Understanding the Standards
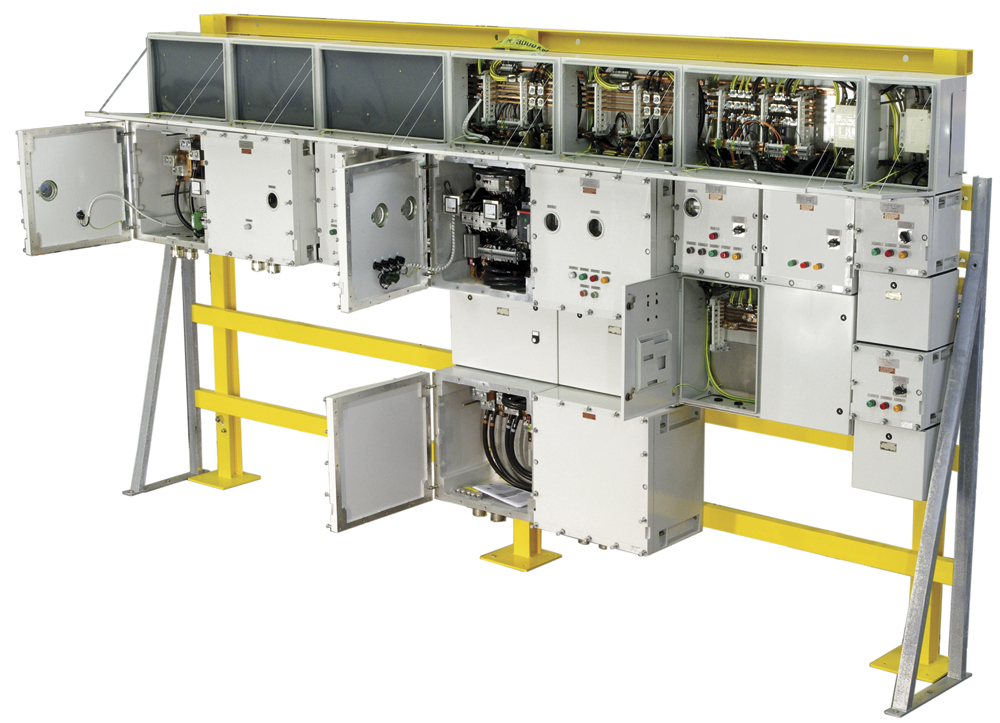
When specifying explosion-proof (Ex d) enclosures to house electrical apparatus for use in explosive atmospheres, engineers must ensure they fully understand the implications of modifying the enclosure prior to and after installation, says Toni Ott, test, certification and patents manager at Cooper Crouse-Hinds GmbH
When sourcing Ex d explosion-proof enclosures to house electrical apparatus for use in potentially explosive atmospheres, it is critical that end-users and installers fully understand the implications of modifying such enclosures. It is important that end-users fully appreciate what they are allowed to do with an Ex d enclosure so as not to invalidate the certification of the equipment.
The primary function of an Ex d enclosure is to prevent the propagation of an internal explosion to the surrounding explosive atmosphere, as well as protecting the internal components from the environment, humidity, dirt, dust or water. With Ex d flameproof enclosures, it is critical that the flame path is not damaged. The external enclosure of any flameproof electrical equipment is designed to withstand an internal explosion. The enclosure joints permit and control the resulting expansion of flames and hot gases, as these are relieved through the joints, preventing the explosion from being transmitted to the external atmosphere. The relevant European (EN 60079-1) and International standards (IEC 60079-1) in addition to EN/IEC 60079-0 ‘General Requirements’ apply.
In Europe, manufacturers and end-users have to consult two directives: Directive 94/9/EC covers equipment and protective systems intended for use in potentially explosive atmospheres (ATEX) and is for manufacturers of the equipment; while for end-users Directive 1999/92/EC ‘Risks from Explosive Atmospheres’ (December 1999) outlines and harmonizes the minimum requirements for improving the safety and health protection of workers potentially at risk from explosive atmospheres. There is no directive covering the middle ground, ie modifying an existing Ex d enclosure. Once Ex d equipment has left the manufacturer and their quality system (requirement to affix the CE mark on the type label), responsibility no longer lies with the manufacturer but with the end-user.
Common pitfalls
Increasing awareness of relevant standards and education are fundamental. Mistakes occur for a variety of reasons, such as lack of knowledge or inexperience. One of the most common mistakes made by end-users and installers is to drill new cable gland entries into an Ex d enclosure prior to or after installation. If space allows, an end-user may decide to fit additional components into the enclosure, such as a switch or an additional component with relevant power loss. This type of modification can affect the temperature class rating of the equipment enclosure or could lead to the overheating of other components inside the box, which, in turn, may result in component failure or give rise to an ignition source. In addition, these modifications could weaken the mechanical integrity of the enclosure or lead to altered flame propagation within the enclosure, in excess of the maximum permitted reference pressures. Also, the results of the flame- transmission test performed during the EC-type examination procedure could be negatively affected and a possible internal ignition may not be safely isolated from the external explosive atmosphere by the existing flameproof enclosure.
According to Directive 94/9/EC, only the manufacturer should carry out such modifications. If the modification is carried out by another party, without the control of the quality management of the original manufacturer, the marking on the equipment is no longer valid.
Therefore, if any modifications are made to an Ex d enclosure that are not within the responsibility and agreement of the equipment manufacturer, only two options exist:
- New EC-type examination certificate with new type label is the responsibility of the legal entity modifying the equipment; or
- The end-user takes full responsibility which means they also become responsible for any subsequent failures of the enclosure that could lead to serious health and safety risks.
Another potential risk when modifying an Ex d enclosure is accidental damage to the flameproof gap. When opening a heavy enclosure, which typically involves unscrewing fasteners and lifting the cover, maintenance technicians must be careful not to inadvertently scratch or damage the flanges or threads. The cover should be lifted slowly and smoothly off the enclosure.
Painting an Ex d enclosure, particularly if paint gets in and around the flame gap, can adversely affect the certification. Also, screws that are painted over can prevent access to the box. As paint is typically non-conductive, this can also lead to electrostatic hazards and introduce a new ignition source.
Fastening the screws to the wrong torque or forgetting to replace screws is another common mistake when placing the cover back on an Ex d enclosure. This is particularly important on Ex d gas group IIC enclosures (including IIB + H2), where the tolerance of the flameproof gap is typically down to 0.1mm. It is critical that all screws are tightened to the correct torque as specified by the manufacturer. If this is not done the cover can bend and lead to an uneven flame gap. The same problem exists for IIB and IIA enclosures.
With flame gaps, the impact of grease is also important. Often, there are misunderstandings among end-users and installers about which greases should be used with an Ex d enclosure. In general, the grease that should be used is the one recommended by the manufacturer. The message is clear in all cases – if in doubt, consult the enclosure manufacturer for advice and guidance on grease selection. The grease recommended by the manufacturer will have been tested at the applicable ambient temperature range. Incorrectly selected grease may harden at low temperatures or may turn into an adhesive at higher ambient temperatures.
When consulting relevant standards, EN/IEC 60079-19 provides end-users with technical instructions on the repair, overhaul and modification of equipment designed for use in explosive atmospheres, while for the design, selection and erection of electrical installations in explosive atmospheres, EN/IEC 60079-14 is the relevant standard.
After an Ex d enclosure has been installed correctly, EN/IEC 60079-17 outlines the principles that the operator should adhere to in terms of maintenance (inspection, service and repair) of the equipment, including advice on the issue of safe work permits.
Certification tests
Buyers of Ex d enclosures should also be aware of the certification tests involved. The tests to be performed are defined in EN/IEC 60079-0 (general requirements) and in EN/IEC 60079-1 for the type of protection ‘flame-proof enclosure’, known as ‘Ex d’.
For all types of Ex d equipment, thermal tests are conducted to determine the maximum surface temperature of the complete equipment (enclosure and inbuilt parts) under maximum service conditions (with an additional safety margin). Thermal endurance to heat and cold (non-metallic enclosures or parts of enclosures) is also tested, and impact tests are always carried out on critical parts. Tests to prevent an electrostatic ignition source from becoming effective are also performed.
Additional tests that are normally carried out for Ex d enclosures (EN/IEC 60079-1) involve reference pressure, overpressure and flame transmission. Additional tests are necessary for light-transmitting parts made from glass or breather plugs.
The reference pressure tests involve filling the enclosure with an explosive mixture of gas and igniting it. The reference pressure depends on the lower ambient temperature (the lower the temperature, the higher the reference pressure) of the enclosure and of the geometry to be found within the enclosure. After these tests, a hydrostatic overpressure test is conducted to verify the mechanical strength of the enclosure.
Following overpressure tests, the enclosure is also subjected to a series of flame-transmission tests, using a similar explosive mixture of gases as before. The enclosure is also placed in an explosive atmosphere. When the internal explosive mixture is ignited, it is not permissable for this to transmit through the flameproof joints to the outer external atmosphere. Flame propagation depends on the upper ambient temperature of the enclosure/equipment and on the internal geometry. When exceeding the given ambient temperature range stated by the manufacturer, the equipment will typically no longer be safe. The same is true for the mechanical integrity of the enclosure when exceeding the lower ambient temperature. Modifying the internal dimensions, especially when reducing the cross-sectional area, will have a similar result.
For enclosures that have an ambient temperature range higher or lower than –20°C to +40°C, the reference pressure overpressure and flame transmission tests may be conducted at the extremes of low and high ambient specified by the manufacturer.
Sometimes complete Ex d assemblies are put on to the market with just a ‘U’ at the end of the certificate number. This shows that only the empty enclosure has been certified, not the complete assembly. Typically, the temperature class is not shown on the type label because the heat loss of internal components is not known by the manufacturer of an empty Ex d enclosure.
Conclusion
Before starting any work on an Ex d enclosure, end-users and installers should first ensure that they understand and recognize the relevant standards, and have read the instruction manual(s) provided by the manufacturer. To avoid uncertainty, end-users should always buy complete Ex d equipment from the company that owns the certification.