even when the asphalt is recycled. In addition, the bio-binder solutions we have currently under way have been designed to enhance durability and further extend the life of the asphalt, thus reducing the frequency of maintenance interventions.
Another big innovation focus for Aggregate Industries is self-healing asphalt. As we all know, the ongoing maintenance works associated with traditional road builds is not only uneconomical but carbon intensive. To counter this, the adoption of self-healing asphalt – able to repair itself without external intervention – for maximum durability has the potential to change everything. This is because it inherently reduces the number of natural resources used to maintain road networks, decreases the traffic disruption caused by road maintenance processes, and reduces the CO2 emissions during the road maintenance process – in the ultimate win-win.
We also continue to investigate new ways to capture and redeploy the CO2 associated with aggregate processing. A great example of this can be found at our Cauldon cement plant where we have joined a major new carbon-capture initiative which aims to capture and transport carbon dioxide emissions from the site to be permanently locked away beneath the east Irish Sea. We also continue to seek new opportunities to redeploy captured carbon and convert it into new products, which offers the benefit of further mitigating climate change and generating economically viable products.
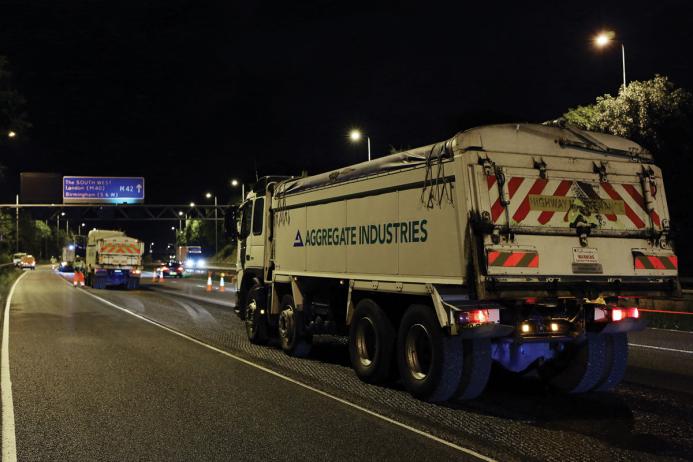
Alongside this, we remain committed to revolutionizing our means of production and construction through investing in clean energy sources, such as solar and wind, to eradicate the carbon impact associated with traditional energy, whilst also enabling new opportunities for self-generation. As part of this, we are currently investigating novel microwave heating technology as a much more effective and sustainable asphalt maintenance approach, thanks to its unique self-healing capabilities.
Looking at the bigger picture, we realize that the road industry is changing too, as it moves towards a future mobility vision of widespread electrification. With this, our parent company Holcim recently unveiled a new magnetizable concrete technology that allows electric vehicles to charge wirelessly while moving along the road surface. Known as ‘inductive charging’, this breakthrough solution reduces the need for charging stations, whilst saving time – and will come as a major asset in the transition to EV adoption. As a group, this continues in our commitment to driving the innovation needed to put concrete at the centre of our world’s transition to net zero.
Importantly, too, what is great is that all regions have access to the full scope of Holcim innovation. Put simply, in the UK this means that Aggregate Industries’ customers are able to take advantage of our global innovation first and work with our UK R&D team or even our wider global R&D hub to develop the specific, bespoke solutions needed to meet their requirements – no matter how big or complex.
Driving change
As EV and other new mobility breakthroughs continue to generate higher sustainability standards for the transportation sector, it is important that the road construction sector is not left behind and continues to raise the bar too, with its own bold and rigorous climate-relevant action.
Of course, Rome was not built in a day and the ‘roads of the future’ will not happen overnight either. But, by taking advantage of the latest advances in material innovations and processes designed to be more environmentally resilient and durable, and also proactively taking the opportunity to invest in innovation, road construction can make a huge carbon-reduction impact today and help drive the change needed for a greener future.
REFERENCES
The Standard: ‘Britain’s population timebomb: By 2060 there’ll be just two workers for every pensioner’
GOV.UK: Transport and environment statistics 2022
RAC Foundation: Motoring FAQs – Mobility.
Subscribe to Quarry Management, the monthly journal for the mineral products industry, to read articles before they appear on Agg-Net.com