RockFuel unveil pioneering carbon-negative cement process
Unprecedented climate-positive cement-making process said to be better than net zero
ROCKFUEL, an innovator in true net-zero energy and industrial processes, have unveiled their pioneering and climate-positive carbon-negative cement process. Described as a pivotal breakthrough in decarbonizing the cement, lime, and concrete industries, the process is said to offer a scalable, planet-positive alternative to traditional cement production, a sector responsible for an estimated 8% of carbon dioxide (CO2) emissions globally.
At the heart of RockFuel’s innovation is their patented RockFuel carbon-neutral lime kiln, a cutting-edge closed-loop system that efficiently produces quicklime (calcium oxide) while capturing CO2 emissions. The kiln operates on renewable energy sources, ensuring sustainability throughout the process. It works by heating limestone to produce quicklime while collecting and storing more than 500m3 of hot CO2 per cubic metre of rock in a dedicated tank. The kiln continuously processes limestone with a proprietary design that retains heat and maximizes efficiency.
The captured CO2 is repurposed within RockFuel’s carbon-negative cement production process, offering an unprecedented eco-friendly alternative to conventional cement manufacturing.
Unlike traditional cement production, which emits large amounts of CO2, RockFuel’s process is designed to be inherently carbon neutral. However, once the cement is used in construction and cures, it actively absorbs CO2, making the entire process carbon negative. This game-changing approach not only reduces the environmental impact of cement production, but also provides a long-term solution for CO2 absorption in infrastructure projects.
The production process begins with limestone extraction, which is then heated in RockFuel’s kiln, using renewable energy sources such as solar, wind, nuclear, hydroelectric power, or carbon-neutral power and energy from other RockFuel processes. The quicklime (CaO) produced is then mixed with clay to form cement. Meanwhile, the CO2 released during the heating phase is processed in an electrolysis plant, powered by excess energy from the process, yielding carbon-neutral oxygen and solid carbon – valuable by-products with applications in steel production, medical procdures, the chemical industry, waste water treatment (for oxygen), and high-tech industries, including carbon-fibre and graphene production (for solid carbon).
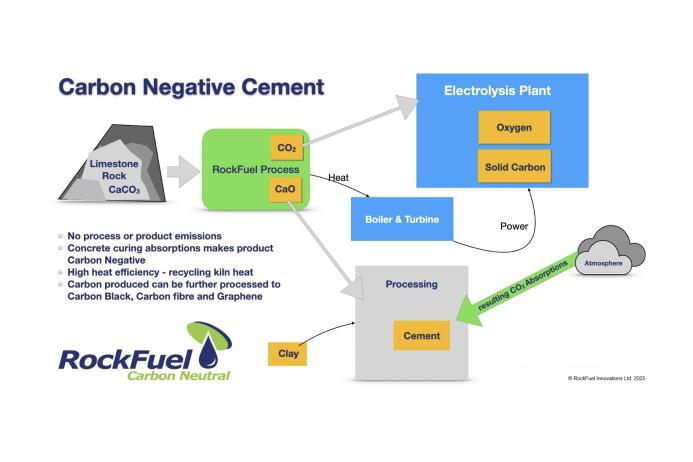
With the global cement industry projected to grow from US$316.3 billion in 2020 to US$463.0 billion by 2026, the demand for sustainable and eco-friendly cement alternatives is increasing. The Asia-Pacific region remains the largest market, while Europe and North America continue to drive innovation in sustainable construction materials, but cement is still a very significant net contributor of CO2 emissions. In the UK alone, the cement industry plays a crucial role in infrastructure development but faces increasing pressure to reduce its carbon footprint.
RockFuel say their carbon-negative cement presents a compelling solution for the industry’s CO2 emission challenges, offering a proven and viable alternative to traditional methods that aligns with global Net Zero carbon ambitions and the UK Government’s ‘Net Zero Strategy: Build Back Greener’ objectives.
A potential use case is in the implementation of the UK’s ‘Clean Power 2030 Action Plan’ that has led to the erection of wind farms at pace. Use of RockFuel’s carbon-negative cement would dramatically and positively impact the total CO2 emission savings in the construction of future wind farms. The 650 to 1,000 tonnes of concrete foundation required for each wind turbine could use RockFuel’s carbon-negative cement, rather than traditional CO2-emitting cement – transforming these admirable Net Zero initiatives, along with other concrete infrastructure and built environment projects, into supercharged climate-positive contributors.
RockFuel say their carbon-negative cement process can be adopted by lime, cement and concrete producers to transform their ESG credentials and cement decarbonization objectives. The resultant chemistry of the cement is unchanged and will transform the construction of buildings, infrastructure, roads and bridges into one of the most eco-friendly and versatile building materials available – whether it is used in poured concrete or precast concrete products. Where cement is increasingly perceived as a questionable building material in our current climate crisis, this innovation transforms the cement industry into a climate-positive building material, sustaining its ubiquitous use.
RockFuel’s innovative approach has been validated through independent chemical engineering assessments, and the technology has already demonstrated profitability through financial modelling, showcasing its potential for widespread industrial adoption. Moreover, RockFuel hold multiple UK and international patents, with further patents pending, solidifying their leadership in sustainable industrial innovation.
According to RockFuel, their carbon-negative cement process marks a paradigm shift for the cement industry, proving that large-scale industrial processes can be both economically viable and environmentally responsible. And as governments and businesses intensify their commitment to carbon neutrality, it seems that the company is set to play a pivotal role in the future of sustainable construction.