Powerscreen to launch four new machines at Hillhead 2014
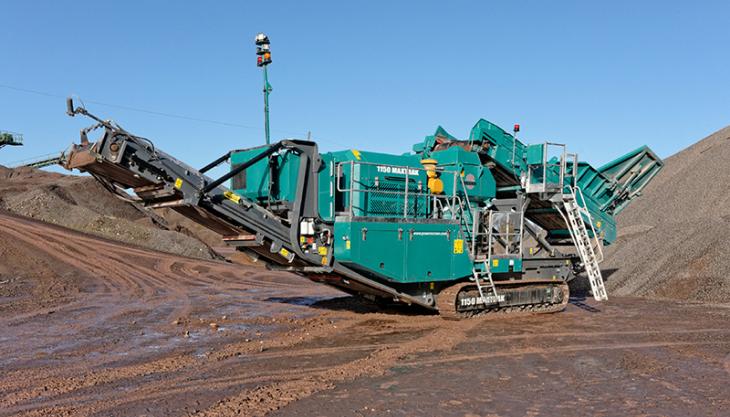
Two new jaw crushers, including a diesel-electric version, a new cone crusher and a new screen
POWERSCREEN, one of the world’s leading providers of mobile crushing and screening equipment, will be unveiling the latest in a series of new products at Hillhead 2014. Visitors to the demonstration area will see four new machines in action – a Powerscreen Premiertrak 300 HA jaw crusher and Powerscreen Warrior 2100 screen will both be working independently, while a Powerscreen Premiertrak 600 diesel-electric jaw crusher will be feeding a Powerscreen Maxtrak 1150 cone crusher.
The Premiertrak 300 jaw crusher features a vibrating grizzly feeder (VGF) set with 50mm bofor bar on the top deck and 30mm mesh on the bottom, and a new hydrostatic drive system option that allows it to reverse and unblock or run continuously in reverse for asphalt applications. Designed to run at low engine rev/min, it offers a high level of fuel efficiency and low noise emissions.
Benefits of the Premiertrak 300 include: a closed-side setting (CSS) that can be set to 40mm while running in both asphalt and recycled concrete applications; large clearances in the bypass chute to improve material flow and reduce the chance of blockages in sticky material; a large under crusher clearance and full tunnelling to reduce the chance of blockage due to re-bar build up; and a hydraulically lowering conveyor that offers convenient access to reduce downtime should a blockage occur.
Rapid set-up times are possible with all folding done hydraulically without the need to work at height, while control is via an easy to use PLC screen control system. Jaw speed and CSS can be changed by a single button which allows the machine to be adjusted to suit the application quickly with no tools required. The Premiertrak 300 crusher is also available with a hydraulic release jaw chamber for difficult recycling applications where additional protection from tramp metal is required. Additional versatility is offered with the lock-off system which configures the HR jaw chamber to operate as a standard HA unit which will not dump.
The Warrior 2100 screen includes Powerscreen’s proven triple-shaft technology, first developed for the successful Warrior 2400 model. This technology, unique to Powerscreen heavy-duty mobile screens, ensures that the 16ft x 5ft screenbox is highly effective and efficient while maintaining exceptional throughput productivity.
The extreme screening acceleration offers the Warrior 2100 screen improved capabilities over its class rivals, especially in sticky scalping applications. With amplitudes and accelerations in excess of 16mm and 6g, respectively, the Warrior 2100 triple-shaft screen is said to outperform conventional screens in a multitude of applications, including aggregates, overburden, processed ores, topsoil, compost, C&D waste, C&I waste, foundry waste and biomass.
The new Premiertrak 600 jaw crusher comes to market in two possible configurations: diesel-hydraulic and diesel-electric. Both versions are designed to deliver maximum production and performance with minimum downtime and running costs. The diesel-electric machine can be powered directly from an on-site source, which further reduces the cost of operation.
At the heart of the Premiertrak 600 crusher is a modern 1,200mm x 820mm jaw chamber incorporating robust construction with many user-friendly features, including a fully hydraulic CSS range of 75–200mm and a reversing system to clear blockages quickly for increased uptime. The crusher’s aggressive stroke and high-inertia flywheels are said to provide high production rates and excellent reduction ratios. With speed and safety in mind, the Premiertrak 600 crusher can be fully set-up from ground level thanks to its hydraulically folding and locking hopper system, in combination with a hydraulically lowering product conveyor.
Targeted at quarry operators and contractors alike, the mid-sized Maxtrak 1150 mobile cone crusher builds upon the success of the Maxtrak 1000 and 1300 models to offer optimum performance, production and versatility. The crushing action of the Maxtrak 1150 model delivers the same product shaping for which the other Powerscreen cones have become renowned around the world.
The machine will be offered in two key configurations: a direct-feed model and a pre-screen version, which will allow customers to handle dirty feed material and achieve higher production rates. With a choice of strokes and four liner options, all of which are compatible with a single upper frame, the Maxtrak 1150 cone crusher can be easily configured for all applications.
Feed sizes of up to 205mm are possible into the 225kW cone chamber which is directly driven by a fuel-efficient 331kW Scania DC13 engine that complies with the latest Stage IV emission regulations. A key feature of the pre-screen model is its patented hydraulic folding system for converting the machine into a direct feed layout in minutes, delivering unmatched flexibility to the end-user.
Meanwhile, on static display on the main Powerscreen stand will an array of existing and newly released products, including: a Powerscreen 1000 Maxtrak cone crusher; a Powerscreen Premiertrak 300 HR jaw crusher; a Powerscreen Powertrak 750 scalping screen; a Powerscreen Chieftain 2100X screen, specially modified for the biomass market; and a Powerscreen Trakpactor 320SR impactor.