Selecting the Correct Pumps for Coal Washing Plants
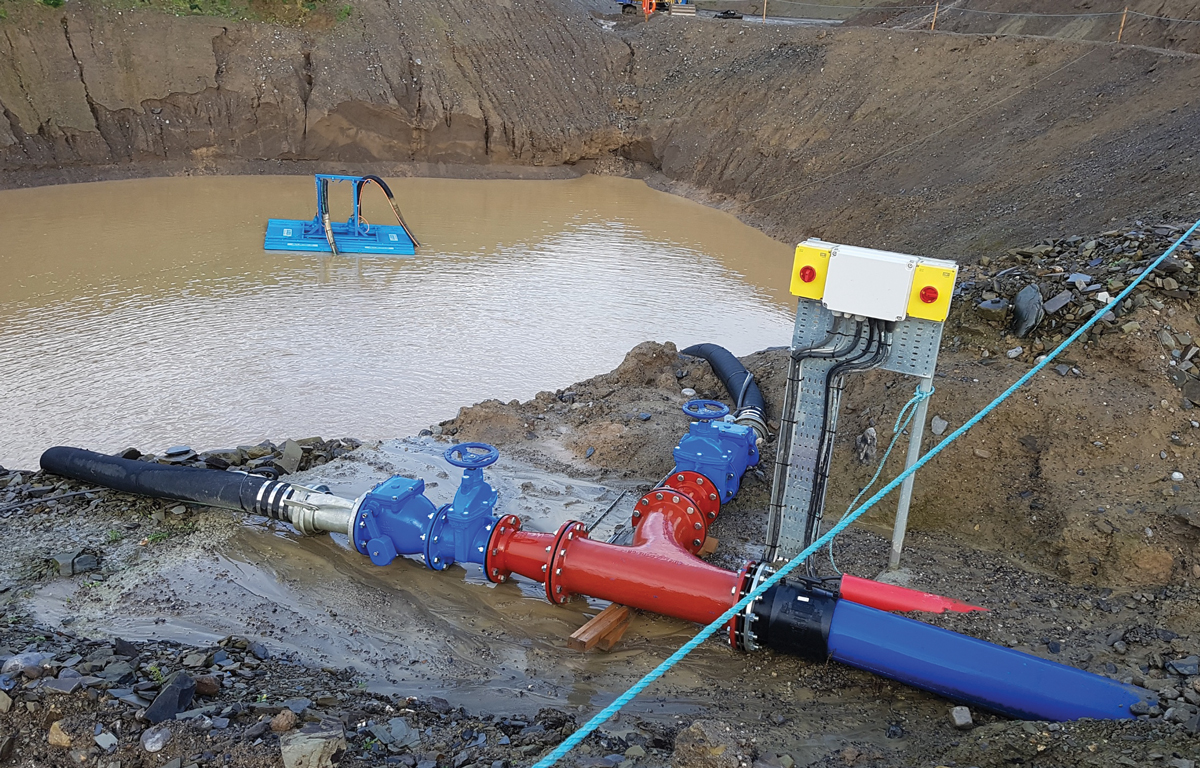
First published in the August 2020 issue of Quarry Management as Paying Attention to Pumps
Bill Noakes, chief marketing officer with Atlantic Pumps, examines the key considerations when selecting the correct pumps for coal washing plants
Although recent growth in global coal consumption has faded, coal power still contributes more than a quarter of the world’s energy. The developing world, in particular, is likely to rely on this power source for a good number of years to come. It is clear that the industry, which is faced with both lower-cost alternative providers and environmental concerns, needs to run as cost-effectively and efficiently as possible.
In the process of mining coal, up to 50% of the extracted material can be waste. This stony material must be removed from the coal before it can be processed. Coal processing plants wash the coal at the same time as crushing and sizing it. A significant factor in the running of a coal processing plant is the sourcing of water to feed the wash plant and the subsequent removal of the abrasive waste water. Paying attention to the pumping requirements of this water transfer is, therefore, vital.
Water feed for the plant
Depending on how and where the plant is situated, sourcing water and supplying it at the required pressure can be a challenge. Wash plants situated in a quarry or mine environment often extract water from an on-site lagoon, which makes sense as waste water can be recycled by allowing it to settle in such lagoons. Alternatively, water can be extracted from a borehole in the vicinity, whilst the most expensive option is to take it from the mains supply.
Pumping water from a lagoon can be achieved using an industrial-grade water pump. Depending on the location of the lagoon, electric power is often not available, so a diesel pumpset may be used. If electric power or a generator is available, an electric submersible pump can be suspended
from a pontoon. The higher the water has to be pumped, and the further away the lagoon is from the wash plant, the more powerful the pump that will be required.
Extracting water from a borehole is achieved using a high-pressure multi-stage pump. These can run at high efficiency due to the water generally being clean and free of residue.
The wash plant
Typically, run-of-mine (ROM) coal is fed into the coal processing plant on conveyors; this supply is kept at a constant rate by maintaining on-site stockpiles. This raw material is crushed and screened to make it more manageable, and is grouped by particle size. The next stage is coal washing. This is the most important stage as this is how the coal is produced to the customer’s quality requirements, and also to meet environmental standards when burnt.
Different grades of coal and the reject material have different densities, which means gravity separation methods can be used to extract coal with the required properties. These methods include jigs, dense-medium baths and cyclones, as well as froth flotation for fine coal washing.
All these methods involve adding water from the plant feed to the ROM coal. The water is stored in a sump under the plant, before being pumped around the plant at a high pressure. Once the coal is added it becomes a slurry, which is a completely different pumping challenge to clean or recycled water.
Pumping slurry
It is important to use a specialist slurry pump because slurry is highly abrasive and quickly wears out ordinary pumps. Slurry pumps have replaceable liners and all wear parts are made from abrasion-resistant materials, usually rubber or high chrome, although elastomers, stainless steel and ceramic can be used. Slurry pumps have wider tolerances to allow solids to pass through, which makes them less efficient but much longer lasting than water pumps. The casing and bearings are also more rugged, so these pumps are larger and heavier, and require more horsepower to operate.
Centrifugal horizontal slurry pumps are the most common kind, whilst vertical slurry pumps, where the shaft sits in the water, are often used for pumping water out of a sump. For applications with a lower flow rate, lobe pumps or peristaltic pumps can be used to transport slurry. Care must be taken when selecting pumps with a higher efficiency; sometimes the effect of abrasion is to quickly erode this efficiency, resulting in higher lifetime costs than a pump with lower apparent efficiency.
Dewatering the coal
A variety of methods are used to reduce the water content of the washed coal. These include centrifuges, screens, cyclones and filters. The resulting waste water is still a muddy, abrasive slurry, laden with coal fines, briquettes and dirt. This waste water requires a slurry pump to move it.
Often, the next step is to use a method such as a thickener tank to extract the water from this waste. The water extracted from the thickener tank can be recycled, either back into the plant or pumped using a standard water pump to an on-site lagoon to be reused when required. The residue sludge, known as the thickener underflow, can be pumped to a tailings dam for disposal or further dewatered. Thickener underflow requires a low-flow pump capable of handling liquid with a high solids percentage, such as a peristaltic pump.
Other water requirements
There is also a requirement for clean water to power the truck wash-down, and to run any dust-suppression systems, depending on the environmental standards where the plant is situated. This clean water can be taken from a lagoon or borehole, or by reuse of the recycled water from the plant, treated as necessary.
Choosing the correct pump
The harsh environment found at a coal processing plant makes pump selection particularly important. Often, pump users focus on the purchase price and initial efficiency. However, it is important to consider lifetime costs, the costs of energy to run the pumps and the costs of servicing and replacement parts.
Basic factors to consider when selecting a pump include:
- What are the required head and flow rates?
- How far does the water have to be pumped?
- What sort of dirty water is actually being pumped – is it cloudy or does it contain heavy solids?
Consideration should also be given to friction loss as a result of the pipework configuration.
Energy costs
Energy costs are a major issue for industry today, both in terms of the need to improve the efficiency and profitability of business enterprises, and in reducing the impact of business on the environment by producing less carbon dioxide. In seeking to make their business more competitive, how often do pump users consider the major cost and energy savings they can achieve by having correctly specified pumps for their application?
Often, when thinking of the costs of pumps, users think a lot about the purchase price, hire costs, or the ongoing maintenance costs, spares and servicing. Yet, it is a little-known fact that all this makes up only 15% of the lifetime costs of a pump. The other 85% of the typical lifecycle cost of a pump is the cost of the energy consumed to keep the pump running.
One of the best ways to reduce energy costs is to ensure that pumps are correctly sized for the application. It is estimated that up to 30% of installed rotating pumps are bigger than they need to be. Lower energy costs are a direct result of matching the correct pump to particular system requirements.
It is important to take into account the required pressure and flow rate, plus other factors such as the temperature or viscosity of the fluid, and the length and configuration of the pipework. The composition of the liquid is also a major factor to consider; for example, when pumping slurry, a more efficient pump can be used if the particle sizes are smaller. An additional benefit of selecting the correct pump for a specific application is that it is highly likely to last longer and cost less to maintain.
When replacing pumps where the original system was not optimized for energy usage, savings of 50% or more can often be achieved.
Stock-holding considerations
As specialist items of equipment, pumps are notorious for long lead times for parts or replacements. This can be very expensive if it results in extended downtime, and consequently leads to end-users stockpiling parts and even spare pumps. This is clearly a misuse of resources unless the plant is in a very remote location. Consideration should be given to purchasing pumps from suppliers who are quick to respond to enquiries and offer rapid delivery as standard.
Future developments
The design of pumps has remained remarkably stable through the industrial age. However, with the advent of the Internet of Things and the next ‘Industrial Revolution’ it is bringing, the way pumps are operated may well change radically.
Remote monitoring of pumps is rapidly becoming normal across many industries. This allows not only for the pump to be operated from anywhere in the world, but also the pump temperature, vibration and energy consumption can be monitored in real time. This, in turn, means pump failure can be anticipated and prevented, even if nobody is on site, and replacement parts can be sent out to arrive just as they are required.
This leads to a whole range of benefits to plant operators, from reduced downtime and maintenance costs, quicker analysis of performance of new installations, through to energy optimization and lower emissions.
- Subscribe to Quarry Management, the monthly journal for the mineral products industry, to read articles before they appear on Agg-Net.com