Performance and sustainability go hand in hand
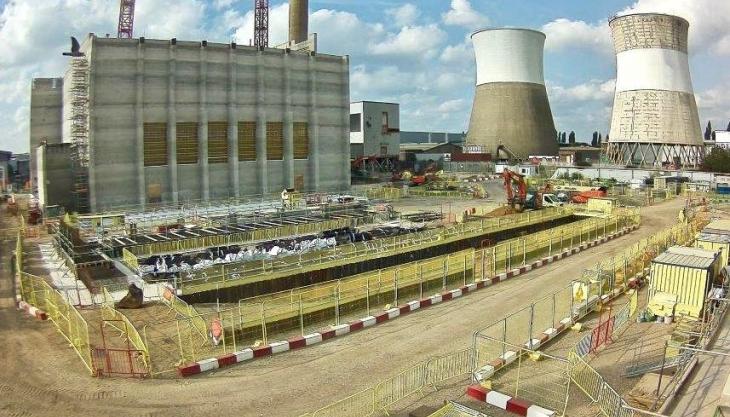
London Concrete supply seven-day continuous slipform pour with ECOPact Prime low-carbon concrete
LONDON Concrete, part of Aggregate Industries, have successfully completed a week-long continuous slipform pour after delivering 3,300 cubic metres of ECOPact low-carbon concrete over seven days for SSE and joint-venture partner CIP, for a new energy-from-waste (EfW) project, Slough Multifuel.
Together with principal contractor Hitachi Zosen Inova and specialist civils contractor Careys, work on the construction of the new £400 million EfW facility, located within Slough Trading Estate, began earlier this year and the facility will be fully operational by 2024.
It will provide a more sustainable waste-management solution for the Greater London area by processing 480,000 tonnes of residual waste per annum and will contribute to the UK Government’s strategy to reduce landfill and the export of waste.
By utilizing residual waste as a renewable energy source, Slough Multifuel will offset more than 147,000 tonnes of CO2 per year and power more than 100,000 homes. Moreover, the project is bringing hundreds of local jobs to the area during construction and will create around 50 permanent jobs in the operational phase.
Construction of the main waste bunker at the new facility commenced earlier this year, with London Concrete brought in to assist Careys and GB Slipform in the delivery of a 24/7 concrete supply. Aggregate Industries’ ECOPact Prime low-carbon concrete was specified to deliver the workability performance needed for a slipform of this size, whilst meeting the challenge set to reduce the concrete’s embodied carbon.
A decision was made early in the process to adopt slipform to help significantly reduce the amount of construction joints in the walls of the waste bunker and ensure a completely watertight structure. It was also essential to make the bunker resistant to chemical attack, and therefore the concrete needed to be DC-3 class compliant.
However, the immense size of the bunker posed a significant challenge, taking seven days and nights to complete. Furthermore, the use of ECOPact Prime – an engineered low-carbon concrete that utilizes higher blends of cement substitutes such as GGBS – presented challenges for slipforming when it came to setting times and compressive strengths.
Jamie Hamill, contracts manager at Careys, explained: ‘We needed to carry out a number of samples of the different types of concrete mixes to make sure we got the right consistency and strength gain.
‘We knew if the concrete went off too quickly in the shutter, then there would be little time to pour it correctly, there would be risks of blockages in the pumps, the rig would need to slide quicker to keep up, and everyone would come under increasing pressure to work faster. This, we knew, would risk a poor finish, or the quality being jeopardized.
‘On a big slide like this, you need to be slow and steady, so that you are always under control. The flipside is, however, if the concrete takes too long to go off, it is difficult to speed it up, which has a knock-on effect on the project time and cost.
‘Getting the concrete right is not an exact science as there are lots of different factors that can affect its strength, hence why testing samples in a relative sample size to determine how quickly we wanted the concrete to set was so important on this project. We did this over a few weeks, and we got the correct strength.’
Daniel King, managing director of London Concrete, added: ‘The project brief was certainly interesting – an eight-day continuous pour using a low-carbon concrete that, by design, with its high GGBS content, is not typically used in slipform construction.
‘However, trials carried out over a two-week period at our Heathrow plant, followed by frequent batch testing and 24/7 supervision during the pour, ensured we could supply a mix design that was optimized for performance, whilst also maintaining the sustainability credentials of the build through the use of a low-carbon concrete.
‘Overall, we were able to deliver a total carbon reduction of 42%, a saving of 608,951kg or 609 tonnes of eCO2 in comparison with a standard slipform mix.’