Washing success for CDE Asia
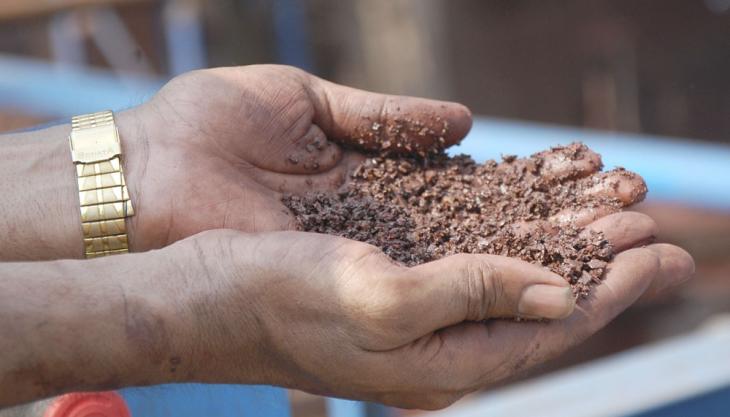
New iron ore washing plant improves feed material Fe grade and metallization for Indian steel maker
A NEW iron ore washing plant installed for Monnet Ispat and Energy (MIEL) in Raigarh, India, has resulted in significant efficiency gains as a result of effective removal of unwanted fines and slimes.
The main problem facing MIEL was the high level of variation in the feed material as a result of it being sourced from a variety of mines rather than a single consistent resource. A high fines content, in particular, was causing most concern as this was resulting in a significantly reduced campaign life.
The new washing plant from CDE Asia effectively removes all of the low-grade fines and slimes which results in a higher-quality ore. This not only increases efficiency in the kilns but has also results in a washed ore product that MIEL are able to sell to export markets at a premium price.
MIEL invested in the CDE washing plant after CDE Asia conducted extensive testing of the feed material to establish the quality improvements that it was possible to achieve.
‘We were able to demonstrate to MIEL that they would enjoy considerable benefits from the installation of our washing plant in the quality of the material processed, ability to handle variation in ore quality, segregation of feed material for different kilns and, of course, reduction of contaminants,’ explained Dr A. Bandyopadhyay, president – technology with CDE Asia.
The new processing plant delivers three products: a –25mm +5mm product; a –5mm +2mm product; and a –2mm +0.075mm product.
Following washing of the iron ore fines through a CDE EvoWash system, waste water is delivered to an AquaCycle thickener which ensures that approximately 90% of the water used is recycled. This significantly reduces the volume of fresh water required to feed the washing plant and makes this sort of process possible where there are restrictions on water availability.
Prior to the introduction of the CDE washing plant, some 7% of the –5mm product comprised –75 micron material, which was the major cause of the inefficiencies being experienced by MIEL in their steel-making processes.
The new plant has reduced this percentage to 1.5%, which has not only improved the Fe grade of the feed material and increased kiln campaign life, but has also resulted in improved metallization.
‘The CDE washing plant installed in our Raigarh operation has increased the campaign life of the kiln by 10% and the yield by 2%. Also, the metallization has improved considerably,’ said S.V. Parameshwar, assistant vice-president of MIEL’s Sponge Iron Division.