Smaller carbon footprint for M6 link road
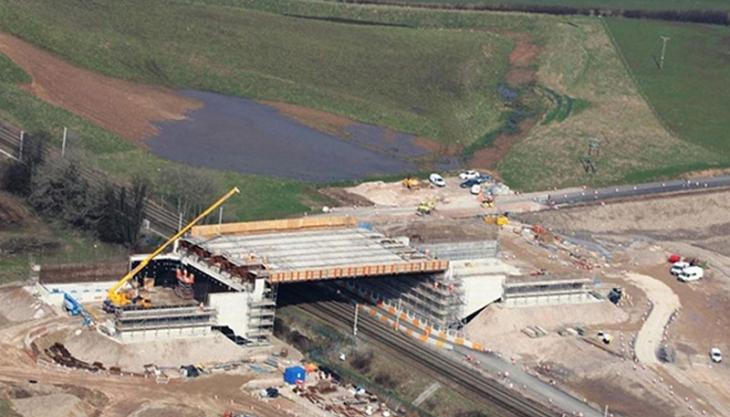
Lafarge Tarmac helping Costain reduce both carbon and costs on new motorway link in Lancashire
COSTAIN are working with supply chain partner Lafarge Tarmac to reduce the carbon footprint of the construction of the Heysham to M6 link road in Lancashire.
The project will connect Heysham and Morecambe to a new Junction 34 on the M6, and includes a 4.8km dual carriageway with a combined footway and cycleway along its entire route.
Lafarge Tarmac are supplying Costain with key materials such as aggregate, ready-mixed concrete and asphalt. They report their CO2e (CO2 equivalent) figures for all materials supplied to the project, with the aim of reducing their embodied carbon emissions by 20%.
Andrew Langley, Costain project director, said: ‘Both Costain and Lafarge Tarmac have identified climate change as a key feature of their sustainability strategies. This project is a great example of the benefits and cost savings that can be achieved.
‘As part of this contract, Lafarge Tarmac’s Sustainability Department provides us with a monthly ‘carbon tracking service’. This captures carbon data that shows both waste reduction and environmental benefits. It also shows the significant cost savings that result from reducing the carbon footprint of materials.
‘Additionally, getting our aggregates, concrete and asphalt in a single supply package means we have managed to ensure zero mineral wastage of produced materials. We have also benefitted from the supply quarry being located just five miles from the project, leading to further carbon- and cost-saving benefits.’
Early contractor involvement has been key to reducing the project’s carbon footprint, according to Nick Toy, business development manager at Lafarge Tarmac. ‘Through early engagement on the design and materials, the project team was able to identify considerable savings in the quantity of materials required and the embodied carbon footprint of the project,’ he explained.
‘The new design reduced the aggregate tonnage by nearly 25%, saving more than 200,000 tonnes of raw materials, and enabled a reduction of nearly 9,000 cubic metres of ready-mixed concrete – just over 26%.
‘This translates into a 21% saving of CO2e from the original design, with the largest carbon savings realized through the reduction in asphalts.’
The Costain team believes there is further scope to potentially lower the project’s carbon footprint and says it will be looking for additional opportunities for value engineering throughout the construction phase.