Schenck Process UK move aftermarket services to new location
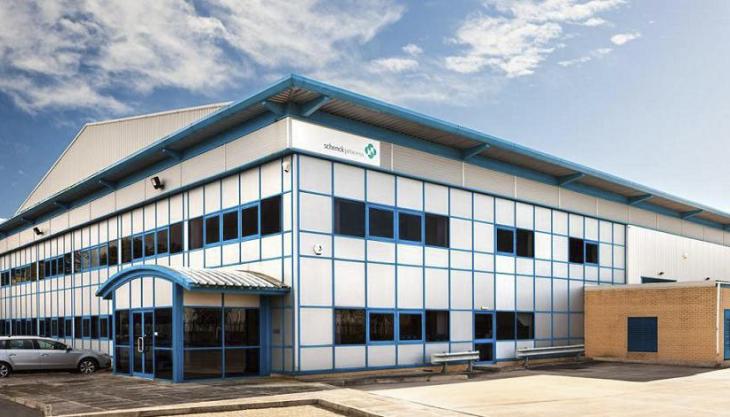
At the beginning of March 2013 all of the aftermarket service and sales personnel for Schenck Process UK moved into new premises in Thorne near Doncaster. The re-location is part of a £1.5m expansion programme the company is carrying out to move the factory and test centre into a new 56,000ft2 building.
Schenck Process UK incorporates the Clyde Process, Redler and Schenck Process products and technologies and also supports the supply of spare parts and replacement machines for a wide number of other brands such as Vac-U-Max, Simon Macawber, Stock and Clyde Materials Handling.
The new offices and factory provides an opportunity to centralize the customer contact point for the aftermarket operation with a low-cost 0845 telephone number and a comprehensive out-of-hours support team. Stocks of spare parts will also be centralized to give improved lead times to UK and international customers.
Tim Carter, director of aftermarket services, commented: ‘Having all customer support staff in one location will increase the level of services that we can offer, give greater efficiencies and one point of contact which we know our customers will value.’
The aftermarket department has a total of 38 UK-based staff including 18 service and commissioning engineers and 12 proposal and customer support staff. All personnel have undergone intensive training on the company’s full range of products and technologies to identify and resolve issues that occur during the working life of the equipment.
The company offers a full aftercare programme called PASS (Process Advanced Service System). The programme covers product installation, routine inspections, maintenance programmes, on-site spare stock monitoring and the repair, upgrade and replacement of parts. All of these services will be co-ordinated by the new central office which can be reached on 0845 201 4564 or by e-mail at spares@schenckprocess.co.uk