Wight Building Materials invest in filter press
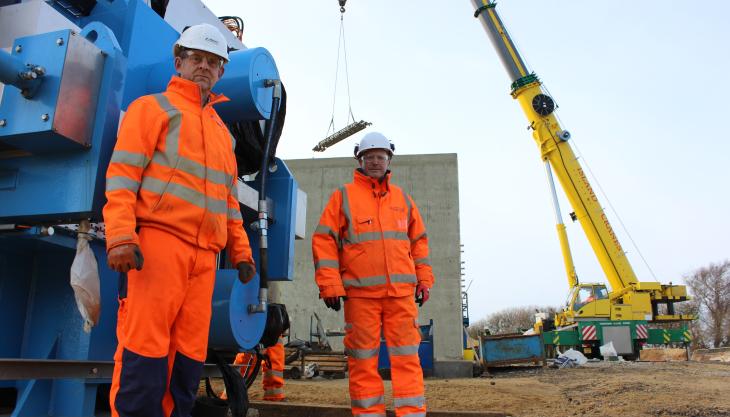
New multi-million-pound Isle of Wight project set to deliver environmental and economic boost
A NEW multi-million-pound project is under way to make sand and gravel extraction at Wight Building Materials among the most efficient and environmentally friendly in the UK. The company has begun the installation of a filter press that will significantly reduce the amount of water used in the processing of aggregate materials.
The British-made filter press – the only such machine of its kind on the Isle of Wight and one of only a few in the UK used in aggregate production – also means that material produced as a by-product of sand and gravel extraction will be of higher quality and more quickly available for quarry restoration. In addition, far less land and fewer lorry movements will be required in the treatment process.
It all means that water used in the process of sand and gravel extraction will be reduced by 70% and the water that is required will be recycled for other uses in the business.
Installation of the press is under way and it is expected to become operational in July – ending the traditional practice of using large lagoons to naturally filter water away from extracted materials before this by-product is dry enough to be used in landscaping. These lagoons, which have been used for more than 50 years, can now be decommissioned and restored to nature.
Wight Building Materials say the investment in the new technology complements their commitment to managing their land in a sustainable way and will assist their ongoing work with Hampshire and Isle of Wight Wildlife Trust to restore quarried sites at St George’s and Prospect Quarry, near Shalcombe, into prime natural habitat.
Steve Burton, Wight Building Materials’ general manager, said: ‘Currently, the existing sand and gravel processing produces a wet silt slurry waste product that is around 75% water. This has to be stored in large settlement lagoons until it is dry enough to be used for restoration, at which point it is removed and taken to the required location by lorry.
‘The filter press will treat the processed silt prior to discharge to lagoons by mechanically squeezing out most of the moisture to produce a semi-dry material that can immediately be used for constructing landscapes in restoration. This process will be repeated up to eight times per day creating a steady supply of suitable material that can quickly be used for WBM’s ongoing restoration work.’
Mr Burton added: ‘It is a major investment and also a major logistical project for us to undertake, but we are a company that is committed to doing the right thing. We pride ourselves in operating to the highest standards in all we do and, as custodian of such important sites, we want to ensure that we look after the environment around us in the most responsible way.
‘We are also proud of our Isle of Wight roots, and another welcome aspect of this project is that we are using, wherever we can, Island businesses to help install the filter press, which means partnering up many local companies working in civil engineering, electrics, pipework, craneage, transport and construction.’