Top-hammer drilling sees new interest in the UK
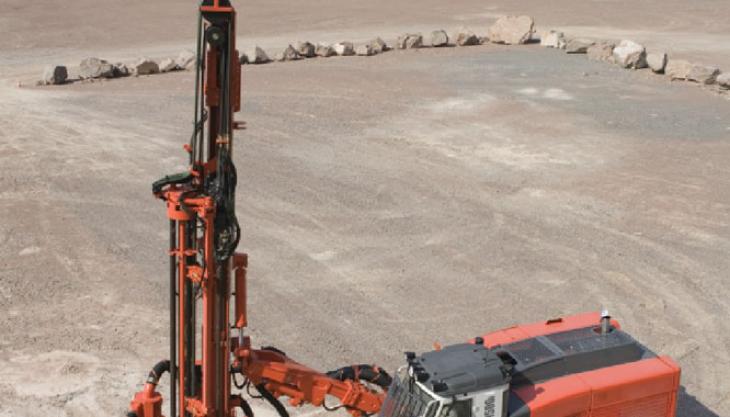
During the 1960s and 70s many UK quarries were littered with drilling tool scrap in the form of bent and broken extension rods, extracted after becoming stuck in the hole. At this time the majority of holes drilled by top hammer were between 89mm and 115mm in diameter. The small, 38mm diameter extension rods were soon exchanged for the DTH (down-the-hole) method, using tubes, hammers and bits.
The rest of Europe and Scandinavia continued with top-hammer drilling, mainly due to the smaller drill hole diameters of 64–92mm, and today this method of drilling still predominates on the continent, while DTH remains the preferred method in the UK.
However, the top-hammer drills manufactured by Sandvik today are far removed from the drills associated with the rigs of the 60s and 70s. Currently, over 450 Sandvik DP (Panteras) are operating worldwide with Sandvik GT60 drilling tools; Germany alone has over 70 units in operation.
And the company say they are definitely seeing a new interest in top-hammer drilling in the UK, with sales of these rigs slowly increasing as drilling contractors add them to their fleets. According to Sandvik, the reduction in bench heights and smaller hole diameters means the power and faster penetration rates of a top hammer drill can be fully utilized. And, they say, hole quality is now very good and fuel consumption is low.
Sandvik offer the DX (Ranger) for construction and small-to-medium-size quarries. This has a special rotating top structure for superior drilling coverage and extra stability in rough terrain, while the DP (Pantera) is available for high-production quarry applications.
Among the key changes to, and advantages of, Sandvik top-hammer drilling machines are:
- RockPilot drilling system that automatically adapts feed and percussion pressures to suit varying rock conditions on the basis of instantaneous penetration speed and rotation torque.
- Greatly improved drill steels offering longer life, straighter holes, fewer jammed drill steels and more production.
- High versatility; the same DP (Pantera) rig can drill 92mm, 96mm, 102mm, 115mm, 127mm, 140mm and 152mm holes.
- Reduced carbon footprint; typically a DTH drill will use 50–60 litres of fuel per hour, while a top-hammer drill will use only 25–35 litres per hour.
- Straight holes and long service life with 60mm diameter Sandvik GT60 extension rods.
- Fast penetration rates with Sandvik HL1000 and HL1560 rock drills.