Metso Minerals help shift waste mountains
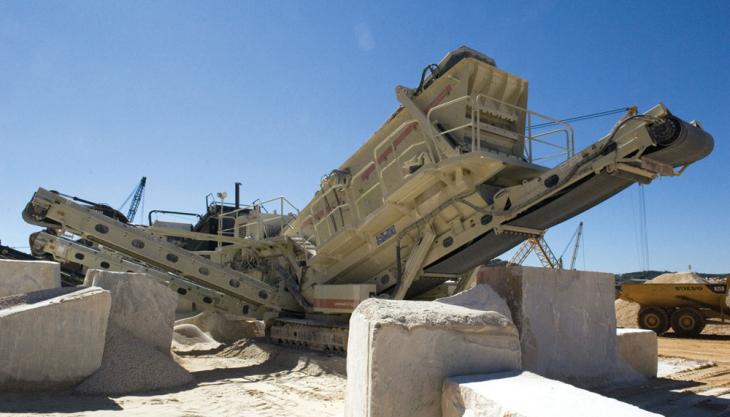
Marble producers are facing an environmental challenge caused by the continuously growing mountains of waste marble at their quarry sites. To tackle this problem, the biggest producer of the world-famous Rosa Portugal marble, Marmetal S.A., who operate four quarries at Borba and Viana do Alentejo, near the highway connecting Lisbon and Madrid, recently began to recycle their waste stockpiles using new-generation Metso Minerals Lokotrack mobile crushing and screening equipment.
‘Today, environmental aspects are becoming more and more important to us, and new regulations issued by the European Union must be met. Therefore, as one of the first marble producers in Portugal to do so, we have decided to begin solving this waste marble challenge ourselves,’ explained José Delgado, managing director of Marmetal S.A.
According to Mr Delgado, there are several applications for recycled marble, such as filler material for industrial use, cosmetics industry applications, fertilizer for agriculture, roadworks, concrete aggregate and landscaping material.
‘Our objective is to create an environmentally friendly recycling process and make a profitable business out of it. We foresee a good market in the Extremadura region in Spain, where we will sell 30–40% of the recycled materials. In addition, the new high-speed train track between Madrid and Lisbon requires large quantities of the kinds of aggregates that we can produce from the waste marble,’ he said.
The crushing and screening process for the marble is built around a new-generation Lokotrack LT1415S mobile impactor equipped with a detachable screen module, and an ST620 mobile screen. Mobile equipment was chosen for ease of movement between the company’s four quarries.
The waste marble is first reduced by hydraulic hammer to a size of around 800mm, suitable for loading into the LT1415S’s crusher cavity, which is operated with a closed-side setting of 60mm. The first screen deck of the LT1415S’s screen module is set to 120mm, with any oversized material returned to the impact crusher by the return conveyor. The –120mm +40mm product is separated via the side conveyor and sold for use in drainage projects.
Meanwhile, the –40mm fraction is conveyed to the ST620 mobile screen, which produces four end products: –4mm, –12mm +4mm, –20mm +12mm and –40mm +20mm, and sometimes –31.5mm for use as roadbase.
During its first few months in operation, the mobile process has achieved an average capacity of around 200 tonnes/h. However, when fine-tuned, José Delgado believes that 300 tonnes/h can be reached. ‘So far we have processed over 150,000 tonnes of waste marble, and we plan to achieve annual production of over 300,000 tonnes,’ he said.
‘We are happy with the availability and capacity of the equipment, and achieve very nicely shaped end products with the impact crusher. We are confident that, little by little, our existing waste marble mountain will disappear, thanks to the Lokotrack fleet.’
Meanwhile in Germany, one company making a profitable business out of clearing up what others throw away is Stork Umweltdienste. Headquartered in Magdeburg, a city that for 40 years was part of communist East Germany, Stork’s entrepreneurial owner, Bernd Stork, believes that sorting and reprocessing special wastes is becoming increasingly important in the country, especially in the new German states, which since reunification in 1990 have been striving to modernize their work practices.
Stork have been active in the area of land reclamation and contaminated debris processing since 1994 and are currently responsible for the reprocessing of hot slag and grate ash from a waste-burning plant in nearby Rothensee, dealing with around 8,000 tonnes of the rock-like material each month.
The company manage this task using a combination of mobile and stationary equipment. First, the slag – which comes in a variety of shapes and sizes (as well as differing materials) – is collected from the waste-burning plant so that it can be cooled down in temporary storage areas for at least 14 days. Once at a manageable temperature, it is initially screened into two sizes and then fed into a Lokotrack LT1110S mobile primary impactor.
The LT1110S used by Stork is an independent unit that can produce one precisely calibrated end product in a closed circuit or two products using an open circuit. The machine is built around the Nordberg NP1110M impactor, which is designed to crush any medium-hard rock or rock-based recycled material.
As part of the transformation of the unprocessed slag into marketable construction fill material, Stork separate any metals present in the slag. According to Mr Stork, jaw crushers were tried first, but these were found to be unsuited to the task, whereas the LT1110S breaks up aluminium, copper, brass, and iron fragments on the first pass.
Another advantage of the Lokotrack machine is its hydraulic reciprocating screen, which allows it to eliminate two particles sizes simultaneously. Using this, the plant is successfully separating stainless steel, aluminium, copper, and non-ferrous metals from the otherwise unpromising looking slag.
Following further processing in six static crushers, the commercially viable recycled slag material is stored in an 8,000m2 room for a further period of cooling, after which it can be sold on for reuse as sub-base material for roads or as a cover for refuse dumps.
In recent years, the reprocessing of construction and demolition waste has become another important area of Stork’s business and, when not required for slag processing duties, the easy to transport and quick to set up Lokotrack LT1110S can often be seen working at demolition sites in Magdeburg’s nearby city centre.
Metso Minerals, Crushing and Screening, PO Box 306, FIN 33101 Tampere, Finland;
tel: +358 20 484 142; fax: +358 20 484 143.
‘Today, environmental aspects are becoming more and more important to us, and new regulations issued by the European Union must be met. Therefore, as one of the first marble producers in Portugal to do so, we have decided to begin solving this waste marble challenge ourselves,’ explained José Delgado, managing director of Marmetal S.A.
According to Mr Delgado, there are several applications for recycled marble, such as filler material for industrial use, cosmetics industry applications, fertilizer for agriculture, roadworks, concrete aggregate and landscaping material.
‘Our objective is to create an environmentally friendly recycling process and make a profitable business out of it. We foresee a good market in the Extremadura region in Spain, where we will sell 30–40% of the recycled materials. In addition, the new high-speed train track between Madrid and Lisbon requires large quantities of the kinds of aggregates that we can produce from the waste marble,’ he said.
The crushing and screening process for the marble is built around a new-generation Lokotrack LT1415S mobile impactor equipped with a detachable screen module, and an ST620 mobile screen. Mobile equipment was chosen for ease of movement between the company’s four quarries.
The waste marble is first reduced by hydraulic hammer to a size of around 800mm, suitable for loading into the LT1415S’s crusher cavity, which is operated with a closed-side setting of 60mm. The first screen deck of the LT1415S’s screen module is set to 120mm, with any oversized material returned to the impact crusher by the return conveyor. The –120mm +40mm product is separated via the side conveyor and sold for use in drainage projects.
Meanwhile, the –40mm fraction is conveyed to the ST620 mobile screen, which produces four end products: –4mm, –12mm +4mm, –20mm +12mm and –40mm +20mm, and sometimes –31.5mm for use as roadbase.
During its first few months in operation, the mobile process has achieved an average capacity of around 200 tonnes/h. However, when fine-tuned, José Delgado believes that 300 tonnes/h can be reached. ‘So far we have processed over 150,000 tonnes of waste marble, and we plan to achieve annual production of over 300,000 tonnes,’ he said.
‘We are happy with the availability and capacity of the equipment, and achieve very nicely shaped end products with the impact crusher. We are confident that, little by little, our existing waste marble mountain will disappear, thanks to the Lokotrack fleet.’
Meanwhile in Germany, one company making a profitable business out of clearing up what others throw away is Stork Umweltdienste. Headquartered in Magdeburg, a city that for 40 years was part of communist East Germany, Stork’s entrepreneurial owner, Bernd Stork, believes that sorting and reprocessing special wastes is becoming increasingly important in the country, especially in the new German states, which since reunification in 1990 have been striving to modernize their work practices.
Stork have been active in the area of land reclamation and contaminated debris processing since 1994 and are currently responsible for the reprocessing of hot slag and grate ash from a waste-burning plant in nearby Rothensee, dealing with around 8,000 tonnes of the rock-like material each month.
The company manage this task using a combination of mobile and stationary equipment. First, the slag – which comes in a variety of shapes and sizes (as well as differing materials) – is collected from the waste-burning plant so that it can be cooled down in temporary storage areas for at least 14 days. Once at a manageable temperature, it is initially screened into two sizes and then fed into a Lokotrack LT1110S mobile primary impactor.
The LT1110S used by Stork is an independent unit that can produce one precisely calibrated end product in a closed circuit or two products using an open circuit. The machine is built around the Nordberg NP1110M impactor, which is designed to crush any medium-hard rock or rock-based recycled material.
As part of the transformation of the unprocessed slag into marketable construction fill material, Stork separate any metals present in the slag. According to Mr Stork, jaw crushers were tried first, but these were found to be unsuited to the task, whereas the LT1110S breaks up aluminium, copper, brass, and iron fragments on the first pass.
Another advantage of the Lokotrack machine is its hydraulic reciprocating screen, which allows it to eliminate two particles sizes simultaneously. Using this, the plant is successfully separating stainless steel, aluminium, copper, and non-ferrous metals from the otherwise unpromising looking slag.
Following further processing in six static crushers, the commercially viable recycled slag material is stored in an 8,000m2 room for a further period of cooling, after which it can be sold on for reuse as sub-base material for roads or as a cover for refuse dumps.
In recent years, the reprocessing of construction and demolition waste has become another important area of Stork’s business and, when not required for slag processing duties, the easy to transport and quick to set up Lokotrack LT1110S can often be seen working at demolition sites in Magdeburg’s nearby city centre.
Metso Minerals, Crushing and Screening, PO Box 306, FIN 33101 Tampere, Finland;
tel: +358 20 484 142; fax: +358 20 484 143.