New polyethylene piping system from Kingfisher
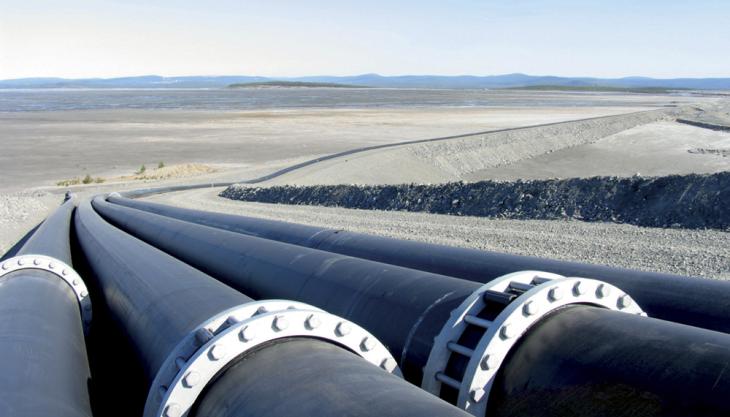
K-Pipe WRP solution offers abrasion-resistant lining and longer service life
KINGFISHER have introduced K-Pipe WRP, a polymer-lined, high-density polyethylene (HD-PE), abrasion-resistant piping system designed for the movement of liquids, sludge and slurry containing abrasive media and contaminants.
The piping system features an inner wear-resistant polymer within its matrix that improves the service life of the pipe when exposed to abrasion. K-Pipe WRP is manufactured via an automated extrusion process that incorporates a traditional HDPE outer sleeve and fuses an inner wear-resistant polymer sleeve, using a patented technology that eliminates the potential for delimitation in service.
According to Kingfisher, this results in a less expensive system than the traditional range of metallics and ceramics used for handling abrasive materials, such as ash, coal and minerals.
John Connolly, managing director of Kingfisher, explained: ‘This is an ideal addition to our range, as it allows us to provide a customized solution to individual applications. The benefits of K-Pipe WRP include: a degree of wear resistance; being lighter than traditional steel-lined pipes; and easy installation. We believe this system will add significant value to a host of applications within the utilities, manufacturing and process industries.
The HDPE system allows extra thickness of the wear-resistant inner polymer to be used in areas such as bends and branches where the abrasive effects of the media are most likely. Another advantage of K-Pipe WRP is that it can be joined using a specially developed butt-fusion technology and electro-fusion couplings, resulting in welded joints as strong and as smooth as the pipe itself.