New Products from JCB
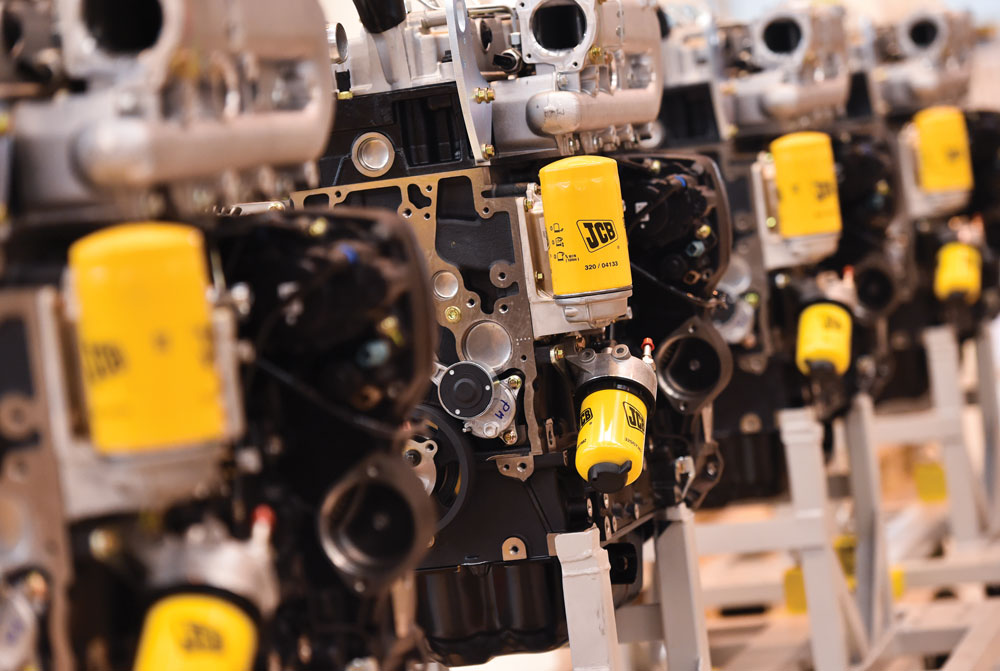
First published in the March 2017 issue of Quarry Management as Powering Ahead
JCB unveil their latest product offerings and corporate developments
Last month [February] JCB unveiled a host of new products and corporate developments to a gathering of more than 100 UK and overseas journalists at the company’s annual international press launch event. Proceedings kicked off with news that production of a brand new, highly fuel-efficient JCB Dieselmax engine is about to get under way, marking the culmination of a £31 million investment programme. Joining the existing 4.4-, 4.8- and 7.2-litre models, the new 3.0-litre JCB430 Dieselmax has been designed specifically for mid-range construction and industrial equipment operating cycles.
Next came news that JCB have entered the powered access market for the first time with the launch of a totally new product range, as the company sets out to grab a significant slice of a global market that generates annual revenue of US$8 billion. JCB have been developing a line-up of powered access machines in secret for the past two years, and last month the wraps came off an initial nine all-new electric scissor-lift models. By the end of 2017, the newly launched JCB Access business will be offering a total of 27 new platforms, including scissors, articulated booms and telescopic boom machines.
On the following pages, we pick out a few of the highlights from the developments and product offerings revealed last month that are likely to be of key interest and relevance to operators working in the quarrying, aggregates, recycling and related sectors.
Engine plant investment
Continuing the engine theme, JCB Power Systems revealed details of a £10 million investment in their UK engine plant as they gear up to begin full production of cylinder heads and blocks for the first time. The Derbyshire-based factory has installed new CNC machining centres and associated automated processes at the site, which the company says will give outstanding levels of finished accuracy in house, as well as boosting production capacity.
JCB Power Systems, based in Foston, began production of their own engine range in 2004 and to date more than 400,000 JCB Dieselmax and JCB EcoMax engines have been produced. The engines now provide power for more than 70% of JCB equipment sold around the world.
The latest £10 million investment will allow the company to produce cylinder heads, engine blocks and bedplates – the major engine components – in house for the first time, boosting efficiency and ensuring that the company’s demanding quality targets are met. The new machining centres will be able to produce a set of engine components in just five minutes, boosting the Foston factory’s capacity to up to 45,000 engine sets per year.
Alan Tolley, JCB group director for engines, said: ‘The multi-million-pound investment in machining in house gives us direct control over specification, quality and cost of the major components. This is a major step forward for JCB Power Systems and an important piece of the jigsaw that keeps us producing class-leading engines at competitive cost.’
New engines for heavy JCB excavators
As well as their in-house engine developments, JCB are to boost the fuel efficiency, productivity and performance of their heavier crawler excavators with the installation of MTU diesel engines. The six-cylinder, Tier 4 Final MTU 6R1000 engine – already proven in JCB’s largest wheel loader, the 457 – will now be used in the JS300, JS330 and JS370 machines.
The 7.7-litre MTU diesel engine is a highly efficient turbocharged and intercooled powerplant that will deliver 180kW (241hp) in the JS300 and 210kW (281hp) in the JS330 and JS370 models. The machines will incorporate selective catalytic reduction (SCR) within the exhaust system, with dosing of a urea-based diesel exhaust fluid (DEF) to reduce NOx emissions by almost 90%. This system allows the MTU engine to meet Tier 4 Final without having to use a diesel particulate filter (DPF), thereby reducing cost and service complexity for the customer. Introduction of the MTU engine will mean fuel savings for customers of up to 10% on the JS370 and 5% on the JS300 and JS330.
The excavators are equipped with a 47-litre DEF tank and the fluid is used at a rate of around 3% compared with fuel consumption. This means that operators will only need to top up the DEF tank, which is located within the top toolbox, with every third tank of diesel. A warning system incorporated within the JS excavators’ main monitor will provide operators with graduated warnings of reducing DEF levels to prevent automatic down rating if the DEF tank is not replenished.
Moreover, by upgrading to the MTU engine, JCB say they have been able to reduce the number of fuel filters required from three to two, thus reducing operating costs for customers. A fuel shut-off tap has also been fitted to make service work easier.
The air cleaner has also been upgraded, with the JS machines moving to a new PowerCore unit that uses an ultra-web nano-fibre technology. This delivers increased dust-holding capability and is said to be three times more efficient than a pleated filter, yet offers increased airflow. Moreover, it is stronger and more durable, and, with the option of a scavenger pre-cleaner, there is no requirement for a vacuator valve.
Access to the new MTU engine has also been improved with the adoption of a single-piece canopy. The steps have been redesigned with an extended lower step as part of a two-tier toolbox. The bottom tier provides access to the standard refuelling pump, while the upper section contains the DEF/AdBlue filler. Tread plates have been installed on the steps and the upper structure, and the machines now benefit from a standard riser handrail, side handrail and kickplates for added safety, although optional full-surround ‘boxing ring’ handrails are available if preferred.
New hydraulic hitches
Meanwhile, JCB Attachments are introducing two improved hydraulic hitches for use with JCB’s mid-weight JS excavators (both crawler and wheeled). The hitches, which meet the ISO 13031 standard and have been designed to suit machines in the 13–14-tonne sector and the 20–22-tonne market respectively, have a positive locking system in which the front safety lock is forced into its default position by a spring, thereby retaining and locking the attachment pin. The hitches use the rear lock as a secondary safety feature, backed up by two powerful springs, thus retaining the attachment’s rear pin in the event of a cylinder failure.
Variable pin centre designs make the hitches suitable for use with a wide range of attachments. Moreover, they have an open-frame design to prevent material build-up and there are no grease points, thus reducing regular maintenance and boosting productivity. Both the front and rear pin hooks are painted to make them visible to the operator in the cab, and there is also a CE tested and certified heavy-duty lifting eye on the end of the hitch. JCB Attachments have also improved the hose routing to the hitch and there is now a guide on the hitch’s tipping link to prevent snagging and damage to hoses.
To operate the hitch, the machine driver must press and hold the hitch switch in the cab for one second until a buzzer sounds and the hitch light on the boom is activated. An unlocked image also appears on the machine’s main console. The buzzer will continue to sound and the lights flash to indicate that the hitch is unlocked. Once the bucket or attachment has been changed, the operator simply has to crowd the bucket service to position the attachment in a safe position and fully close the hitch jaws around the attachment pins. A prompt on the machine display ensures that the operator has checked the attachment security, with a press of the dial required to confirm this.
The smaller of the two new hitches is designed for use with the JS130, JS131, JS140, JS145 and the JS145W excavators, whilst the larger version is for use with the JS200, JS210 and JS220 models. Both hitches are available as line-fit items or can be ordered through JCB dealers as aftermarket offerings. ™
New Proximity Braking System
For operators of JCB wheel loaders, the company is launching a brand new safety system to help reduce the risk of on-site collisions between man and machine. The JCB Proximity Braking System (PBS) – which has been developed in collaboration with FCC Environment (UK) – is being launched initially as an option on JCB’s flagship wheel loader, the 19-tonne JCB 457, but with plans to roll out the feature across the rest of JCB’s wheel loader range.
The PBS system uses triple antennas mounted on the wheel loader to generate a detection zone or ‘safety bubble’ around the machine and automatically sounds an alarm in the cab, puts the vehicle into neutral and applies the braking system to bring the loader to a halt if a person enters the pre-set exclusion zone. In tandem with this, operatives on site are equipped with a vibrating transponder – usually attached to a safety helmet – that will vibrate to warn them that they have entered a danger zone. Potential collisions are recorded on the wheel loader’s MCU, with date and time information, so that further investigation can be carried out as to why the individual entered the machine’s danger zone. This can be used to highlight further safety improvements that can be carried out on site.
The JCB Proximity Braking System can be fitted to multiple machines on a single site. It is particularly suited to heavily trafficked working areas, such as waste and recycling sites. Installation of the system requires a site visit and assessment in order to understand the site operation, check on walkways, traffic routes and other site-specific variables that can affect the operation of the system. JCB also stress that the Proximity Braking System should be seen as an additional aid to site safety and not a replacement for standard site safety practices.
New industrial version of the JCB TM320
Finally in this JCB launch event round-up, comes news of the unveiling of a new TM320 telescopic wheel loader designed specifically for the construction and industrial sectors. Combining the central driving position and all-round visibility of a wheel loader with the reach and lifting capabilities of a telescopic handler, the new machine will sit alongside the existing TM320 Wastemaster.
With a maximum lift capacity of 3,200kg, which is available from ground level to a full lift height of 5.2m, and a maximum lift capacity of 1,750kg at full forward reach (2.95m ahead of the front wheels), JCB say the TM320 is highly versatile and particularly suitable for re-handling applications in concrete batching plants or smaller quarry operations.
The new TM320 is powered by a 4.4-litre version of the award-winning JCB EcoMax engine, which develops 93kW (125hp) and meets EU Stage IV/US Tier 4 Final emissions compliance using JCB’s selective catalytic reduction (SCR) system. JCB’s chief innovation and growth officer, Tim Burnhope, said: ‘This is a proven solution that we introduced on our Loadall telescopic handlers for Europe earlier this year. It’s a very compact installation that makes efficient use of AdBlue, without detracting from the engine’s excellent power, torque and fuel-consumption characteristics.’
Driving through a four-speed JCB Powershift transmission, the engine offers a maximum speed of 40km/h. The transmission can be operated in automatic mode or manually, using a traditional left-hand lever, by operating the shift and forward–reverse selector switches mounted on the Servo joystick. For maximum performance and efficiency, the machine is equipped with a load-sensing hydraulic system, with an output of 140 litres/min.
A hydraulic reversible cooling fan that provides a choice of reversing intervals to suit different situations, as well as manual activation to purge the cooling pack of dust and debris when necessary, is available as an option. The TM320 also gets cylinder end damping as standard, to refine the operating experience when the telescopic section of the boom is fully extended and when the boom is retracted and lowered, whilst JCB’s Auto Smooth Ride System boom suspension is available as an option. In addition, resilient bronze graphite bushes extend the chassis pivot and boom greasing interval to 500h.
A full-colour instrument display is one of several new features in the spacious operator’s cab. This provides information and warnings in a clear ‘at a glance’ format, and allows daily checks on engine oil, coolant and washer fluid levels to be completed from the driver’s seat during engine start-up, saving time and ensuring that these essential checks are carried out as a matter of routine. An optional rear-view camera with colour display can be supplied, and an immobilizer key option is also available to complement the theft deterrence provided by JCB LiveLink.
- Subscribe to Quarry Management, the monthly journal for the mineral products industry, to read articles before they appear on Agg-Net.com