Turning off-spec particles into premium sand
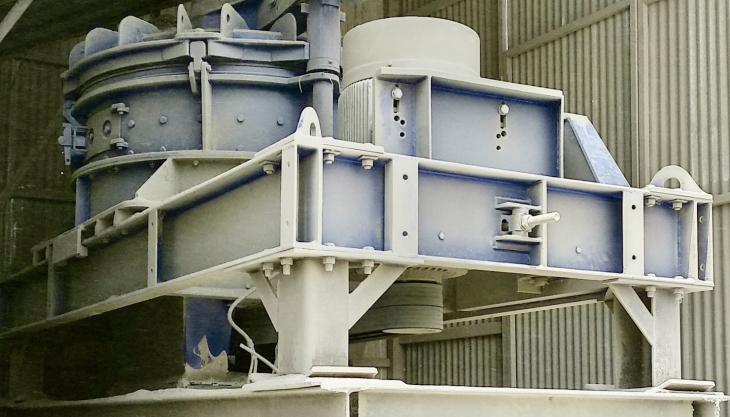
Indian sand manufacturer benefits from RPM 1513 rotor impact mill supplied by BHS-Sonthofen
SAND manufacturers Kasprs Build Mate inaugurated a new plant for processing off-spec particles in mid-2019. The centrepiece of the plant in Pune, India, is a rotor impact mill from BHS-Sonthofen, which, in contrast to conventional vertical-shaft impact (VSI) rotor crushers, is designed to further reduce fine grain sizes.
As a result, Kasprs can make use of off-spec material from other companies to produce high-quality plaster sand and dry mortar sand for the construction industry.
Sand production using conventional VSI rotor crushers, which are commonly used in India, produces large volumes of off-spec particles 10–15mm in size, which remain in the circuit without being crushed any further.
These off-spec particles, which can account for up to 35% of the total volume, are often backfilled, which is why Kasprs Build Mate were looking for a way to turn this surplus material into high-quality sand.
Himanshu Mavadiya, production applications manager at BHS India, identified the RPM 1513 rotor impact mill as the perfect tool for this task: ‘Our RPM 1513 delivers a targeted and very high crushing ratio, which has a consistent grading curve over the entire tool lifetime,’ he said.
‘It is, therefore, able to produce sand of the highest quality with an excellent particle shape from the surplus material of conventional rotor crushers. The producer benefits considerably from this and, in addition, every tonne of sand that can be produced from off-spec particles slows down the depletion of natural sand deposits.’
BHS-Sonthofen have a modern test centre where the material to be processed can be tested in advance in various machines.
‘In this particular case, we are dealing with basalt – a magmatic rock that presents some challenges,’ said Mr Mavadiya. ‘The BHS experts in Germany were able to carry out tests using a rock sample, allowing them to select the ideal machine and determine the best settings too.’
Not wanting to leave anything to chance in this project, Kasprs inspected the machine at the German manufacturing site. The goal was not only to find the right technology for the application, but also one that stood out from competing suppliers in the Indian region in terms of quality.
From the outset, the RPM 1513 rotor impact mill fulfilled all expectations. In total, several hundred thousand tonnes of high-quality sand have already been produced and Anup Karwa, project manager at Kasprs Build Mate, is well satisfied.
He said: ‘For our company, efficient value creation and thus resource savings is an enormously important decision factor when it comes to choosing new technology. BHS-Sonthofen convinced us on site with their modern test centre, experienced experts and robust high-performance machines.’
In the meantime, the sand produced by the BHS rotor impact mill has become a brand in its own right. ‘Customers have taken to calling this high-quality product Kasprs Sand,’ said Mr Karwa. ‘This name stands for an optimal, homogeneous particle shape, and despite its somewhat higher price, it has become a sought-after construction material, especially for ambitious projects.
‘In contrast to naturally occurring sand, which often has to be shipped over vast distances and is sometimes of dubious origin, this sand is also a local product: the basalt rock extracted in the vicinity of the plant has been made fully usable by BHS technology.’