Increasing the Life of Pump Wear Parts Threefold
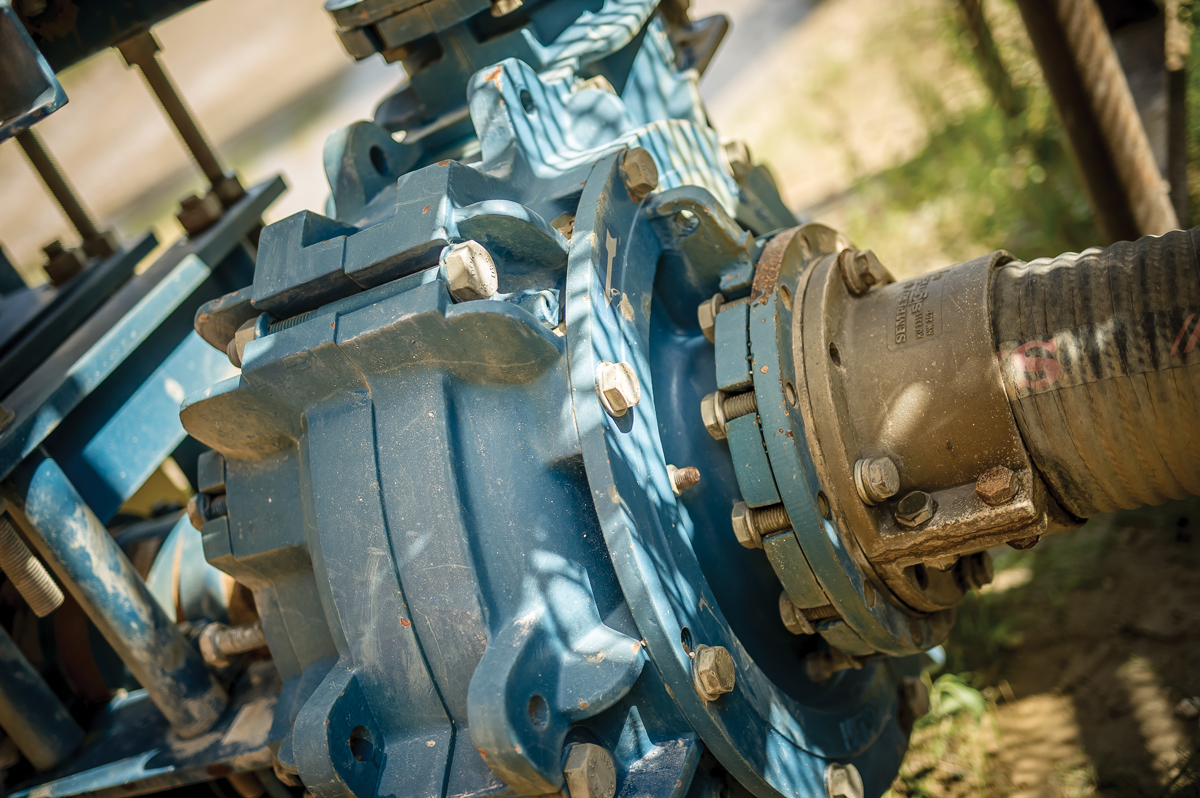
First published in the July 2019 issue of Quarry Management
Sand-treatment plants with wet process operations frequently face problems with excessive pump wear due to the highly abrasive nature of the product. GSM’s Montfrin-Meynes Quarry, in France, overcame maintenance problems by upgrading its cyclone module pump to a double-adjustment system that increased wear life by a factor of three.
GSM, part of the HeidelbergCement Group, are one of the leaders in the aggregates market in France, with 90 quarries and 670 employees. In the Languedoc region, the company manages nine quarry operations, including the Montfrin-Meynes site, near Nîmes, which produces 200,000 tonnes of alluvium materials per year.
The quarry extracts a silico-calcareous deposit with an abrasiveness of 1,980g/t. The material passes through a scrubber and a cyclone module powered by a Metso HR200 pump. Larger material is fed through a Metso Nordberg HP4 cone crusher to produce crushed sand of various sizes, which is then washed in a cyclone module fed by a Metso HR150 double-adjustment pump.
Double-adjustment solution
Since 2008, when Metso delivered their Nordberg HP4 cone crusher to the quarry, Metso’s service technician and the quarry manager have developed a good relationship, due in no small part to the technician’s emphasis on details that matter. Over time, it became evident that GSM were experiencing wear problems with previously installed cyclone module pumps. The wear parts needed to be replaced too often, maintenance was complicated, unsafe, and very time-consuming, and the quarry wanted to avoid expensive downtime.
‘We organized a meeting with the customer to examine the details of the problem,’ said Anthony Isse, the Metso service technician for this area. ‘We presented a Metso HR150 double-adjustment pump solution focused on ease of maintenance, increased safety, and a wide range of materials and advanced technologies to optimize the life of the wear parts.’
GSM studied the offer and the advantages of the pumps, especially the double-adjustment feature, which optimizes the replacement of wear parts and, therefore, reduces maintenance needs and increases the overall life of the pump. ‘We decided to invest in the HR150 double-adjustment pump because we also knew the after-sales follow-up would live up to our expectations, which was an important element for us,’ said GSM quarry manager Eric Viale.
Safety and ease of adjustment
The double-adjustment system recommended by the Metso sales and technical team provides a significant advantage for abrasive applications in which the impeller as well as the front and rear shields of the pump casing generally experience excessive wear.
The frame of double-adjustment pumps differs from standard pumps in that it allows optimum adjustment of the internal, front and back clearances of the pump. The rear wheel clearance is changed by means of an adjusting screw mounted on the pump. The front impeller adjustment allows the front play to be reduced. Both allow a constant front and rear play to be maintained to fully optimize wear part life times.
Cutting the budget by three
Thanks to Metso’s option of several sealing systems, pump casing linings and impellers, it is possible to configure a pump to the precise needs and optimize the process. This allows a pump to be adapted to any process changes.
In GSM’s case, the Metso HM150 double-adjustment pump was installed and optimized for the correct sand concentration. This rubber-lined pump with a high chrome metal impeller and a clear water pressure injection seal saw the maintenance needs of the operation drop significantly.
Eric Viale said: ‘After the reconfiguration, Anthony regularly monitored the wear of the parts and trained us to adjust the pump. We quickly saw that the life of the parts was three times longer than those of our old pumps. As a result, we stop much less frequently than before to change the wear parts, thanks to the optimization of their service life, which has allowed us to reduce the pump’s operating budget by a factor of three.’
He added that maintenance work on the pump during parts replacement is quick and easy, due to the impeller-release mechanism that rapidly allows uncoupling, and the system is also very safe during maintenance operations.
‘Added to all this, we also have the follow-up that we wanted from our after-sales technician, who continuously provides us with new solutions and trains our staff,’ said a very satisfied Mr Viale.
- Subscribe to Quarry Management, the monthly journal for the mineral products industry, to read articles before they appear on Agg-Net.com