World launch of the new WashPod
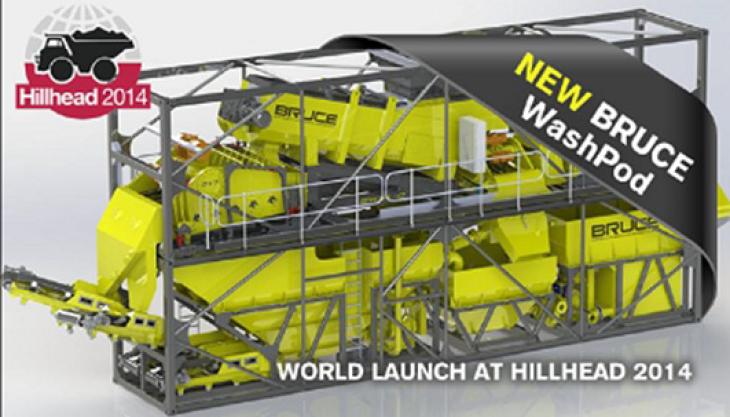
Bruce Engineering using Hillhead to introduce their new, compact and highly mobile washing plant
IT scrubs, washes and separates; it has the footprint of a 40ft container; it is compatible with any screen and crusher; and it is easy to set up and manoeuvre – it is the new WashPod from Bruce Engineering.
Bruce say they have listened to the aggregates recycling industry where, with space often at a premium and demand for quality-concrete aggregates increasing, many producers are turning to the washing of secondary and recycled materials to manufacture sized gravel and sand products.
With the introduction of the new WashPod, aggregate scrubbing, trash removal, aggregate rinsing/sizing and sand production are all achieved on one simple chassis, compatible with any mobile screen or crusher.
In the past, decision-makers in the industry may have been discouraged from introducing a washing process into their already multi-faceted businesses because of four main factors: capital outlay; the static nature of such plant; the size of the plant; and the complexity of its operation.
Capital outlay
Traditional aggregate washing plants often have purchase budget costs measured in millions of pounds which, even for directors of established companies, can be viewed as a risk too far for the introduction of a new, and in some cases experimental, process. Now, with the new WashPod, the decision to move into aggregate washing is not so substantial.
Static nature of plant
Even with existing so-called ‘mobile’ or ‘modular’ systems, set-up times can often run into weeks and they generally require considerable site input in terms of civil engineering and planning compliance. Moreover, once a plant is up and running it can be a huge upheaval to move it to another location. The WashPod requires only two standard twist-lock trailers to be mobile.
Size of plant
In many cases companies simply do not have the room to consider washing, but with the footprint of a shipping container, excluding ancillary equipment, the WashPod opens up the possibility on most sites.
Complexity of operation
With its clear and accessible operator interface, the WashPod makes it very simple to produce two aggregate products and one or two sand products, while its plug-and-play operation, easy transport options and compatibility with Bruce’s range of silt-management solutions, mean any company can be self-sufficient in concrete aggregates in very quickly.
One of the first WashPod units has already been purchased by Barr Quarries Ltd. Operating from 12 sites in south-west Scotland, the company provides a wide range of heavy-side construction materials, including asphalt, concrete, stone, sand and gravel, recycled construction materials, and soils.
Having identified a need for a compact washing plant, when Bruce unveiled their new and innovative design, Barr found that the WashPod was exactly what they required. Director Colin Morrow said: ‘We believe its mobility is a real plus, allowing us to set up quickly, wash, and move on to the next site without the normal high transport costs. We will use this equipment to continue to deliver benefits to our customers in the markets we serve.’