Energy Efficient Pneumatics
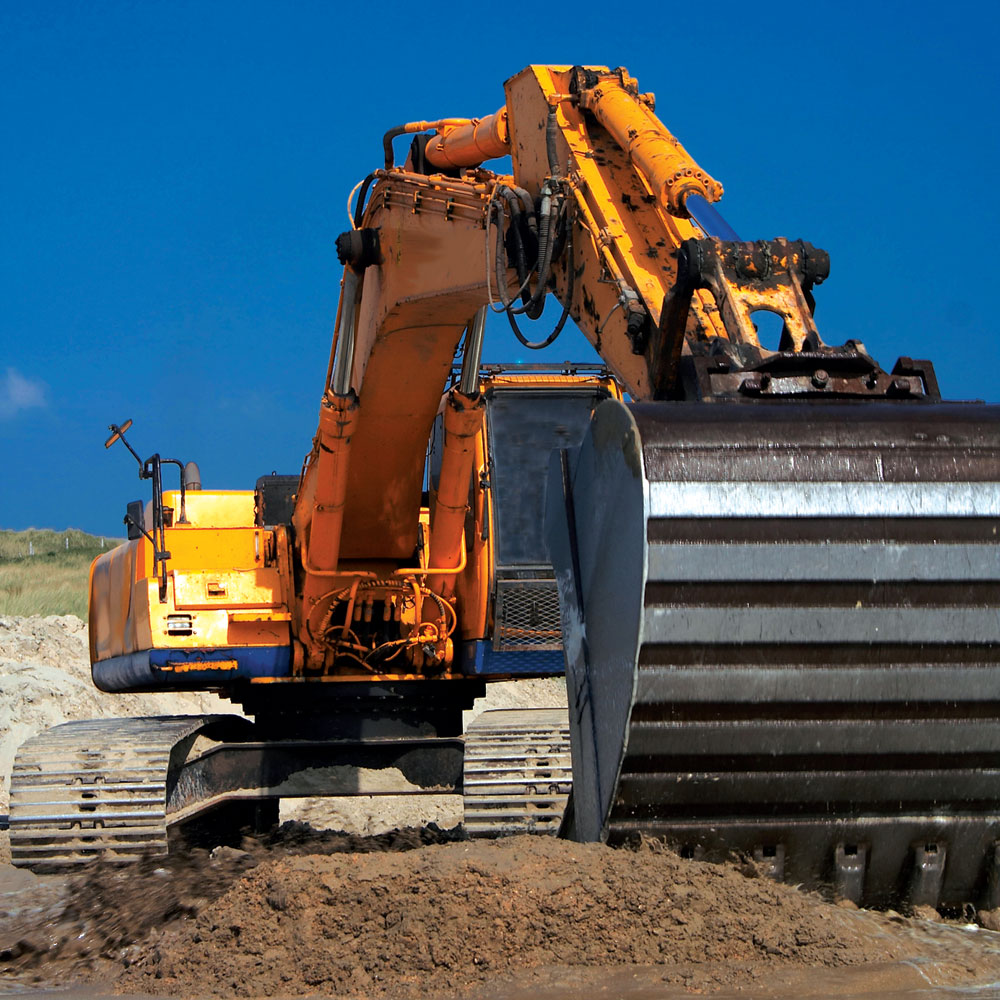
John Hill, marketing services manager for Parker Hannifin’s Pneumatics Division, explains how the energy consumption of pneumatic applications can be reduced considerably using the latest energy-efficient technology
As energy prices continue to rise, the need to minimize the energy consumption of quarrying operations is becoming increasingly important. To remain profitable and to keep costs down, companies are increasingly looking at their operations to find areas where energy can be saved. As the use of pneumatic systems is often accountable for a considerable proportion of the electrical energy consumed in a quarry, increasing the efficiency of equipment that uses compressed air can result in sizeable energy savings and a noticeable reduction in costs and environmental impact.
Typically, to reduce the energy consumption of pneumatic systems, operators focus on the efficiency of the compressors used. While upgrading compressors can have an immediate impact, this is just one of many areas where improvements can be made; what is not widely recognized is that a considerable amount of energy is often wasted downstream of the compressor. Installing more efficient filters, valves and cylinders can be a simple, fast and cost-effective way for companies to increase the efficiency of pneumatic systems.
Effective filtration
Effective filtration is essential to the efficiency of compressed-air systems. If filters are inadequately sized or become blocked, the performance of pneumatic equipment can be noticeably degraded. To ensure maximum output from the minimum input, fit-for-purpose filters should be used throughout pneumatic systems, from intake filters on compressors to in-line filtration downstream of the compressor.
It is important to check regularly that the compressor intake filters are clean and working effectively. Filter elements are often used for longer periods than is recommended by manufacturers, leading to a build-up of dirt and contaminants and, therefore, a drop in input pressure. This has a significant effect throughout the pneumatic system; no matter how efficient the downstream filters and components are, if the input pressure is reduced, performance will be impaired. The life of input filters can be extended by keeping the area around the filter clean using a physical barrier.
Although a relatively coarse filter fitted to the compressor intake is normally sufficient to protect the compressor, it is difficult to prevent particles smaller than five microns being drawn in; these pass through the compressor and can be fed, under pressure, to downstream equipment, together with moisture and vaporized compressor oil.
While this may not initially sound significant, a typical quarry environment contains millions of particles of dust, grit and pollen per cubic metre of air. When this is compressed the density increases dramatically, resulting in a build-up of contaminants on the internal surfaces of valves and cylinders, leading to wear, inconsistent operation and premature failure.
This problem can be prevented by using the latest generation of in-line air filters, which allow particulates and other matter to be removed without a significant drop in pressure across the filter.
When specifying filters, it is crucial that they are sized correctly to ensure that a higher degree of filtration does not have an adverse affect on flow rate, pressure drop and service intervals. Similarly, the correct sizing of valves and cylinders is crucial to optimize the efficiency of a pneumatics system and to minimize energy consumption and costs.
Pressure regulation and lubrication
Of equal importance as effective air filtration is pressure regulation, as excessive pressure can lead to increased energy costs, while low pressure may be unable to support the loads present downstream. Therefore, pressure regulators are generally used to control output pressures using a piston or diaphragm acting against a spring. It is important to consider both the peak and average demand when determining the required pressure for an application, as only a proportion of the total number of devices in the system is likely to be in operation at any one time.
Lubrication is also important to ensure that pneumatic components are able to operate efficiently and reliably. This is achieved by adding lubricating oil to the compressed air upstream of the components requiring lubrication. Although modern components are increasingly being designed to operate lubricant-free, thereby eliminating the need for the lubricator, once lubrication is added to a system it must be maintained, as lubricants can often wash away built-in pre-lube.
Modular technology
Modular technology, such as Parker’s Moduflex system, is now available to make building and installing a bespoke air-preparation solution simple, fast and cost-effective. These innovative FRL (Filter Regulator Lubricator) units use patented Cliplok connectors, which allow each module to be simply slipped into place and then locked securely in position using a robust and integrated clamp or over-strap. This method of construction allows a complete FRL assembly to be constructed in less than half the time taken for conventional devices, and the units can be built by an engineer or technician without the need for tools or special training. In addition, the clip-together assembly method eliminates the need for extra parts, such as pipe connectors, and allows individual modules to be removed or changed quickly and easily, so that system maintenance and downtime can be reduced to a minimum.
The quick-release, one-piece body design of this latest technology allows filter elements to be changed extremely quickly, ensuring that downstream pneumatic systems are maintained at optimum efficiency. This eliminates the problems encountered with some traditional systems, where elements are left unchanged due to the difficulty of the process, resulting in impaired system performance.
The latest robust aluminium filtration systems make choosing the right solution for a specific pneumatic application simpler than ever before, as a bespoke set of individual components can be connected together in each case. With pressure levels carefully regulated and maintained throughout the system, contaminants can be removed effectively, while the necessary pressure reaches the downstream components.
Efficient valves and cylinders
In addition to installing effective air-preparation systems, using efficient and correctly sized valves and cylinders is also vital in the drive to minimize energy consumption and costs. Pneumatic components are now available that have been developed to provide consistently high levels of efficiency under even the most demanding conditions.
For example, heavy-duty pneumatic solenoid valves are available from Parker that have been specifically designed for use in aggressive environments such as quarries. The Viking Xtreme valves are compact, rugged devices that can operate effectively at extreme temperatures as low as –40°C, and at pressures of up to 16 bar.
Unlike traditional solenoid valves, which typically use O-ring or lip seals between the valve spool and body, the heavy-duty valves feature a single-piece aluminium spool, over-moulded with a specially formulated rubber compound. This eliminates the problems of seals deforming or extruding, especially under conditions of high pressure or flow. As a result, the valves offer faster response times and minimal levels of spool break-away force or stiction, providing a highly energy-efficient solution.
Similarly, a new kind of mechanically coupled rodless cylinder has been designed that allows the energy used by pneumatic systems to be reduced still further. The new P1T rodless cylinder is believed to be the first of its type to eliminate almost entirely the problems of air leakage, while also providing exceptionally low levels of stiction and break-away force, providing highly efficient results.
With the latest design, air losses have been minimized by means of an innovative twin-seal design. This is achieved by using a longitudinal polyurethane body seal that lifts and passes through the body of the carriage as it moves, combined with a specially developed polyurethane piston seal that prevents air leakage from the inner face of the cylinder bore, at the point where the piston and carriage connect.
In addition to eliminating the problems of air leakage, this special design helps to reduce stiction and break-away forces, minimizing the energy required to operate the cylinder, as well as providing improved positional accuracy and far smoother operation, especially at start-up and at low operating speeds down to 2mm/s.
When sizing cylinders, the three key considerations that must be determined are the amount of thrust or clamping/holding force required, the air pressure available and the operating efficiency of the cylinder, based on its type or method of manufacture. Similarly, correct valve sizing can only be achieved once factors such as the required flow rate, working pressure and acceptable pressure drop across the valve are known. If in doubt, the best way to ensure that components are sized correctly is to work closely with a leading supplier who can help maximize the efficiency of the pneumatic system.
Summary
With quarrying companies coming under increasing pressure to protect themselves against rising energy costs and minimize their environmental impact, reducing the energy consumption of pneumatic equipment is more important than ever. By using the latest generation of energy-efficient pneumatics technology, including modular FRL units, valves and cylinders, and by ensuring energy losses are minimized throughout the system, operators can achieve these objectives simply and cost-effectively, with a positive impact on their bottom line.