Abrasion-Resistant Pumps and Valves
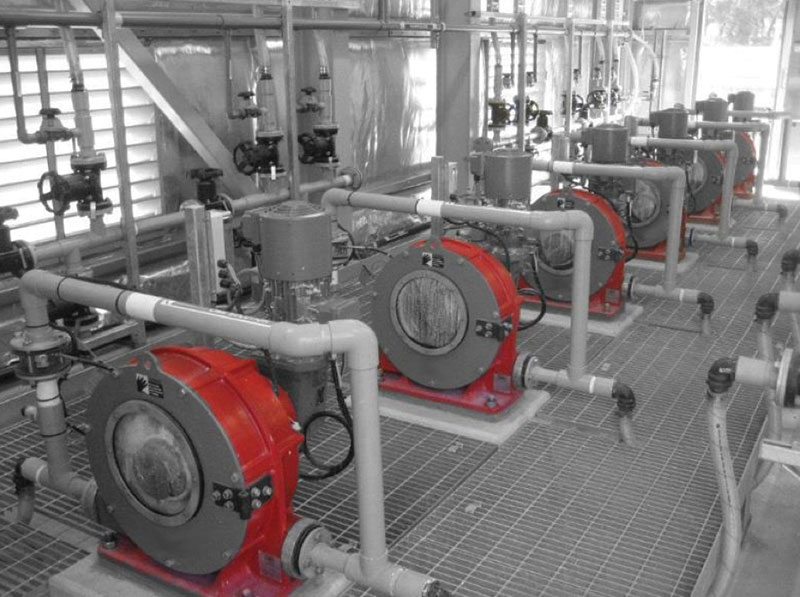
First published in the July 2015 issue of Quarry Management
Dave Fitzpatrick, managing director of Cheshire Pump Company Ltd, offers some valuable insights into pumps, pumped systems and fluids
The majority of pumps used for dewatering, slurry handling and a number of other processes in the quarrying industry tend to be centrifugal (roto-dynamic) types, that is they have rotating parts that create the force that moves the water. If the process stream contains abrasives (which it invariably does), hard materials are used for the impellers, back plates, wear plates and shafts. The more demanding the process, the harder the materials used.
There is a well known pump industry statement that most pump breakdowns are caused by seal failure. Mechanical seals are used to overcome seal wear, and while seals are seen as the weakest link in the chain and tend to fail first, they are not always the root cause of the problem.
High-viscosity fluids generally need more energy to move them than low viscosity fluids – think of viscosity as the resistance to movement. Dynamic viscosity is stated in centipoise (cP). It is commonly used because water at a temperature of 20°C has a viscosity of 1.002cP; pump test and performance data is stated ‘in water’ (1cP).
Below about 300cP, and dependant on fluid type and system detail, roto-dynamic (RD) pumps are generally used, eg centrifugal pumps, submersible pumps etc. Generally, RD pump quantity/head (Q/H) curves go from zero flow at maximum pressure (closed valve) to maximum flow at minimum pressure. Depending on impeller design, the greater the flow, the greater the power required.
Positive displacement (PD) pumps are used for fluids with a viscosity that is usually greater than about 300cP. PD pumps are available in a number of forms: rotary PD pumps, such as peristaltic pumps, gear pumps, progressing cavity pumps, rotary lobe pumps; and reciprocating PD pumps, such as plunger piston pumps, mechanical diaphragm and hydraulic diaphragm pumps.
Crucially, peristaltic pumps are not adversely affected by variations in viscosity and some can be operated in reverse direction, allowing system blockages to be ‘back-pumped’.
It is necessary to consider the fluid density and slurry type:
Light slurry: Presence of solids is unintentional. Solids size typically <200 microns. Non-settling solids remain in suspension. Specific gravity <1.05. Less than 5% solids by weight.
Medium slurry: Solids size 200 microns up to 5mm. Settling or non-settling slurry. Specific gravity <1.15. From 5% to 20% solids by weight.
Heavy slurry: Main purpose is to transfer material, ie sand & gravel. Solids size >5mm. Settling or non-settling slurry. Specific gravity > 1.15. Greater than 20% solids by weight.
To understand positive displacement pumps, it is necessary to investigate their place in the pump world:
A – Roto-dynamic pumps (centrifugal pumps, submersible pumps)
B – Rotary positive-displacement pumps
C – Reciprocating positive-displacement pumps
The reciprocating and peristaltic designs are most suitable for high viscosity, variable viscosity and metering applications, as can be seen by comparing the flow (Q) and pressure (P) curves of the three types (see fig. 1).
A – Centrifugal pumps are ideal for fluids that are ‘water’ based, eg low-viscosity sewage and waste water. Usually an RD pump curve is shown as a QH curve with pressure shown on the vertical axis and flow in the horizontal axis.
B – Rotary PD pumps are ideal for constant-viscosity clean media, such as oils, however they will suffer from an effect called ‘slip’ with changes in fluid characteristics.
C – Peristaltic pumps, in particular, are largely unaffected by viscosity and can pump abrasive and aggressive media. All PD pump flow rates can be varied by speed or stroke length in the case of reciprocating types. If it is possible to get the fluid into a pipe, a peristaltic pump will move it.
There are a number of misconceptions about some peristaltic designs:
- You cannot run them continuously – You can if you get the right product. Check the pump curves to see if there are any limitations on running time across any portion of the performance field caused by run time or temperature. If there are, and it if it impacts on the duty you need, do not use it (see the footnotes on fig. 2).
- You have to stock shims or packing to adjust the pressure on the pump hose to obtain optimum performance – Not if you buy the right pump. Most peristaltics use this system, however manufacturers such as Flowrox have an adjustable contra-rotating roller design (fig. 3).
- Peristaltics use large volumes of lubricant in the hose chamber – Not if you use the right pump A roller design that rubs the hose creates friction heat and limits hose life. A design that rolls around the hose squeezing it, all but eliminates this and needs minimal quantities of lubricant and will offer extended hose life.
- Fitting a round hose into a circular chamber deforms the hose making it elliptical and reducing performance – Not if you use hoses that are pre-formed into the correct shape, and even more so if the inlet and outlet ports are opposing and in line.
The use of peristaltic pumps for some applications, especially processes such as thickener underflow, filter-press feeding and slurry transfer, has additional benefits.
If the process is thought of as a bulk transfer of solids rather than a volumetric fluid flow, it is possible to start to think about moving the solids not the water. Make the process thicker, reduce water usage, increase the solids transfer.
The most obvious aspect of peristaltic pumps is that most have only one wear part – the pump hose, made from an elastomer to suit a particular process stream and pressure rating. Combine this with equipment such as pinch valves, which again have one wear part made from similar elastomers, and it is possible to change the whole life cycle of a plant. No more spare impellers, wear plates, shafts, seals, cases, worn leaking and jammed valves, just one spare hose, a small quantity of lubricant and a few valve sleeves – simple as that!
- Subscribe to Quarry Management, the monthly journal for the mineral products industry, to read articles before they appear on Agg-Net.com