The Importance of Stockpile Dewatering
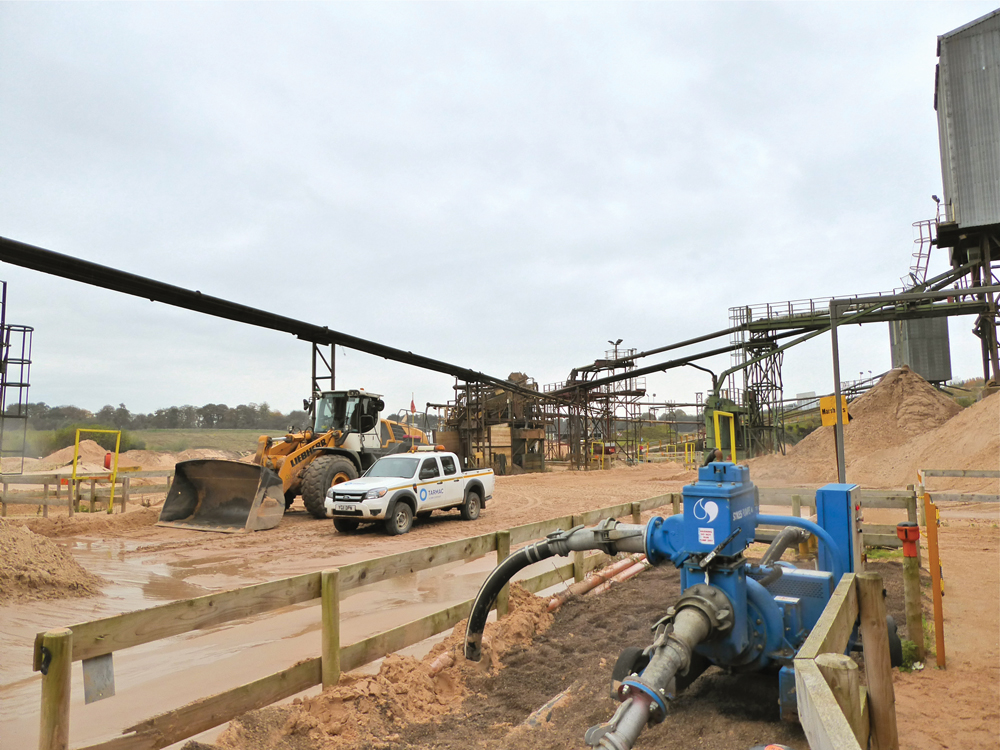
First published in the December 2016 issue of Quarry Management as All Pumped Up and Ready to Go
Stockpile dewatering is a crucial part of the site operations at many quarries. Joseph Priest of hire specialist Sykes Pumps outlines the importance of the process at Tarmac’s Eaton Hall Quarry, in Cheshire, where an electric pump supplied by Sykes has recently passed a two-year milestone of 24/7 operation without a single defect or downtime incident.
Eaton Hall in Congleton, Cheshire, is home to no ordinary quarry. The Tarmac-owned site is the source of superior silica sands and the company supplies a wide customer base with an array of these industrial sands for a range diverse applications. Chemically purer and more even-grained than construction sand, and containing a high proportion of silica in the form of quartz, silica sand is an essential raw material for the glass and foundry industries, as well as other for industrial applications including ceramics, chemicals and water filtration.
Silica sand extraction is concentrated in certain areas in the country with the north-west region of England accounting for nearly half of total UK output. Cheshire plays an important role both regionally and nationally in the supply of silica sand to the glass and foundry industries. With silica content in excess of 96% and predominantly rounded grains, the Eaton Hall silica sands are widely recognized as among the best in the UK for foundry core and mould production.
The production process
Sand is transported from the extraction area, either by pipeline or conveyor, to a central processing plant where it is washed, screened, classified, drained and dried to suit the required product specification and market. The sand’s quality and the temperature of the product on delivery are critical. In the case of sand for glass manufacture and foundry purposes, continuous 24h processing allows delivery around the clock.
Hire specialists Sykes Pumps are on hand at Eaton Hall to play their part in the drying process, removing excess water from the dredged sand before it is dried. ‘It’s essential that we reduce the moisture content, not only prior to us loading the sand on to delivery lorries, but also before we send the sand to the driers,’ explained Eaton Hall’s quarry supervisor, Andy Gibson.
‘If we send wet sand up to the driers, you are looking at in excess of 10 litres of fuel per tonne of sand to get it to the desired moisture level. By using a Sykes pump to remove excess water before it goes to the drier, we can get that fuel consumption down.’
The operation is simple yet effective. Sand is dredged from a lake at a quarry and goes through screening and classification processes according to the specification being produced on the day. Different industries require different grades of sand, with exacting standards.
No sieves used in the classifiers, instead the separation is achieved by water pressure. ‘At the bottom of the classifiers are spray bars,’ explained Mr Gibson. ‘High-pressure water is directed downwards and this is used to float the fines. Basically, the sand that we don’t want to collect floats up and over into a pipeline to an adjacent classifier.’
The silica sand remaining is now of the correct specification for collection. This exits the classification tower down a chute to be dumped on to the floor as a wet sand stockpile. Beneath the stockpile is a mass of underground pipes – laid out in similar fashion to an underfloor heating installation – which is connected to the pump supplied by Sykes Pumps.
‘We handle 1,500 tonnes on each chute from the classifier, and the pump runs 24h a day, seven days a week, to draw moisture out of the sand,’ said Mr Gibson. The pump’s vacuum draws the excess water through the underground pipe network and discharges it into a fresh water lake, at a maximum flow rate of 90 litres/s. This on-site lake supplies water for reuse through the spray bars, as well as for other processes at the quarry.
The dredged sand has a moisture level of around 13% when it comes in for processing, which is brought down significantly through the use of the Sykes pump. Levels are typically in the region of 4–4.5% after one day.
Reliability is crucial
The 6in GP150 electric surface pump from Sykes has now passed a two-year milestone of 24h a day, seven days a week operation at Eaton Hall Quarry without a single defect or downtime incident.
Tarmac already hire pumps from Sykes at a number of other quarries, and the company’s 14-day servicing intervals within the hire rate and 4h response commitment from its Stoke-on-Trent depot, helped secure the Eaton Hall dewatering contract.
‘The reliability of the dewatering pump on hire from Sykes is so critical to our operational efficiency and the production of a high-quality product,’ said Mr Gibson.
The on-site Tarmac team are responsible for daily checks on the pump, such as keeping oil levels topped up, and can call out the Sykes Pumps team at any time if they have any maintenance concerns. ‘With Sykes, we can not only be confident of a correctly specified and reliable machine from day one, we also have the peace of mind that comes with great service, technical backup and regular maintenance visits. The backup from Sykes is absolutely brilliant – just one phone call and someone will be here within the hour.’
To buy or not to buy?
The electric pump used for stockpile dewatering at Eaton Hall Quarry is part of a hire package put together for Tarmac by Sykes Pumps. Tarmac can rely on the latest pump technology, without the need to purchase their own pump equipment, backed up by regular service visits and a fast response should an emergency call out be necessary.
The hire option has also been adopted at several other Tarmac sites where stockpile dewatering is required. However, outright pump purchase is also an option and this can be backed up with a bespoke service agreement, as required.
The need to hire pumps can be driven by many factors but the key element of the decision-making process often involves balancing the convenience of hire against the capital cost of purchase and ownership. Businesses may see ongoing hires as an unnecessary cost, but in most circumstances hire will work out cheaper than the cost of ownership.
A pump is not a throwaway commodity and the initial purchase price reflects that. The level of expertise required to service and maintain pumps is not always readily available within an organization, and even if it is, that expertise is often gainfully employed in some other full-time role. When the capital costs are added to wages, service vehicles, specialist tools, as well as storage and distribution costs, it quickly becomes more cost-effective to hire pumps from a supplier who already has that expertise and is based in multiple convenient locations.
GP is front of the grid
Tarmac have opted for the 6in GP150 electric-motor-driven model from Sykes’ general-purpose (GP) range. For sustained pumping performance and maximum reliability, Sykes say their general-purpose pumps still lead the way, as they have done since 1857. Handling everything from clean water to sludge and slurry, they are specifically designed and manufactured for arduous applications.
The pumps are easy to maintain and provide hours of unattended operation due to the use of tried and tested components, selected to ensure maximum reliability. Manufactured in the UK, the GP pumps comply with all of the most stringent quality standards, both British and European.
Used wherever there is a need for positive self-priming pumps, the GP range incorporates Sykes’ special vacuum system that allows the pump to prime and re-prime fully automatically from dry, and to operate with the suction intake intermittently exposed to atmosphere.
From the 2in unit, which comes with handles for ease of movement on site, up to the 8in model, the same high-quality standards are applied. Each unit has an integral fuel tank that allows up to 24h of pumping before refuelling, ensuring minimal disruption to the job in hand and that labour is not interrupted by the need to fuel the pumps on a regular basis. Fuel consumption can be as little as 0.5 litres/h, and all GP pumps are available with alternative engines, motors and chassis configurations.
These extremely versatile pumps offer flow rates of up to 161 litres/s and a maximum head of 43m, with the ability to handle solids up to 75mm in size.
For more information visit: www.sykes-pumps.com
- Subscribe to Quarry Management, the monthly journal for the mineral products industry, to read articles before they appear on Agg-Net.com