Bitumen Tanks Remain Cool Under Pressure
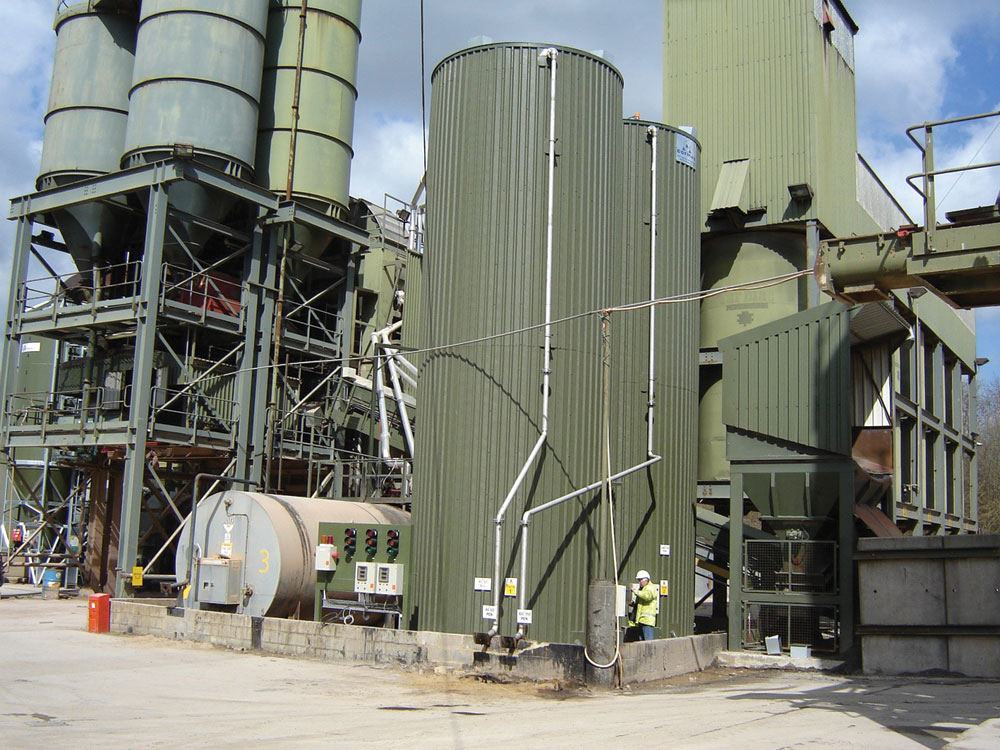
The quarrying industry has traditionally been a large user of energy and consequently management is constantly targeting areas of high-energy consumption, in particular asphalt and coating plants, in an effort to reduce costs. By its nature bitumen needs to be transported and stored at elevated temperatures. As a result, storage tanks can act as giant radiators if not suitably insulated, using large quantities of energy and adding, in their small way, to global warming.
Now, however, a significant development in bitumen storage tank design is bringing important energy- and cost-saving benefits to asphalt manufacturing plants throughout the UK and Ireland. In parallel, the new tank design is improving bitumen logistics while enhancing safety by incorporating an RBA (Refined Bitumen Association) compliant fail-safe safety system to prevent overfilling and spillages.
During the past decade Glasgow-based Cormac Ltd have built a strong reputation in the design and installation of vertical and horizontal bitumen tanks. In response to customer demands and an internal drive for continual product development, the company have recently undertaken an in-depth 15-month program to identify ways of further improving their products, with a strong emphasis on optimizing energy efficiency and safety. Through the application of sound engineering principles, including thermography to identify any unwanted hot spots, the company have been successful in significantly reducing the transfer of heat from the inner tank to the outer cladding. This in turn minimizes the amount of energy that is needed to maintain an optimum storage temperature for the bitumen. The new tank design uses a combination of traditional insulation materials combined with a special reflective thermal coating, which together produce significant energy savings compared with a conventionally clad tank. To back up their findings, Cormac commissioned a study with the Energy Department of Stathclyde
University, which confirmed that the new tanks reduce energy consumption by over 50%.
Cormac’s managing director, Steve Corbett, explained: ‘The tests carried out by the University on one of our 100m3 tanks show that users should be able to benefit from an annual energy saving of over 40,000kWh, which at current energy costs equates to savings of over £4,000 a year. To reduce energy consumption even further, our tanks are fitted with proprietary progressive multi-stage heating systems, which maintain the temperature of the bitumen within a preset bandwidth. Based on this, we are confident that the new tanks will pay for themselves twice over during their lifetime.’
Safety in numbers
Energy efficiency is not the only area to come under scrutiny by Cormac engineers; plant safety is given an equal priority during design considerations. Great efforts have been made over the past few years to reduce injuries caused by bitumen spillage and Cormac have worked closely with a leading bitumen level measuring specialist to develop their RBA-compliant level-based safety system. This now comes as standard with all tank installations and is helping to make a significant impact on improving operator safety.
The safety control equipment incorporates a special bitumen TDR guided-radar continuous tank level measuring system and an independent high level alarm probe. Measuring levels in bitumen tanks is notoriously difficult, as the hot vapour rapidly coats anything in the tank with bitumen, rendering some level systems inaccurate or ineffective, sometimes in a matter of days. In contrast, the Cormac TDR system continues to give reliable results even when the stainless steel conductor cable becomes coated. The system uses data from the TDR sensor to provide an early warning high level alarm (HLA) set at 90% of the available tank contents, while an independent ultimate high level alarm is set 2.5% higher, providing a ‘belt and braces’ warning should anything fail or affect the reading from the TDR.
The control panel clearly displays the current bitumen level in the tank, the total available space left in the tank (ullage) and the current bitumen temperature, taking into account the RBA recommendations that 10% of the available tank level must always be kept empty. A simple, unambiguous traffic-light system, which uses multi-LED technology for bulb redundancy and increased brightness, clearly shows the tanker driver the status of each tank. A green light means the entire tanker can be safely discharged, while amber or red lights indicate either the HLA or ultimate high level alarm has been initiated. If for any untoward reasons the early high level alarm is reached during the filling process, an amber beacon at the control panel and the amber traffic light flash together with an audible warning, giving sufficient time to shutdown the fill procedure and safely blow the tanker lines clear. However, even if this fails, the independent high level probe alarm will still provide ample warning to prevent overfilling.
Size matters
Traditionally, bitumen tanks were designed to hold the contents of a single tanker. However, this can put strain on both the asphalt plant operator and the supplier, while making it difficult to comply with recommended safety guidelines.
Smaller tanks can no longer accommodate full loads from today’s larger tankers and so, in order to improve bitumen logistics, Cormac have developed tanks up to 340m3 capacity. These can be heated using a variety of sources including electricity, thermal oil, steam and renewable energy. The ability to store larger quantities of bitumen allows asphalt plants to even out their delivery requirements, removing the need for traditional early morning deliveries.
To further enhance their tank installations, Cormac are now offering remote inventory management (RIM) and vendor-managed inventory (VMI) capabilities. RIM and VMI systems have grown in popularity over the past decade, providing security and flexibility for the management of raw materials and finished products. Manufacturing sites rely on raw material availability, and optimizing stock holding versus cost is essential for uninterrupted profitable productivity. The system is based around the Webflex web-enabled remote monitoring and data-logging terminal, which brings a new dimension and transparency to the concept of remote inventory monitoring.
‘We are working closely with customers and the authorities to ensure we provide more competitive products, which run more efficiently, reduce energy costs and continue to improve safety,’ said Steve Corbett. ‘By achieving this we can offer our customers the ultimate in bitumen-management systems and do ‘our bit’ for global warming at the same time.’