Slurry Pump Development
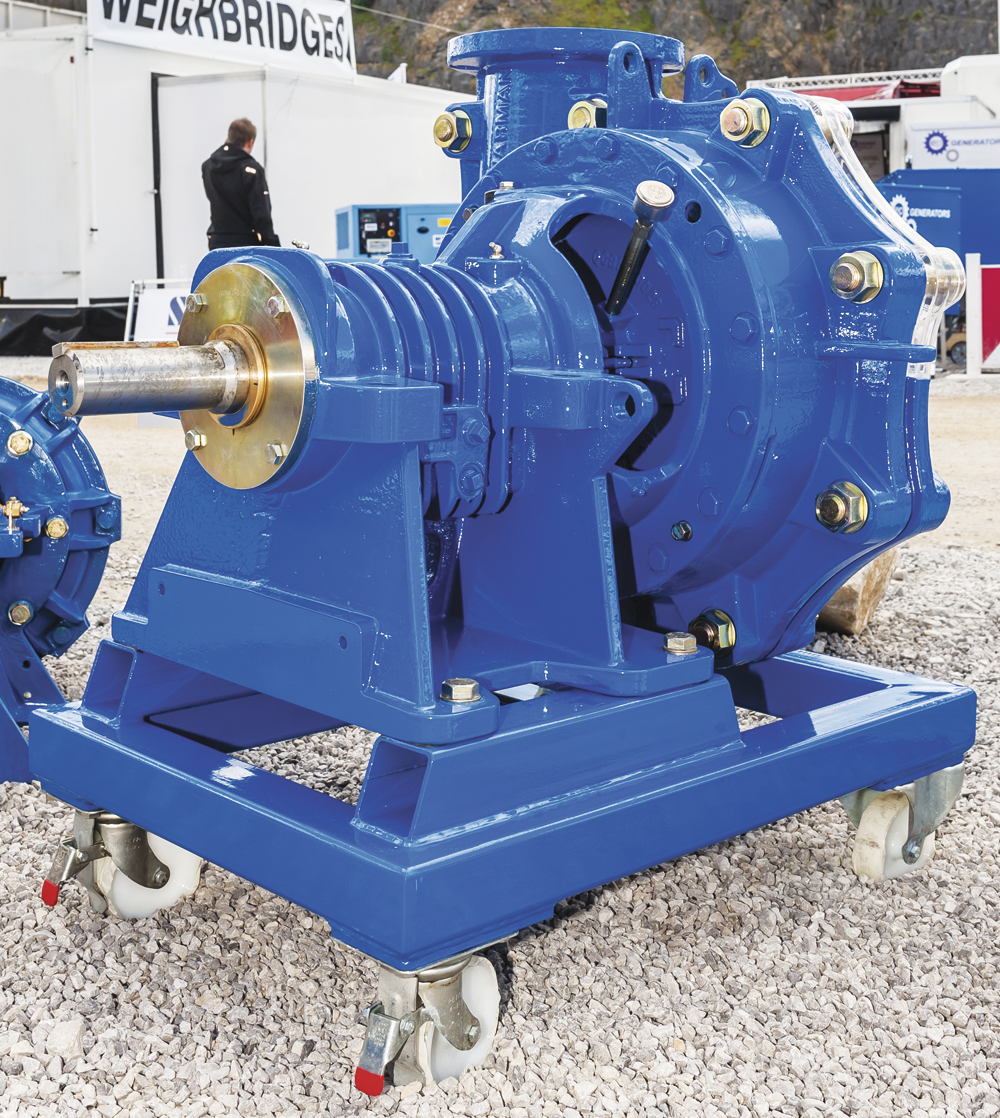
Strengthening the backbone of the quarrying process
By Harvinder Bhabra, senior product manager, Weir Minerals Europe Ltd
As the complexity of processing at quarries increases, producers are looking closely at the performance of their pumps. This article examines how the need for increased efficiency, longer wear life and easier maintenance led to the development of the newest member of the Warman family of pumps.
Quarrying, for the most part, is not a high-margin business. The products generated, unlike other resources extracted from the ground – including oil and gas derivatives, precious stones and metals, and rare-earth elements – do not command high commodity prices, despite the difficulties involved in extracting, processing and transporting them to customers.
For this reason, the impact of the efficiency of a quarrying process is felt more acutely on the bottom line than in many other industrial sectors.
In recent years, the financial challenges have been compounded by the increasing emphasis on excellent environmental performance, driven by both increasingly strict regulation and for commercial reasons – demand for materials with strong environmental credentials has burgeoned in the last 10 years.
The result has been an increase in the complexity of the typical quarrying process, with extra stages introduced to ensure that the maximum amount of water is kept within the system and that the finer particles in the raw mixture can be classified, cleaned and sold.
The need for complex separation and screening processes will grow more relevant in the years ahead as producers look to extract from increasingly mixed raw sources as environmental regulations develop and accessible pure sources become depleted.
One important consequence of this increase in process complexity is the need it has created for more reliable pumping equipment at the typical quarry.
As a result, the focus of producers on the longevity and efficiency of the pumps they are using has intensified. Manufacturers are responding to this by innovating and applying advanced engineering to develop pumps that are more efficient, run for longer between repairs and are quicker and easier to service.
It is these challenges that have led Weir Minerals to develop the Warman WBH, an update to the long-standing Warman AH pump range – a common feature at quarries around the world and considered the industry standard by many operators.
Back to basics
The original brief for the research and development project was launched when it became clear that to improve the Warman AH any further, fundamental changes would be required. As a result, the decision was made to start from scratch and design a new pump that would outperform the Warman AH in every way – wear life, efficiency, safety, ease of maintenance etc.
This new development, the Warman WBH pump, was developed using state-of-the-art techniques, drawing on every available design verification method. Computational fluid dynamics (CFD) software was used heavily during the process to develop wear prediction and performance analysis models that assisted in refining the impeller and volute design.
This identifies the high-turbulence areas (for a given shape), which normally cause excessive wear. Working with three-dimensional CAD models, Weir Minerals were able to design in features that were needed to improve both wear life and overall performance.
The accuracy of the models was verified by comparing the results with wear patterns on used AH wear parts and actual energy consumption data.
The new design takes into account the full range of slurry mixtures the Warman WBH could be required to handle.
The final product is a pump range that has a number of unique features, including:
- A four-vane impeller design that allows for much improved slurry guidance and smoother flow to give improved life, higher efficiency and low net positive suction head (NPSH) characteristics, reducing the likelihood of bubbles of gas forming in high-temperature flows.
- A streamlined volute liner with a profiled cutwater.
- A single-point control that allows the throatbush to be adjusted both axially and radially.
Staying efficient
When a pump is newly installed and correctly set up it will run at close to its optimum performance. However, as wear takes its toll – as is inevitable with abrasive slurries passing through at high speeds – efficiency will begin to fall and energy consumption for a given flow rate will increase.
Years of experience with the Warman AH has revealed that one major reason for this decrease in efficiency is due to wear between the impeller and throatbush (suction liner), causing the front clearance to increase. This leads to recirculation of slurry within the pump, which, in turn, leads to loss of efficiency and performance.
One of the key innovations of the Warman WBH is the adjustable throatbrush, which allows operators to adjust the clearance easily and quickly. This allows the clearance to be closed and rotation of the throatbush at the same time, thereby allowing equal wear. Adjustment of the throatbush is one of the most common maintenance operations carried out on pumps, so the ability to perform this fine-tuning without too much interruption to the process is a significant advantage.
A number of other maintenance features have also been designed into the range. For example, a quick-release mechanism has been developed for the casing liners in both metal- and rubber-lined pumps, to speed up the process of changing worn liners. Also, a rigid, one-piece bearing frame and fixed bearing position ensures optimum alignment, increasing efficiency and bearing wear life.
Field trials
Several field trials have been undertaken in a variety of industries and applications to thoroughly test the WBH pump performance. Every test has shown significant wear life, energy consumption and maintenance advantages over existing pump designs.
A Warman WBH has been tested at coal mining operations in Australia, including Coal & Allied’s Mt. Thorley operation in New South Wales. The company previously used Warman AH units to move slurry through its preparation plant, but the new pump is said to have exceeded all expectations.
Elsewhere, AH pumps were achieving an average time between parts replacement of 2,200h on a very aggressive china clay application – a not unreasonable figure on such a slurry pumping duty – but the Warman WBH delivered 6,700h between replacements, more than three times the duration.
Another WBH pump on a cyclone feed application in a sand and gravel application outlasted an existing slurry pump by a significant margin, and was still consuming 15% less energy against the ‘as new’ pump.
The Warman WBH was born of a need for operators to get the very best performance out of their pumps. In the quarrying industry, where the efficiency of a process can have a significant impact on the operation’s profit margin, the case for investment in the latest technology is clear.