Ruttle Plant purchase two Bell wheel loaders
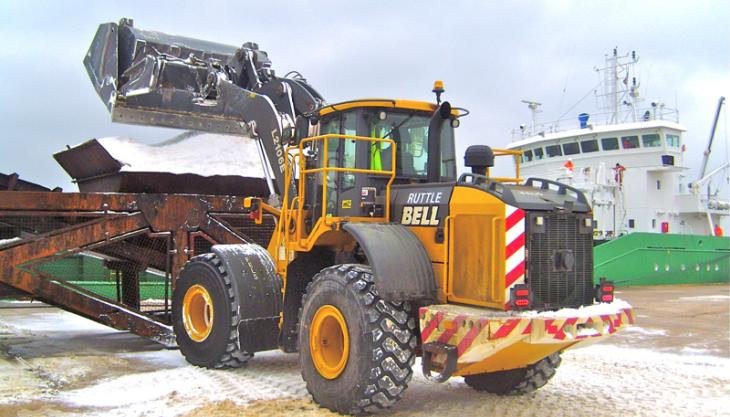
Specially modified 2106 wheel loaders being used for ‘toughest ever application’ at salt works
RUTTLE Plant have purchased two wheel loaders from Bell Equipment, for use at a salt works in what Bell are calling the ‘toughest ever application’ for the machines.
Extensive modifications have been made to ensure that the 2106 loaders are able to withstand the rigours of working with salt, which is notorious for its aggressive and corrosive effects on machinery.
Although Ruttle Group have been buying articulated dumptrucks from Bell Equipment for more than a decade, this deal represents a significant first, being the first time that Ruttle have purchased Bell wheel loaders.
When a boat arrives at the salt works, the loaders are required to move the salt from the sheds where it is stockpiled and load it into hoppers, from which it is conveyed on to the boat.
The boat schedule is subject to time restrictions, requiring a swift and reliable loading operation to prevent the customer from being charged for demurrage for going over the time allowed.
After trialling a number of machines, Bell and Ruttle decided that the 2106 – fitted with a 4.2 cubic metre capacity high-tip bucket – presented the optimum solution. Each machine can load six tonnes per bucket.
A more significant discovery, however, was just how rapidly salt began to affect the performance of the loaders. During the trial, the demo machine was caked in salt and checking existing machinery on site confirmed the high level of corrosion.
As a result, Bell engineers devised an extensive series of modifications to make the new loaders fit for purpose.
‘Salt is horrendously aggressive, and these machines need to withstand a lot,’ explained Carl Woollaston, sales support manager at Bell Equipment.
Each loader has been supplied with an autogreaser with stainless steel fittings that pumps grease into the pivots to keep them working.
Bell also went through the whole machine methodically, spraying any component that might be susceptible to salt damage with a protective wax – ‘literally every nut and bolt,’ confirmed Mr Woollaston.
While the John Deere engine already benefits from fully sealed electrics, Bell took no chances, adding a protective wax over all engine and transmission control units that are located within the operator cab.
Other components required a more bespoke treatment. Alternators were sent to a specialist in underwater machines to be ‘marinised’, while the entire cooling pack was removed, including all radiators, coolers and air-conditioning units, and supplied to another specialist who sprayed the components with an appropriate anti-corrosion paint.
Once all of these modifications had been completed, Bell put the loaders back together – after which they were sprayed with three coats of rust-protection lacquer, Dinitrol.
Ensuring that the loaders were ready to be used on site was only the beginning. Ruttle Group have experienced downtime with other equipment at the salt works and were determined to avoid the same problems with the Bell machines.
‘Our first request to Bell was: ‘tell us what to do to keep the loaders in good working order’, and they have been fantastic in devising a strict maintenance regime,’ said Gareth Ruttle.
Bell Equipment have provided detailed instructions on what to do immediately after a shift, including a high-volume, low-pressure wash-down in place of the customary steam clean, which would not be appropriate in this situation because it would remove the wax protection.
In addition, because the loaders are not in use in between the arrival of each boat, Bell have advised Ruttle to grease the pivot points on the bucket before and after each shift.
Finally, Bell have tasked Ruttle with completing a respray using Dinitrol every two weeks.
‘We cannot risk our reliability being compromised, and Bell Equipment have gone out of their way to ensure that the loaders are ready to load each new boat,’ said Mr Ruttle. ‘Both loaders are performing exceptionally well so far – testament to the precautions that have been taken to protect them from the rigorous conditions at the salt works.’