Principles and Procedures of Sieving Analysis
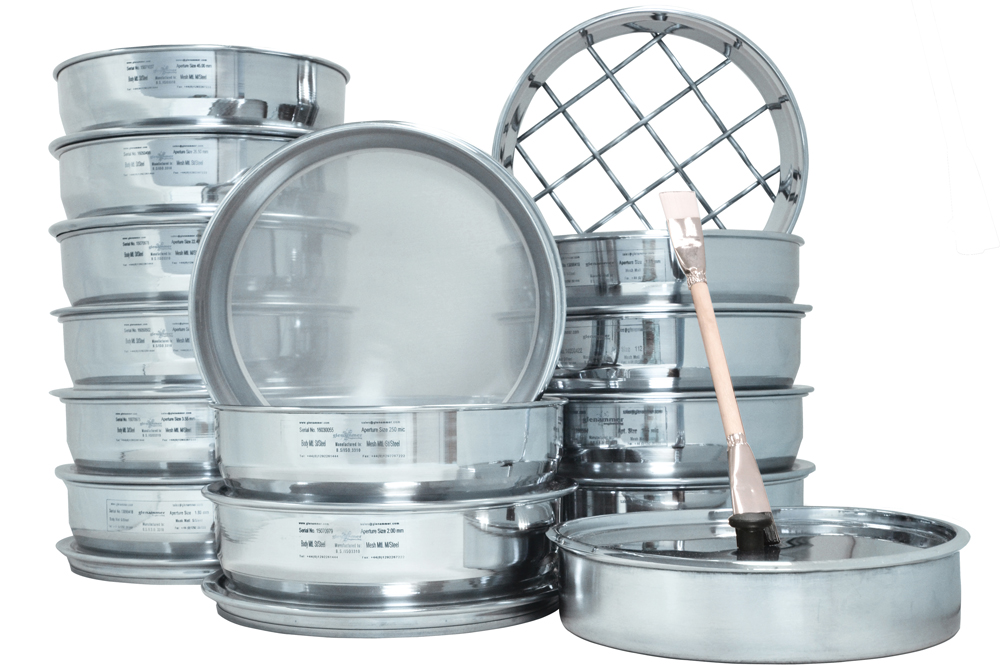
First published in the December 2017 issue of Quarry Management as Sieving Analysis
Glenammer Engineering, manufacturers of engineered laboratory test sieves, outline the principles and procedures
Sieving analysis is the first choice in particle size analysis for numerous reasons. Among them, simplicity, efficiency and low cost have all made sieving analysis the most widely used quality-control procedure in any powder process control industry. In order to conduct accurate sieving analysis, however, users need to understand the test sieve standards and tolerances, the correct sieving process, and the care and cleaning procedures needed to keep sieves in good condition.
Understanding test sieve standards and tolerances
Mesh number represents number of wires per inch (25.4mm)
Woven wire sieves are sold either by mesh number or by the wire spacing. Mesh number is measured as shown in figure 1. The ASTM American standards use mesh numbers, whereas ISO/BS International and British standards tend to use wire spacing.
8in is not 200mm
In ASTM standards, sieve diameter sizes are measured in inches, whereas in ISO/BS standards millimetres are used. There is a slight difference between 8in and 200mm, or 12in and 300mm diameter. In reality, 8in is 203mm and 12in is 305mm. Thus, 8in diameter test sieves and 200mm diameter test sieves will not nest with each other, likewise nor will 12in and 300mm diameter test sieves.
Not all apertures sizes are the same
There are three main aperture parameters in the standards: maximum aperture size, average aperture size and maximum standard deviation. Considering the ISO/BS and ASTM standards all allow aperture size variation, particles larger than nominal size might pass through. In most situations, the cut point will be very close to the upper standard deviation but will not be the exact principle size. Thus, if particles have to be cut to a certain nominal size, users are recommended to choose a sieve that is slightly smaller than the nominal size to get a more accurate result.
Understanding the standards helps users to choose the test sieve with the most suitable diameter size and aperture size. Before conducting an analysis, users might also want to make themselves aware of the following tips to make their analysis more efficient and accurate.
Tips for sieving analysis
Monitor the laboratory conditions
Before conducting the experiment, one factor that needs to be considered is the reaction of the material to ambient conditions. It is worth noting that extremely dry conditions can cause fine powders to adhere both to sieve components and to each other with strong electrostatic charges.
Control of sample size
For a lot of experiments there is a tendency to use an excessively large sample to get more accurate test results. However, for sieving analysis, the accuracy of the result will be reduced if the sample is too large, because this will not permit each of the particles an opportunity to present themselves on the test sieve surface. Generally, a 25–100g sample is recommended. A procedure exists to help establish the appropriate sample size, using a sample splitter to reduce the sample to different weights (25g, 50g, 100g, 200g), and testing samples in the various weight ranges. If the test with a 50g sample shows approximately the same percentage passing the fine sieve as a 25g sample, whereas a 100g sample shows a much lower percentage passing, this would indicate that the 50g sample is the appropriate sample size.
Intermediate receivers make testing more efficient
By using intermediate receivers, users can conduct two or more different experiments while operating the sieve shaker only once. As shown in figure 2, material A and material B can be tested at the same time; material A can be collected in an intermediate receiver and material B in the receiver at the bottom.
Consider using ‘relief sieves’
To avoid overloading any sieves and causing damage, care should be taken in selecting the proper sieve aperture sizes. Large concentrations of material passing through the sieve will result in a large proportion of material being retained on the test sieve. ‘Relief sieves’ are larger-aperture sieves placed above the one the sample is to be retained in. They are used to help remove the burden and avoid damage to the fine mesh, otherwise particles slightly larger may become wedged in or forced through the sieve opening by the mass of material resting above.
Sieving procedure
Apparatus:
- Stack of test sieves
- Balance (with accuracy to 0.01g)
- Rubber pestle and mortar (for crushing the test material if lumped or conglomerated)
- Sieve shaker
- Oven.
The balance used should be sensitive to 0.1% of total weight of sample taken.
Procedure:
Step 1: Take a representative oven-dried sample that weighs approximately 500g.
Step 2: If particles are lumped or conglomerated, crush the lumps but not the particles using the pestle and mortar.
Step 3: Determine the mass of sample accurately – Weight (g).
Step 4: Prepare a stack of test sieves. The sieves are stacked in order, with the largest aperture size at the top, and the smallest at the bottom. A receiver is placed under all of the sieves to collect samples.
Step 5: Weigh all the sieves and the pan separately.
Step 6: Pour the samples from step 3 into top of the stack of sieves and put the lid on, place the stack in the sieve shaker and fix the clamps, adjust the timer to between 10 and 15 minutes, and switch on the shaker.
Step 7: Stop the sieve shaker and measure the mass of each sieve and retained soil/material.
Once the whole procedure has been completed users can analyse the results. The starting sample weight should be recorded and compared with the finished total sample weight retained on the sieves after the experiment. If the weight of the finished sample deviates by more than 2% from the initial weight, the analysis and sample should be discarded. Technically, sample losses can result in error and inaccuracy of the analysis.
Test sieve care and cleaning
Like other laboratory test equipment, test sieves require regular care to maintain the performance standard.
Clean between sieving
Between uses, it is recommended that a nylon-bristle paintbrush be used to clean the mesh with a gentle circular motion from the underside. However, excessive brushing can damage the mesh, so brushing should be avoided on sieve mesh finer than 150 microns (No.100).
Maintenance after use
When particles are lodged in the fine mesh, using brushes or sharp objects to remove them can cause damage. Ultrasonic cleaning is the best method to remove particles trapped in the mesh. The sieves should be immersed in the ultrasonic cleaning bath and then dried thoroughly before reuse. Ultrasonic cleaning should be conducted on a regular basis after testing.
Some experiments might require wet-wash sieving. This is a method of analysis where liquid drains through a stack of sieves, after which the residue needs to be dried, either over a hot plate or in an oven. If the oven temperature is too high, the sieve cloth might become loose and the solder joint could be damaged, therefore maintaining the temperature below 149°C (300 °F) is recommended.
Time to replace the sieve?
With proper cleaning and care, test sieves should provide many years of consistent service. However, users should replace the sieves if they show any sign of the mesh becoming loose or damaged, or if it fails to pass calibration.
Protecting sieves from damage
It is important to use test sieves with the correct aperture size. When it is necessary to utilize sieve shakers to conduct experiments, the use of larger aperture size sieves stacked above the finer ones, to reduce damage to the finer mesh, is recommended.
Glenammer test sieves are designed to be easy to clean and offer a simple maintenance solution. The company reinforces all test sieves that are under 90 microns (No.170) by attaching a larger aperture as a stronger backing mesh to support the fine mesh and protect it from damage. Also, the edge between the mesh surface and the frame is painted to prevent particles from getting stuck.
Moreover, each Glenammer test sieve comes with a laser-marked label on a highly polished frame. Since 2014, the company has used laser technology to replace the traditional riveted/protruding labels. Laser labels are longer lasting and more resistant to fading through regular usage. It is also a labelling method that minimizes the use of materials and subsequent waste to the environment. A brand-new 3D laser-marking machine came into production in August 2017, allowing Glenammer to make much bigger and clearer laser labels three times faster than before. Gleanammer say the use of laser marking makes their test sieves unique and easy to clean, with no risk of residual material or contamination. For more information visit: www.glenammer.com
- Subscribe to Quarry Management, the monthly journal for the mineral products industry, to read articles before they appear on Agg-Net.com