Two new Volvo loaders for LKAB Minerals
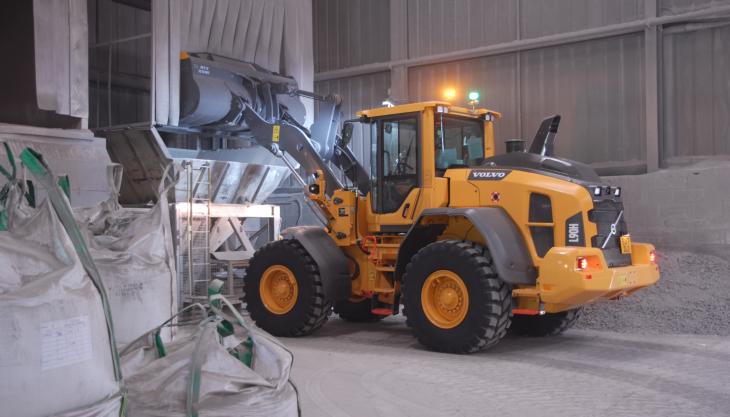
Industrial minerals group maintains long-standing tradition of operating Volvo loading shovels
UK-based LKAB Minerals Ltd are continuing a long-standing tradition of operating Volvo loading shovels with the addition of a new L90H loading shovel and with a second unit on order for delivery this autumn.
The new 12-tonne loading shovel has been supplied complete with a 2.5 cubic metre direct-mount straight-edged bucket for handling refractories from the company’s recycling facility near Sheffield.
‘Both the size of the machine and especially the size of the bucket are the key to handling the variety, weight and density of the materials arriving here on site,’ explained works manager Simon Hallissey.
‘Here at Bagmoor Lane, we receive a whole variety of refractory materials – ranging from alumina 55 to slag coming from chrome metal production – which can have densities anywhere between 2 and 4 tonnes per cubic metre, and are therefore extremely heavy.
‘The L90H and bucket combination is proving to be the optimum solution for handling this type of diversity and not least for loading the hoppers for the crusher, drying plant and screens.’
LKAB Minerals Ltd have been operating Volvo loading shovels for the past 22 years, thanks to their consistent product quality coupled with first-class customer service, as Mr Hallissey explained: ‘Our operation here at Bagmoor Lane is tough on the machines because the material is both highly abrasive and creates a lot of dust when loading the hoppers inside the sheds.
‘Volvo Construction Equipment fully understand our needs when it comes to specifying the machines to cope with the application, and the after-sales service they provide from their Immingham support centre is excellent.’
The L90H supplied to LKAB is powered by a Stage-IV final Volvo 6-litre engine that develops 186hp with a maximum torque of 853Nm at just 1,400 rev/min.
To meet LKAB’s specification requirements, the machine has been equipped with an optional reversible cooling fan and an oil bath air cleaner coupled to a Turbo II pre-cleaner. The machine is also fitted with an RDS Loadmaster system.
The new L90H joins an existing L90G model and has been put in charge of loading a variety of material into the main crusher, then rehandling the crushed material into the drying plant, and finally on to the screening plant where it is bagged, ready for dispatch.
The machines are operated on a 16-hour, two-shift-per-day system at Bagmoor Lane. Similarly, there are two Volvo L50 machines and an L90 shovel working across the five LKAB facilities across the UK.
The L90H, as with LKAB’s other Volvo loading shovels, has been supplied complete with a Volvo Gold Service agreement, which is, in effect, a full repair and maintenance programme offered by Volvo CE. Apart from fuel and oils, Volvo take care of the uptime running of the machines, giving LKAB Minerals complete peace of mind on machine availability.
Paul Boustead, operations director at LKAB Minerals, said: ‘LKAB Minerals have enjoyed a long-term partnership with Volvo CE, with machines matching our expectations of high-reliability performance and operational cost-efficiency.
‘As we seek to further improve our business performance with the LKAB Operational Excellence Programme, the efficiencies gained through partnering with Volvo CE and selecting this model in terms of reduced fuel consumption, improved environmental performance and reduced total running costs, made the decision to replace our existing machine with the next-generation Volvo very easy.’