New Energy Savings Plan from ABB
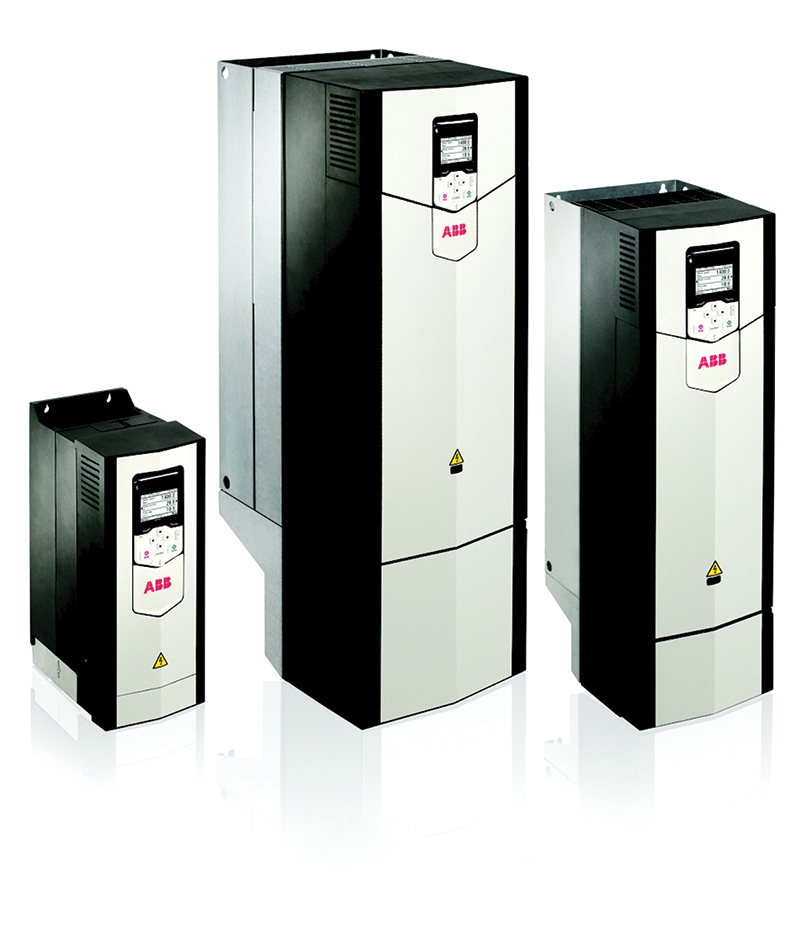
First published in the October 2015 issue of Quarry Management as Enhanced Performance
New savings plan from ABB increases production output and cuts energy bills
ABB have launched an all-new Energy Efficiency and Productivity Improvement Plan, aimed at providing step-by-step support for enhancing the performance of motor-driven applications using variable-speed drives (VSDs) and high-efficiency electric motors. The plan takes into account the often-overlooked productivity benefits that variable-speed drives can bring.
‘When drives were initially introduced some 40 years ago, the focus was on regulating motor speeds to improve production output,’ explained Dave Hawley, general manager for ABB’s UK motors and generators business. ‘It was only in later years that the focus on energy efficiency began to dominate. It is time to redress the balance and once again highlight the important features that variable-speed drives offer to improve productivity.’
Included within the 10-stage plan is an Energy and Productivity Appraisal that is undertaken by ABB and their network of authorized value providers.
The appraisal starts by outlining the scope of supply, focusing on processes and applications where significant energy savings can be made. These will most often be variable-torque applications that obey the cube law, running continuously and where flow is controlled by a mechanical means, such as valves or dampers. The productivity part of the appraisal will look at both variable- and constant-torque loads, their control methods and where improvements such as reduced maintenance, increased availability or product quality can be made.
The next step is monitoring and data collection, which involves identifying applications that may be running inefficiently. An ABB engineer will look not only at fixed-speed motors, but also at any drives currently being used, to see if the application is running at maximum efficiency and productivity levels. The selected applications may be monitored in order to accurately determine which applications are consuming the most energy or operating inefficiently. This stage may be performed over a seven-day period, to gain a complete picture of the plant’s typical energy use and productivity profile.
Data analysis takes the findings and identifies potential savings using dedicated software. The findings are presented with tables and graphs to help identify where savings are likely to arise. Among the data available are present energy usage, areas of potential savings, payback time if an investment is made in drives and/or motors, and CO2 emission reduction.
Recommendations consist of an action plan, usually comprising an executive summary and a detailed engineer’s report, highlighting applications that can benefit the most from using VSDs. The figures will be translated into monthly savings and there will be detailed recommendations for fitting particular drives or motors. The report also shows the expected payback time on fitting new equipment.
Implementation uses the recommendations from the appraisal and identifies the correct drive and motor for the respective application. ABB can help with the installation and start-up or commissioning of the drive and motor. Verification and follow-up analyses the new equipment in operation and looks at the energy savings achieved against the predictions shown in the engineer’s report, to help justify the investment in drives and electric motors.
Energy and CO2 savings with new toolkit app
Energy, CO2 and money saved, together with an estimated return on investment, are also the outputs of a new ABB App, called the AVP energy toolkit, which is designed to show the benefits of using VSDs and electric motors to replace direct on-line starting.
Within the App, which is available for download through the Apple App Store, users select their industry and whether they have a pump or fan application, along with their energy cost, motor rating, voltage and operating hours.
The App produces an instant mini-report to show the potential savings that can be realized.
The report contains details of a matched ABB motor-drive package and includes the energy savings, in MW hours, that the recommended package can achieve.
Details of the recommended VSDs and/or motors can be sent directly to one of ABB’s authorized value providers, if selected by the user. The nearest provider is identified by matching the users’ location details with that of the partner network. There is also a ‘Find my AVP’ function that allows the nearest provider to be located using the user’s GPS location, allowing an engineer authorized by ABB to be contacted anywhere in the UK.
A full quotation and engineers report can be requested and installation and commissioning of the recommended products arranged. Manuals, catalogues and brochures for ABB’s drives, motors and auxiliary equipment range can also be accessed via the App, giving users up-to-date resources and product information.
Campaign unearths true cost of running electric motors
To help motor users to make better-informed purchasing decisions, ABB have devised a simple formula which shows that the cost of ownership is equal to the purchase price plus the cost of running plus the cost of not running.
A campaign launched by ABB to raise awareness among end-users about the true cost of owning electric motors, aims to educate OEMs and end-users about the different elements that should be considered apart from the purchase price alone. Total cost of ownership is made up of a combination of the purchase price, the cost of running the motor in terms of the energy consumption over its lifetime and the cost to a business if that motor fails to run when needed.
For example, a 45kW motor costing £1,700, with 94.1% efficiency and running for 6,000h per annum would cost £2,105,454 over a 20-year life. This assumes an average electricity price of £0.08 and a downtime cost per annum of around £80,000.
When expressed as purchase price over total cost of ownership the resulting ratio is very small. For example, if the ratio was 1, this would mean that the purchase price was the same as the cost of ownership. But in the above example, the ratio is 0.0008.
Given such a high ratio, the true cost of owning a motor in a critical continuous process application is far more important than the initial purchase price. Buyers should, therefore, focus on the efficiency and the reliability of the motor.
The biggest risk and the highest cost for the motor owner is the cost of not running and unplanned outages through motor failure. High efficiency alone is not necessarily a guarantee of high reliability. When choosing a motor, consideration must be given to the full-load operating temperatures of the windings and the bearings.
Also, end-users and OEMs need to think about how motor manufacturers can assist in predicting when critical motors will fail, through on-site or remote condition monitoring and analysis, so that service interventions can be planned during scheduled plant shutdowns. And if the worst comes to pass and the motor fails between planned shutdowns, consideration should be given to how the manufacturer can get things running again as quickly as possible.
Use of the total cost of ownership calculation is not suitable for all motor users, only those that have critical motors running long hours. Nonetheless, end-users and OEMs alike should have the information to hand to be able to make informed choices.
For further information visit: www.abb.com
- Subscribe to Quarry Management, the monthly journal for the mineral products industry, to read articles before they appear on Agg-Net.com