Improving pump reliability and reducing water waste
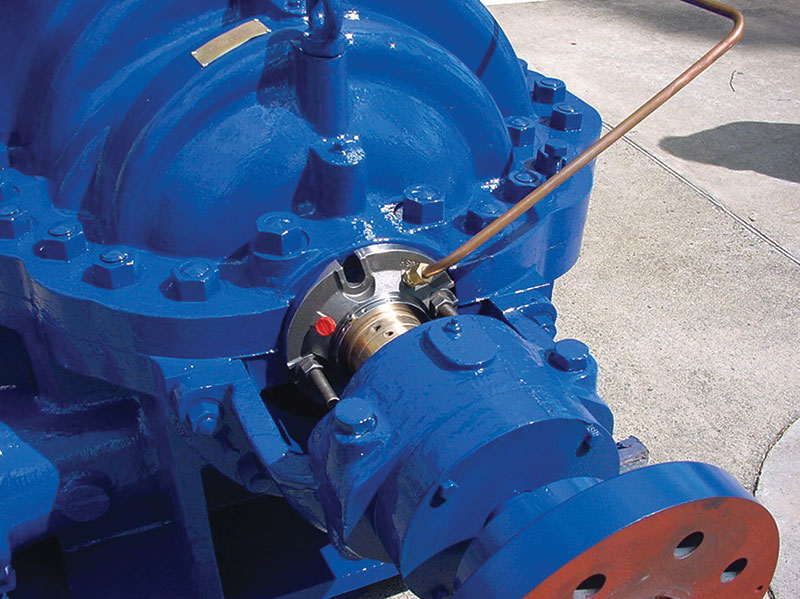
First published in the July 2015 issue of Quarry Management as Seal of Approval
The quarrying and mining industries can present a number of challenges for engineers centred on a scarcity of water and high-pressure transfer slurry pump applications. In this article, John Baills, sales director with AESSEAL Australia, looks at how upgrading from gland packing to double mechanical seals (fig. 1) ensures that the equipment is better able to deal with these demanding requirements.
Liquids carrying abrasive particles represent the most common type of slurry applications found in industry. The percentage of solids, concentration and particle size create a combination which will result in abrasion and seal failure, if the correct seal and seal environment is not properly selected. Gland packing is still used in the quarrying sector as a means of preventing liquid from escaping around the pump shaft. However, many engineers are choosing to replace this method with mechanical seals because the ‘leakage’ that occurs with gland packing can create a number of issues.
It is excessive leakage due to packing deterioration that is of greatest concern as it can result in environmental damage and equipment failure. Gland packing must be flushed with clean water to keep it cool and lubricated. A single large, conventional slurry pump consumes approximately 37.8 litres/min of water to cool and flush the packing. In one year, this amounts to more than 19.6 million litres of water added to the waste stream. Upgrading to a double seal and water-management system that recirculates the water instead of flushing it to drain or adding it to the slurry, can save 99.995% of this flush water.
When gland packing is used in high-pressure slurry pumps it is also prone to ‘slime out’, where the packing fails dramatically and almost instantaneously. Apart from the clear health and safety implications for nearby plant operatives, the leaking slurry cuts the pump bearing housing to pieces or, at best, penetrates into the bearing housing in a matter of minutes and destroys the bearings.
Furthermore, gland packing requires continuous labour because friction wears away the packing increasing the leakage rate until the packing is manually adjusted or re-packed to the original leakage rate. Moreover, whoever installs the gland packing has to ensure that they apply exactly the right amount of pressure on the shaft to create an adequate seal. If this is not done correctly, for example, with too much pressure, it results in shaft or sleeve wear and the pump will require more drive power to turn the shaft. Inadequate pressure, on the other hand, means there will be excessive leakage of fluid.
The following case studies illustrate how upgrading to mechanical seals from gland packing resulted in improvements to mean time between failures (MTBF), cost savings and limited detrimental impact on the environment.
Case study 1
A coal mine in Australia had used gland packing on three of its coal slurry transfer pumps for a number of years. However, the site engineers were concerned that the gland packing was failing after only six weeks’ operation and the yearly maintenance bill for the three pumps was more than A$135,000 (c.£67,000).
One of the concerns with the gland packing was that when it started to fail, it slowly caused the pump pit to flood. This resulted in the pumps having to be overhauled every 6–7 months, which proved to be both a disruptive and a time-consuming process. Leaking water was also causing bearing failures and each time this required a rebuild of the bearing barrel and change out of the stuffing box, sleeve, gland follower packing and lantern ring.
After carrying out an audit, an AESSEAL engineer recommended replacing the original gland packing on all three pumps with HDDSS (heavy-duty double slurry seals), together with W2 water-management systems operating in API Plan 53 configuration (fig. 2).
The new seals have eliminated leakage problems and increased MTBF to more than 24 months and counting. After providing a rapid return on the initial upgrade costs, the new seals have saved more than A$53,000 (c.£26,000) in the first year of operation and are currently saving in excess of A$130,000 (c.£64,500) per year from the maintenance budget alone. The equipment has been running for 13 months without failure or leakage, which represents a 242% increase in MTBF, and counting.
Case Study 2
A mineral sand slurry pumping application was fitted with gland packing and required 9 gallons per minute of flush water for proper operation. The high volume of flush water and excessive leakage of the packing was so severe that it created an artificial lake around the pump (fig. 3a).
The packing was replaced with a modern double mechanical seal and water-management seal support system, which virtually eliminated the leakage. Figure 3b shows how the double mechanical seal and support system, highlighted in red, eliminated the artificial lake.
A total of 24 pumps were upgraded to double seals, and three years after the installation the majority of pumps are still running the exact same seal and process. The water saving from 24 applications at 9 gallons per minute totals 113,529,600 gallons per year.
The customer’s engineers reported a return on investment period of three weeks, based upon the additional product they are now pumping, whereas previously they were pumping a high proportion of packing flush water.
Conclusion
It can be seen that there are a number of inherent limitations when using gland packing in certain applications. Although this method may appear to offer lower initial cost, when the lifetime cost is factored into the equation, together with subsequent reduction in MTBF, there are sound economic, efficiency and environmental benefits for investing in mechanical seals. The latest designs ensure long, trouble-free life for equipment, as highlighted in the case studies discussed above. For more information visit: www.aesseal.com
How it works – Double mechanical seals
A double or dual mechanical seal consists of two independent seals mounted within a seal chamber, which is flushed by barrier fluid from a water-management system.
The barrier fluid on double mechanical seals (usually water on slurry applications) maintains a clean, constant fluid film between the stationary and rotary seal face – effectively isolating the seal faces from the slurry.
This makes them ideal for sealing hazardous liquids, liquids with abrasives or liquids that are corrosive, as the seal faces only see clean lubrication, which greatly increases the seal life.
As a result, double mechanical seals are particularly suited to harsh, abrasive environments found in the quarrying and mining sectors.
- Subscribe to Quarry Management, the monthly journal for the mineral products industry, to read articles before they appear on Agg-Net.com