New TwinAir sets record air flow for mining sector
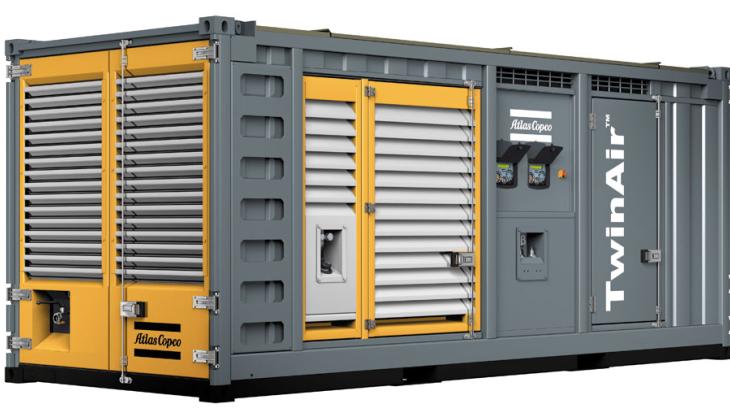
Atlas Copco say their new TwinAir range of air compressors has been designed to meet the high demand for greater-capacity compressors and enhanced productivity in mine and large open-pit drilling applications. Models in the range feature two operationally independent compressors with interconnected air manifolds housed within a standard 20ft ISO container, providing a robust, energy-efficient and safety-enhanced air supply at medium and high pressures.
According to Atlas Copco, the package delivers the highest volume of compressed air available with the smallest footprint. The model XAH 1066 (XAH 2250 CD6) provides a total free air delivery (f.a.d.) of 1,058 litres/s (2,232ft3/min) at a working pressure of 12 bar (175 lb/in2), while the XRV 946 (XRV 2000 CD6) delivers a f.a.d. of 936 litres/s (1,975ft3/min) at a working pressure of 25 bar (365 lb/in2).
Designed for fast installation and minimal set-up times on site, the units are also easily and legally transportable as container cargo, resulting in reduced transportation costs. The containerized units feature fork-lift slots and lifting eyes for loading on to flat-bed trucks for ease of mobility on site etc. TwinAir compressors can also be stacked up to three units high for storage or if operational space is restricted.
Air outlets are fitted at both ends of the container, together with a large grating for efficient air intake. A double ceiling within the container provides separation of the cold intake air channel and hot air outlet, thereby improving ambient condition performance. High-specification paint finishes make the units well suited to harsh environments, while stainless steel door locks and hinges provide additional corrosion resistance and security.
Prime power is provided by two Caterpillar C13 Acert, six-cylinder in-line diesel engines, each rated at 328kW (440hp), to provide a combined total of 656kW (880hp) at 1,600 rev/min. The engines meet Stage 3A (EU)/Tier III (EPA) legislation, while independent access controls for both engines allow a single compressor to be used for half the maximum flow, if required. Fuel coolers are fitted as standard, increasing the fuel efficiency and performance of the engines, while over-speed protection/intake shutdown controls prevent engine overruns. Three standard emergency stop buttons are provided to disable both power plants.
With a combined capacity of 1,800 litres (396gal), the fuel tanks are sufficient to keep the TwinAir unit operating at full load for up to 9h. All models are fitted with a quick-coupling connection for linking to an external fuel tank for continuous operation.
Large service doors provide easy access for walk-in servicing and maintenance, and a built-in ladder system provides access to the roof. A self-powered internal lighting system allows service operations to take place around the clock.
All components are positioned for ease of access, while centrally located drains for the compressor element, air receiver, engine coolant etc ensure fast and easy drainage at the recommended intervals. Spillage-free skid-frames protect the environment from inadvertent spills. Air filters are service friendly for disassembly and reassembly, with separate circuits for the engine and compressor air inlets and a safety cartridge fitted as standard.
The container also houses storage space for spare parts and small tools, and a convenient maintenance kit provides the necessary parts for servicing.
A wide range of optional extras is available to further improve the performance of TwinAir units and to meet specific application requirements. Standard options include: OilTronix: this guarantees virtually no water in the compressed-air system, thereby ensuring extended air-end life; FuelXpert: this offers significant fuel savings at partial loads for best-in-class efficiency; Cold-weather equipment: an Eberspacher fuel heater is available for starting at temperatures down to –25°C (–13°F), together with larger batteries, 5W40 engine oil and Paroil S compressor oil; and COSMOS: this comprehensive service and maintenance system pinpoints the exact location of the unit and indicates when servicing is required.
Atlas Copco Portable Air Division, PO Box 102, B2630 Aartselaar, Belgium; tel: +32 3 870 21 21; fax: +32 3 450 62 00.