Wentvalley take delivery of new Liebherr R 976
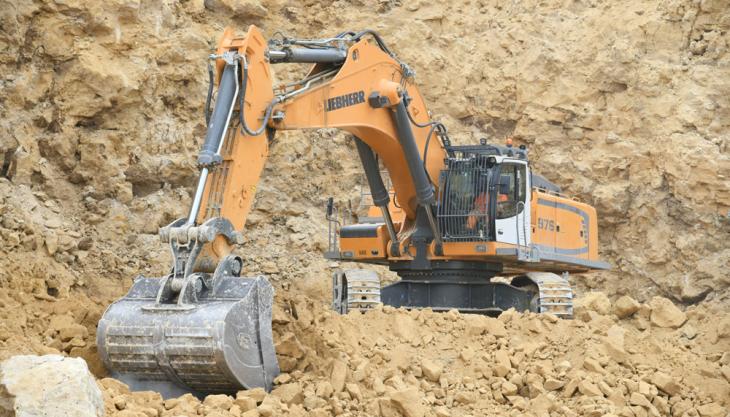
Firm invests in heavyweight prime mover to maintain feed to 90-tonne primary jaw crusher
YORKSHIRE-based quarrying and recycling specialists Wentvalley Aggregates & Recycling Ltd have taken delivery of a new Liebherr R 976 crawler excavator to feed their 90-tonne jaw crusher.
The company owns and operates a state-of-the-art recycling facility within the grounds of a yellow limestone quarry in West Yorkshire where recycled material is sold alongside virgin material extracted from the quarry. The operation, which has been going for more than eight years, is owned and run by Russell Meakin and currently produces in excess of 1 million tonnes of mixed material per year.
There has been significant investment in upgrading plant and equipment to deliver a constant flow of material and when the company invested in a 90-tonne GIPOREC R170FDR jaw crusher, an equivalently substantial machine was needed to load it in order to maintain the high production rates required at the quarry.
Having successfully used a Liebherr R 974 excavator for almost a decade, Wentvalley decided to purchase the 80-tonne excavator’s replacement model and have recently taken delivery of a new R 976. ‘We looked at other manufacturers but have had a good relationship with Liebherr,’ said Mr Meakin.
Regular operator of the machine, Rob Netherwood, has been operating excavators for more than 40 years and praises the Liebherr product: ‘I have been on a number of Liebherr excavators over the years, starting with an R 932, and when they are set up right, they are by far the best diggers out there. We need a large excavator on site to keep up with the crusher. Anything smaller than this would really struggle.’
Equipped with a 5.5 cubic metre direct-mount bucket, the R 976 has been supplied with a 7.2m mono-boom and 3.3m dipper, which is designed to give a combination of excellent breakout force and reach to load the crusher’s hopper. Mr Netherwood is able to reach sufficient material to keep the crusher operating for about half a shift, working on a 3–3.5m high bench of blasted material.
The combination of a 14.1-tonne counterweight and a heavy-duty 3.5m wide undercarriage ensures the excavator remains totally stable even at full reach with almost 10 tonnes of material in the fully outstretched bucket, which is a larger capacity version than on the older machine.
Once the pile of blasted material has been exhausted, the team can quickly reposition the feeder conveyor, crusher and excavator to the next bench where operations are resumed for the remainder of the shift.
Fitted with 600mm double-grouser shoes, the excavator has ample traction to get up on to the loose material, whilst the large, heavy-duty galvanized access ladders mounted to the track frames have been designed to deflect any errant rocks. Combined with a sturdy handrail and access catwalk, the climb to the cab is quite easy and Mr Netherwood is generally pleased with the upgrade on the Liebherr cabin compared with the older R 974.
Power to the excavator comes from a Liebherr 16-litre V8 engine that delivers 544hp at 1,800 rev/min. An AdBlue SCR system brings the engine up to Tier 4f exhaust emission standards, with the machine claiming to be more fuel efficient than its predecessor.
For Wentvalley, however, production is the most important thing: ‘We need to get the material out of the gate and to do that we need to put it through the crusher, and the Liebherr helps us achieve that,’ said Mr Netherwood.
A ground-level reach of almost 13m means a large area of blasted material can be cleared around the excavator before it needs repositioning, whilst a load-over height of more than 8m allows the R 976 to work on the quarry floor when, from time to time, it is called upon to rip out areas to expose suitable material.
‘Without the weight and power of this machine, we wouldn’t be able to do this job,’ said Mr Netherwood, who was keen to mention Liebherr’s service provision: ‘The older machine was looked after by the Wigan depot and the backup we had from them was exceptional. We are hoping for more of the same from the Sheffield branch, as and when we need it.’