Powerscreen and Flex-Mat help recycle road base
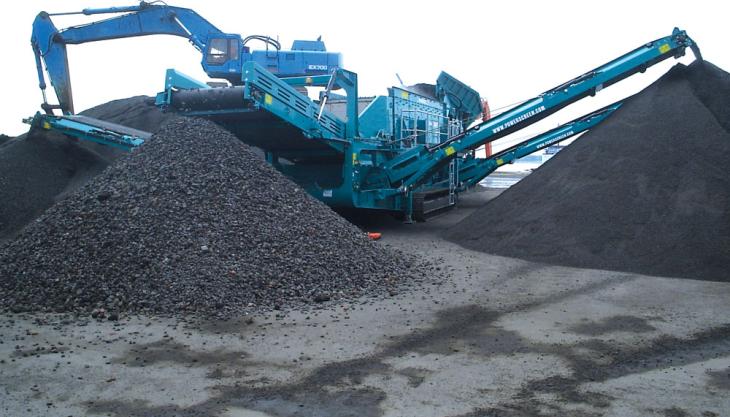
Dutch firm Van Bentum Recycling Combinatie are using a Powerscreen H6203 with Flex-Mat 3 screen media to separate recycled asphalt, which has been cleaned of tar, for reuse as road base.
The site manager at Rotterdam-based Van Bentum Recycling Combinatie said: ‘We’re very pleased with the Powerscreen H6203 as it has such good capacity and speed. The Flex-Mat 3 screen media manufactured by Major Wire Industries is a great addition, as throughput is extremely good and blinding and pegging is minimal. Also, the Flex-Mat 3 screen media does not need to be changed as often, so not only is the process more efficient and profitable for us, it is more economical to run.’
The recycled asphalt is first burned by Van Bentum’s thermal cleaning facility to remove the tar before being processed by the Powerscreen H6203, which has three screen media producing four end-products at approximately 300 tonnes/h. The top deck of the machine comprises 30mm x 30mm square woven mesh, the middle deck is 9mm Flex-Mat D-Series and the bottom deck is 3mm Flex-Mat S-Series. This produces clean 0–3mm, 3–9mm, 9–30mm and 30mm+ oversize asphalt suitable for reuse.
The Powerscreen H6203 is designed for large-volume processing of crushed stone, sand and gravel, coal, recycled concrete, asphalt etc, and is capable of producing up to 800 tonnes/h of four specific-sized products. It features a high-productivity 6.0m x 1.83m horizontal triple-deck, geared triple-shaft oval-stroke screen.
Weighing 48 tonnes, the H6203 is Powerscreen’s top-of-the-range model, measuring 18.55m in length and 4.75m in height in working mode. Its four attached stockpiling conveyors, which are all angle-adjustable and feature infinitely variable belt speed control, fold hydraulically for transportation, giving the machine a travelling width of only 3.2m. The feed conveyor also has variable-speed control for optimum material feed performance. On site set-up time is typically around 1h, with the low-ground-pressure, heavy-duty crawler undercarriage providing a high degree of mobility around the job site for a machine of its size.
Since it was introduced, the Flex-Mat 3 high-performance, self-cleaning screen media has been used in more than 12,000 applications around the world and is said to have increased production by 20–40% in applications prone to blinding and pegging, compared with woven wire, square or slotted cloth.
Polyurethane strips centred on each screen deck crown bar support allow individual wires to vibrate independently at different frequencies, preventing material from accumulating between the wires. Flex-Mat 3 also has up to one-third more open area per screen and is said to last up to three times longer than woven wire.
Four configurations of Flex-Mat 3 are available: Series D (diamond pattern), for precise sizing of passing material and most standard applications; Series S (wave pattern), for the removal of fines to produce a cleaner retained product; Series T (triangular pattern), larger sizes reinforced for heavy loads or high-impact materials; and Series T (triangular pattern) for fine screening from 30 to 8 mesh. The D and S Series configurations are used in Van Bentum Recycling Combinatie’s application.
The site manager at Rotterdam-based Van Bentum Recycling Combinatie said: ‘We’re very pleased with the Powerscreen H6203 as it has such good capacity and speed. The Flex-Mat 3 screen media manufactured by Major Wire Industries is a great addition, as throughput is extremely good and blinding and pegging is minimal. Also, the Flex-Mat 3 screen media does not need to be changed as often, so not only is the process more efficient and profitable for us, it is more economical to run.’
The recycled asphalt is first burned by Van Bentum’s thermal cleaning facility to remove the tar before being processed by the Powerscreen H6203, which has three screen media producing four end-products at approximately 300 tonnes/h. The top deck of the machine comprises 30mm x 30mm square woven mesh, the middle deck is 9mm Flex-Mat D-Series and the bottom deck is 3mm Flex-Mat S-Series. This produces clean 0–3mm, 3–9mm, 9–30mm and 30mm+ oversize asphalt suitable for reuse.
The Powerscreen H6203 is designed for large-volume processing of crushed stone, sand and gravel, coal, recycled concrete, asphalt etc, and is capable of producing up to 800 tonnes/h of four specific-sized products. It features a high-productivity 6.0m x 1.83m horizontal triple-deck, geared triple-shaft oval-stroke screen.
Weighing 48 tonnes, the H6203 is Powerscreen’s top-of-the-range model, measuring 18.55m in length and 4.75m in height in working mode. Its four attached stockpiling conveyors, which are all angle-adjustable and feature infinitely variable belt speed control, fold hydraulically for transportation, giving the machine a travelling width of only 3.2m. The feed conveyor also has variable-speed control for optimum material feed performance. On site set-up time is typically around 1h, with the low-ground-pressure, heavy-duty crawler undercarriage providing a high degree of mobility around the job site for a machine of its size.
Since it was introduced, the Flex-Mat 3 high-performance, self-cleaning screen media has been used in more than 12,000 applications around the world and is said to have increased production by 20–40% in applications prone to blinding and pegging, compared with woven wire, square or slotted cloth.
Polyurethane strips centred on each screen deck crown bar support allow individual wires to vibrate independently at different frequencies, preventing material from accumulating between the wires. Flex-Mat 3 also has up to one-third more open area per screen and is said to last up to three times longer than woven wire.
Four configurations of Flex-Mat 3 are available: Series D (diamond pattern), for precise sizing of passing material and most standard applications; Series S (wave pattern), for the removal of fines to produce a cleaner retained product; Series T (triangular pattern), larger sizes reinforced for heavy loads or high-impact materials; and Series T (triangular pattern) for fine screening from 30 to 8 mesh. The D and S Series configurations are used in Van Bentum Recycling Combinatie’s application.