Recycling railways in the Netherlands
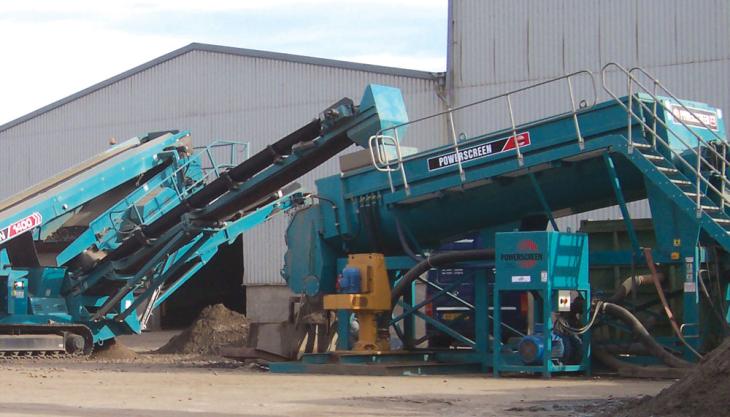
Railway ballast that has lost its geotechnical properties and is no longer able to fully support the rail track or provide adequate drainage has to be renewed. However, rather than sending the old ballast to landfill, much of this spent material can be turned into valuable recycled products by an effective washing and screening process.
Dutch firm Joroen van der Bos Railway Ballast Recycling are doing just that using a range of Powerscreen equipment to clean discarded material so that the majority can be reused, with some of the recycled aggregate going full circle for reuse as railway ballast, while other end products are used in concrete production.
On arrival by rail wagon at the company’s processing yard at the Port of Rotterdam, the used material is first screened into three sizes by a Powerscreen Chieftain 1400. This dry screen takes out any +63mm oversize and, at the same time, removes the majority of –4mm material, which is referred to as Category 1 soil.
This 0–4mm soil is usually contaminated with diesel oil and other hydrocarbons but can be used along the edges of motorways and other busy roads to create sound barriers that help divert traffic noise away from built-up areas. The soil is carefully laid on to plastic to prevent any leaching of the hydrocarbons, and the material location is fully documented and recorded so that it can be treated appropriately in the future.
Meanwhile, the –63mm +4mm material from the Chieftain 1400 is fed directly to a Powerscrub 120 attrition-washing unit, which mixes and scrubs the material to break up any clay conglomerations while removing any fines and allowing light organic matter to float off with the process water.
The remaining coarser material from the Powerscrub 120 is fed on to a 3.5m x 1.5m twin-deck rising screen fitted with a 35mm top deck screen mesh and 4mm bottom deck screen mesh. This unit removes any unwanted –4mm material and produces a washed –63mm +36mm product and washed –36mm +4mm material. The latter is of such quality that it can be used in the concrete industry, while the former completes a full circle and is reused as railway ballast.
Waste water from the Powerscrub 120 and –4mm material from the rinsing screen are fed to a Powerscreen Finesmaster 60 sand plant, which uses hydrocyclone technology to clean and recover any saleable product larger than 63 microns. The recovered material is discharged on to a high-frequency dewatering screen to produce a washed –4mm +63 micron sand with a moisture content of around 12%.
Water used in the washing plant is fed to an on-site water-management system to remove the silts, clays and organic matter. Once clean, the water is re-circulated and pumped back to the plant, so that only a small amount of top-up water is needed to keep the system working.
Powerscreen International, 200 Coalisland Road, Dungannon, Co. Tyrone BT71 4DR; tel: (028) 8774 0701; fax: (028) 8774 7231
Dutch firm Joroen van der Bos Railway Ballast Recycling are doing just that using a range of Powerscreen equipment to clean discarded material so that the majority can be reused, with some of the recycled aggregate going full circle for reuse as railway ballast, while other end products are used in concrete production.
On arrival by rail wagon at the company’s processing yard at the Port of Rotterdam, the used material is first screened into three sizes by a Powerscreen Chieftain 1400. This dry screen takes out any +63mm oversize and, at the same time, removes the majority of –4mm material, which is referred to as Category 1 soil.
This 0–4mm soil is usually contaminated with diesel oil and other hydrocarbons but can be used along the edges of motorways and other busy roads to create sound barriers that help divert traffic noise away from built-up areas. The soil is carefully laid on to plastic to prevent any leaching of the hydrocarbons, and the material location is fully documented and recorded so that it can be treated appropriately in the future.
Meanwhile, the –63mm +4mm material from the Chieftain 1400 is fed directly to a Powerscrub 120 attrition-washing unit, which mixes and scrubs the material to break up any clay conglomerations while removing any fines and allowing light organic matter to float off with the process water.
The remaining coarser material from the Powerscrub 120 is fed on to a 3.5m x 1.5m twin-deck rising screen fitted with a 35mm top deck screen mesh and 4mm bottom deck screen mesh. This unit removes any unwanted –4mm material and produces a washed –63mm +36mm product and washed –36mm +4mm material. The latter is of such quality that it can be used in the concrete industry, while the former completes a full circle and is reused as railway ballast.
Waste water from the Powerscrub 120 and –4mm material from the rinsing screen are fed to a Powerscreen Finesmaster 60 sand plant, which uses hydrocyclone technology to clean and recover any saleable product larger than 63 microns. The recovered material is discharged on to a high-frequency dewatering screen to produce a washed –4mm +63 micron sand with a moisture content of around 12%.
Water used in the washing plant is fed to an on-site water-management system to remove the silts, clays and organic matter. Once clean, the water is re-circulated and pumped back to the plant, so that only a small amount of top-up water is needed to keep the system working.
Powerscreen International, 200 Coalisland Road, Dungannon, Co. Tyrone BT71 4DR; tel: (028) 8774 0701; fax: (028) 8774 7231