Single tower with two plants for Fröschl Beton
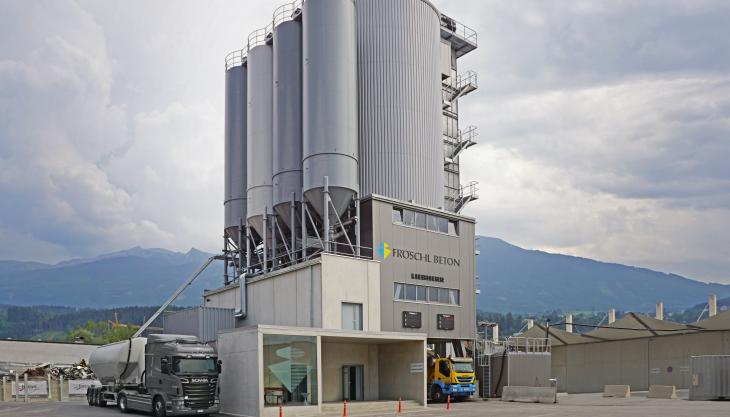
State-of-the-art concrete mixing tower from Liebherr covers entire concrete logistics chain
ONE of Austria’s most modern concrete mixing plants has been proving its worth since spring 2019. The Liebherr Betomat-type mixing tower was optimally adapted to suit customer requirements. With the new mixing tower, the Fröschl Beton company is ideally positioned for the future.
The Fröschl Beton company has been supplying construction sites in the Innsbruck area with ready-mixed concrete for many years, but their 45-year-old mixing plant was technically obsolete and no longer met the standards of today.
The requirements for the replacement purchase were high: it would have to cover the entire concrete logistics chain and deliver flawless concrete efficiently and flexibly, both today and in the future.
After an extensive planning phase, Liebherr’s Betomat concept was chosen because it allows the operation of two completely separate mixing plants within one mixing tower. Fröschl Beton found the compact design of the two weighing and mixing lines, as well as the Liebherr quality and service, compelling.
The Betomat holds up to 600 cubic metres of stone in nine silo chambers. The mixing tower is fed with aggregates via two charging hoppers and a powerful bucket elevator with an hourly output of 200 cubic metres per hour. The plant has seven silos for a binder supply of around 840 tonnes.
The new mixing plant is equipped with two mixer systems: a ring-pan mixer with agitator system and a double-shaft mixer. This means that normal standard concretes as well as high-performance and special concretes can be produced very efficiently. When in operation with both mixer systems, the plant can achieve an output of around 160 cubic metres of compacted fresh concrete per hour.
The tower is equipped with two lanes. Thanks to the separate weighing lines, two vehicles can be loaded simultaneously with different types of concrete, making the mixing plant highly efficient and flexible.
For environmentally friendly operation, the housing and exhaust air-filter systems reduce noise and dust emissions, whilst residual concrete from the truckmixers and plant cleaning are processed in an LRS 908 residual concrete recycling plant. Washed-out material and residual water can be returned to concrete production. This enables considerable cost and material savings.
To ensure smooth operation even during the cold winter months, the entire plant is protected with a 100mm insulated wall and equipped with heating.