NSK solve bearing problem and reduce costs
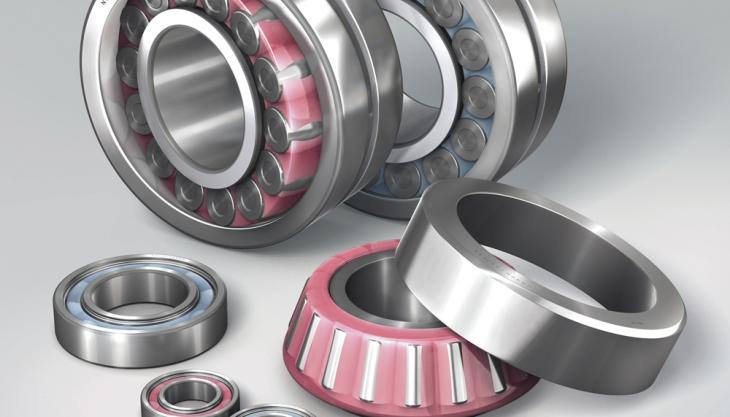
AIP cost-reduction programme delivers significant annual savings on operation of overhead conveyor
NSK’s Asset Improvement Programme (AIP) has achieved a major success with a large quarrying company, delivering annual cost savings of more than €14,000 per year having solved an ongoing bearing reliability problem on an overhead conveyor by replacing the existing bearing inserts with NSK’s Molded Oil bearings.
The problem with the conveyor was regular failure of bearing inserts every two months, or approximately 440h of operation. These failures were due to the harsh environment where the inserts were exposed to ingress from water and abrasive particles.
In addition, the bearings were assembled 5m above ground, making inspection, maintenance and the possibility of predicting premature failure especially difficult.
While the annual cost for replacing the bearings themselves was not too onerous, at €540, this figure was dwarfed by the €15,750 annual cost for the downtime resulting from the bearing failures. Clearly, this total annual cost of €16,290 was unsustainable, so an initiative was launched with a view to sourcing higher performance bearings.
As part of this initiative, engineers from NSK’s AIP cost-reduction programme were called in to give advice. The engineers visited the quarry, inspected the overhead conveyor and identified the problem. They suggested a solution using NSK’s Molded Oil Bearings, which they were certain would prolong bearing life.
Molded Oil bearings employ a special solid lubricant to transform the performance of machinery in environments exposed to high humidity, corrosion and contamination. The solid lubricant technology also means that there is no need for refilling of lubricant, as Molded Oil provides a continuous supply of lubricating oil.
Molded-Oil bearing inserts were fitted to the conveyor and have subsequently provided significantly extended bearing life. The bearings have already exceeded the life of the previous bearing inserts by a factor of nine, delivering 19 months of trouble-free operation (4,140h).
The resultant savings from this improved operation are considerable. With less than one replacement a year, maintenance cost is just €63 and downtime cost €1,838, giving a total cost per year of €1,901. This represents an annual saving of €14,389 as a result of replacing the existing conveyor bearings with the Molded Oil units.