Vacu-Lug continue to provide tyre support for Viridor
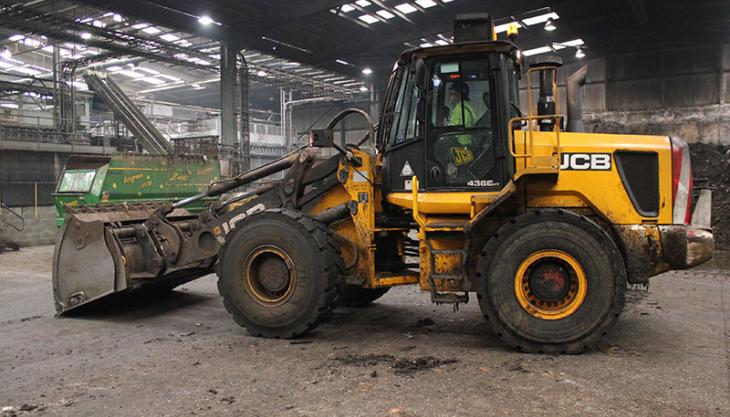
UK recycling operator enters 30th year of using Vacu-Lug tyres for its North West waste-handling operations
VACU-LUG Traction Tyres are entering their 30th year of tyre supply and support to Viridor, one of the UK’s leading recycling and waste-management operators. The tyre specialists have been providing tyre supply/support as part of Viridor’s long-term contract with the Greater Manchester Waste Disposal Authority.
Viridor manage over 30 locations with more than 200 vehicles across their fleet, including 110 lorries, 55 loading shovels, 14 fork lift container handlers and 22 wheeled excavators, The sites include: household waste recycling centres (HWRCs) across the Greater Manchester area; as well as advanced recycling and recovery facilities, some of which have attached railhead terminals.
The waste and recycling of over 1 million households from nine Greater Manchester districts (Bolton, Bury, Manchester, Oldham, Rochdale, Salford, Stockport, Trafford and Tameside) is processed within these facilities.
The wheel loader fleet is predominantly JCB 436 and 456 models, while the remaining loaders consist of Case and Caterpillar machines. These are using a combination of Vacu-Lug puncture-proof Tyrfil tyres (MTK 5 104s) specifically designed for the waste industry.
According to Vacu-Lug, these tyres feature a unique tread design and offer long service life, making them suitable for waste, glass and recycling operators looking to keep costs to a minimum.
At Viridor’s Longley Lane facility and railhead in Manchester, where four of the company’s 25-tonne container handling fork lift trucks operate, vehicle downtime must be avoided to ensure strict adherence to train timetables and integration with other Viridor facilities.
To ensure the general smooth running of all vehicles in the fleet, Vacu-Lug are managing the contract with the supply of new and remould tyres which are inspected on a rolling monthly cycle and rotated through different positions on each vehicle to optimize wear and increase tyre life.
The management process also helps Vacu-Lug to closely monitor each tyre, where, if necessary, it can be removed from the vehicle early enough to be remoulded for a second and third time, which further reduces costs and contributes to Viridor’s ongoing environmental awareness programme.
As part of the long-term running contract with Viridor, Vacu-Lug have implemented a forward tyre-replacement programme. This allows tyres to be quickly replaced when needed and avoids costly machine downtime. Vacu-Lug also provide 24h a day, seven days a week support by using their own in-house technicians and numerous tyre service partners.
When each tyre inspection is completed, the date is logged and should any work need carrying out, the details are forwarded via Vacu-Lug’s online VFM (Vehicle Fleet Management) system to the appropriate service provider who will, subsequently, complete the requisite task and record the details on a database.
Commenting on the long-standing relationship between the two businesses, Dave Rogerson, asset maintenance engineer at Viridor, said: ‘Waste handling is a continual process which requires uninterrupted mobility of all support vehicles and wheeled equipment. To this end, the Vacu-Lug team works closely with Viridor, often calling on their extensive practical knowledge and experience, to ensure minimum downtime and maximum efficiency.’