Breaking Up Is Hard To Do
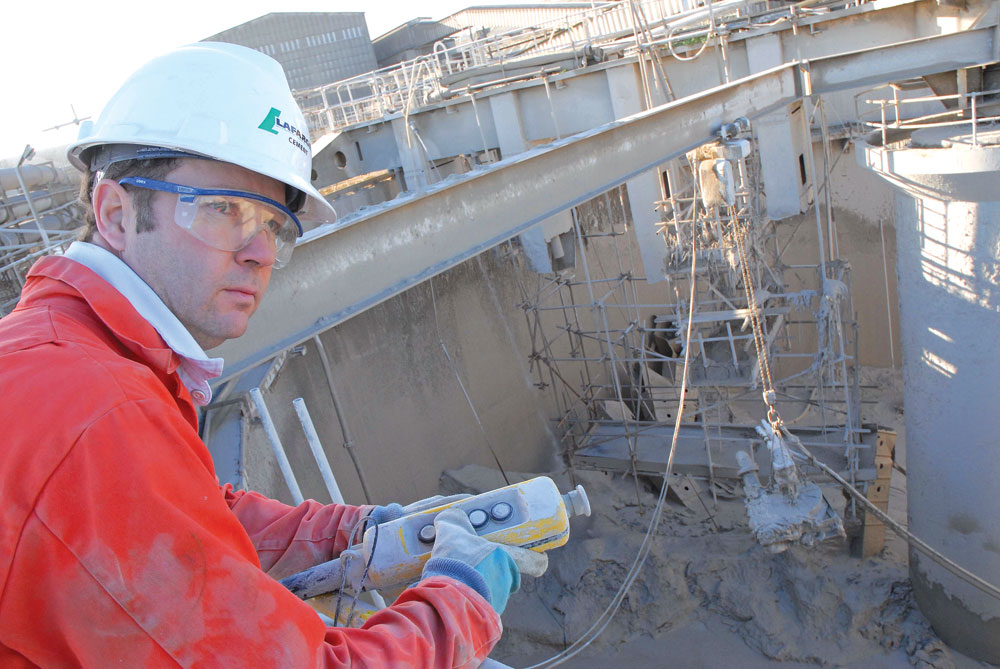
Sweepax pumps tackle hardened slurry with ease at Northfleet
Northfleet in Kent has been the site of cement production since Joseph Aspdin, a bricklayer from Leeds, first took out a patent for what is now known as Portland cement and set up a cement works there in 1824. The most recent Northfleet Works was opened in 1970 and, until this year, produced more than 1 million tonnes of cement each year for customers throughout the south of England, making it the largest cement works in the UK.
Now, almost 200 years after it first began, cement production at Northfleet has come to an end, following Lafarge’s sale of its Northfleet Works as development land for luxury riverside apartments. With its close proximity to the M25 and prime location on the bank of the river Thames, the redevelopment of this historic location comes as no real surprise.
However, clearing-up the site in preparation for decommissioning did hold a few surprises for silo-cleaning specialists RJS Silo Clean International Ltd, for whom the challenge of removing hardened sludge from three huge slurry tanks proved no small undertaking.
Compacted over the course of many years at the bottom of Northfleet’s iconic storage tanks, the material that had to be removed before the tanks could be demolished had become a mass of hardened slurry which could no longer be pumped out by conventional means. The challenge for RJS Silo Clean was not only to clean the tanks, but to do so in a way that would allow Lafarge to recycle the slurry as saleable product before each of the storage tanks was decommissioned.
Ordinarily, RJS Silo Clean use their vacuum tanker for cleaning out silos and sucking up spillages. However, the material in the tanks at Northfleet was so hard, and man entry to the tanks so dangerous, that the company had to find an alternative solution.
‘The slurry at the bottom of the tanks had collected and settled over such a long period of time that it was extremely hard,’ explained Jason Johnson from RJS Silo Clean. ‘There was no way that we could empty the tanks without first finding a way of breaking up the slurry.
‘Fortunately, we had tackled a previous silo-cleaning job on the same site about three years earlier and Sykes Pumps had been able to provide us with a specialist pump to break up the sediment, so that it could be pumped out of the tank. As this had proved a convenient and cost-effective method of cleaning the tank for that project, we opted to use the same approach again and contacted Sykes for their advice.’
A specialist approach
The first step for Sykes Pumps was to send a specialist sales engineer to the site to complete a site survey and gain an understanding of the exact application at first-hand.
‘Even though we had supplied equipment to RJS Silo Clean for a similar job at the same site a few years earlier, this was an important starting point for determining how RJS and ourselves were going to overcome the logistical issues of manoeuvring the pumps,’ commented Steve Gray of Sykes Pumps. ‘It also provided an opportunity to assess the nature of the slurry.
‘It was clear that the material in the tanks was tougher than anything that an ordinary pump could handle. Added to this were the challenges posed by the enormous size of the tanks, which meant there was a very large volume of slurry in each one and a wide surface area for any equipment to cover.’
The tanks were cleaned one at a time, using two specialist Sweepax submersible hydraulic pumps, both of which were placed inside the tank at the same time. These large 700kg pumps are capable of pumping material that is up to 50% dry solids. However, their role in this project was not to pump the slurry, but to break it up into a pumpable material. Once this had been done, the slurry could be pumped out via the tank’s integral pumps for reuse.
A specialist pump available only from Sykes Pumps in the UK, the Sweepax features a central petal blade that spins round extremely quickly when the pump is in operation. It was this blade that was used to cut through the sludge, allowing the pump to throw the macerated materials back down into the bottom of the tank so that it could be pumped out as normal.
Once RJS Silo Clean had designed a solution for removing the slurry from the tanks, the next hurdle was to find a way of operating the pumps within the tanks with the manoeuvrability required to break up all the hardened slurry.
In preparation for the pumps, a moveable beam was constructed from steel inside each tank to act as a platform from which the Sweepax pumps would be suspended. The two Sweepax pumps were lifted into position by crane and connected to an electrical hoist that was installed on the beam. This meant that the pumps could be moved around easily within the tanks and positioned correctly to carry out the job of breaking up the sludge across the entire area without having to be lifted out and repositioned each time the RJS team was ready to move on to a different part of the tank.
‘Each of the two Sweepax pumps weighs 700kgs and the tops of the tanks are over 40ft off the ground, so the pumps had to be lifted into position using a crane,’ explained Mr Johnson. ‘However, lifting them by crane every time we needed to move them would have been costly and impractical, so the moveable beam and electric hoist within the tank was the ideal solution, helping us to manage costs and increase the rate of progress.’
Delivering results
‘Cleaning the tanks was a time-consuming and frustrating process, but it’s hard to see how it could have been done without the aid of the Sweepax pumps,’ said Mr Johnson.
‘We were expecting very thick slurry, but it was even harder and more compacted than we had expected, so each tank took months to complete. The size of the tanks and the sheer volume of material that had to be broken up made the project extremely challenging and alternative methods would have been cost-prohibitive.
‘With the Sweepax pumps, we found an effective method of breaking up the slurry so that we could achieve the dual aims of cleaning the silos and recycling the material for reuse. Not only that, our experience of seeing just what the Sweepax could do gave us peace of mind because we knew that if there were any issues with the tanks’ integral pumps, the Sweepex would be more than capable of pumping the softened slurry.’
‘This was a demanding and unusual project but that’s what the Sweepax pumps specializes in,’ added Mr Gray. ‘It can cope with working environments, sludges and slurries that would simply be too challenging for other hydraulic submersibles, and that’s why we’ve invested in ensuring it’s an important part of our fleet.’
Sykes Pumps, Premier House, Darlington Street, Wolverhampton, W. Midlands WV1 4JJ; tel: (0800) 211611; email: info@andrews-sykes.com